デジタル流量計とは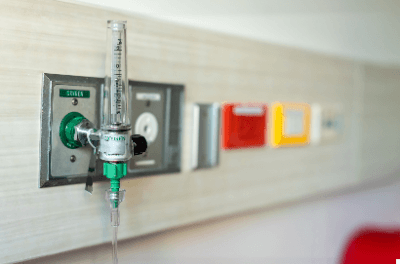
デジタル流量計(英語:Digital flow meter)とは、流量計で計測した結果をデジタル信号で送信する流量計です。ちなみに、流量計とは、気体・液体・蒸気などの流体の、単位時間あたりに質量や体積を計測する計器のことです。
流量計で計測された流量値は、流体が流れているため常に変化しています。この連続した計測値のアナログ数値をデジタル数値に変換し伝送する計器になります。流量計本体に、指示計と発信器(デジタル信号伝送器)を付属しているものや、指示計と発信器が別になっているものがあります。
デジタル流量計の使用用途
デジタル流量計の使用用途は、単に流量計して計測された瞬時の流量値を目視確認するだけではなく、流量値をデータとして各種制御機器へ伝送することで、制御システムで流量制御バルブを使用し流量制御を行ったり、出力された積算流量データを蓄積して消費量を監視したりすることができます。
また、流量の上限・下限値を監視し警報を発報・表示し、制御システムにより流体の流れを閉止することができます。
したがって、各種プラントや流体を使用する製造現場において、流量データを使用して自動化し制御するような場合で多く使用されています。
デジタル流量計の原理
デジタル流量計の原理は、一例としてタービン式流量計では、管路内に設置した羽根車(ロータ)を流体により回転させ、羽根車に取り付けられた磁石が回転します。この磁石は流速に比例して回転するし、回転数はピックアップコイル(非接触で本体内にあるリードスイッチ素子)で検出され、変換器で遠隔伝送に適するパルス列信号に変え出力されます。
このパルス信号(デジタル信号)を都度出力し、一定時間間隔(例:1回から100回/秒)ごとにデジタルの数値としてサンプリング(計測時間と計測値をデータとして抽出すること)します。サンプリングされたデジタルデータを計測時間情報ともに伝送出力したり、デジタルデータを移動平均処理したり、積算処理をして出力したりしています。
最近では、マイクロプロセッサを搭載し、検出・記憶・演算の他、判断・通信機能を有し、フィールドバス(双方向で信号のやり取りができるデジタル通信方式)に対応したインテリジェントタイプの伝送器を付属しているものもあります。
このようなデジタル発信器を使用することにより、正確な数値や情報をもとに流体の制御を行うことができるようになり、プロセス制御の可能性が広くなります。