黒染め加工とは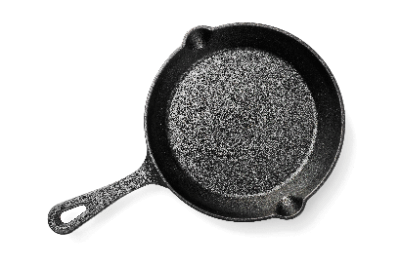
黒染め加工 (英: blackening) とは、金属の防錆などを目的とした表面処理法です。
アルカリ性の薬液で金属を煮沸することにより表面を酸化させ、黒色の被膜を形成します。 黒染め加工は、主に鉄鋼製の部品の防錆加工に用いられます。
黒染め加工のメリットは、被膜が非常に薄く、元の金属の寸法精度の変化が少ない点です。 耐摩耗性や保持性に優れ、薬液の廃棄も不要なため環境にも優しいです。 メッキ加工に比べて低いコストで防錆処理できる点も長所といえます。
一方で、黒染め加工のデメリットは、薬液の特性上、黒色にしか加工できないことです。 メッキ加工や塗装のように、他の部品と色を合わせることは基本的にできません。 防錆性を維持するために、防錆剤を塗布する必要がある点も注意が必要です。
黒染め加工の使用用途
黒染め加工には、防錆性の向上、見栄えの向上、反射防止などを目的とした使用用途があります。
1. 防錆性の向上
黒染め加工の本質的な用途は、黒色の被膜を作ることで防錆性を向上させることです。加工前と後で、寸法精度がほぼ変わらない特徴に加え、加工コストも比較的低いためさまざまな用途で活用されます。
2. 見栄えの向上
黒染め加工により生じた落ち着きのある黒色は、高級感があるため、デザイン性を高める用途に使われます。 工業製品だけではなく、インテリアやアート作品に用いられる場合もあります。
3. 反射防止
黒色加工後の金属部品は光沢が抑えられるため、反射を防止する用途でも使われます。 製造機械などの目に見える部品の光反射を防止することで、作業者のストレスを緩和することが可能です。
4. 潤滑性向上
黒染め加工を行った鉄鋼材は耐摩耗性が向上し、防錆剤の効果で潤滑性も良化します。
黒染め加工の原理
黒染め加工は、鉄鋼材を苛性ソーダ成分があるアルカリ溶液に入れて、140~150℃の温度で15~20分程度加熱処理し、表面を黒色の錆で覆う工法です。この黒錆びの成分は、四酸化三鉄 (Fe3O4) であり、安定した不働態の被膜です。これにより、鉄鋼の赤錆を防止して防錆性が向上します。
黒染めの被膜厚さは1~2µm程度のため、寸法精度の影響が少ない加工です。表面の化学反応処理であり、メッキや塗装のように、はがれることはありません。また、耐摩耗性や含油性があるのも長所です。表面がポーラス状で防錆剤が保持されます。
黒染め加工は加熱温度が低いので、材料強度や材料特性への影響が少ない長所があります。
黒染め加工の種類
黒染め加工は、「黒色メッキ加工」と呼ぼれることもありますが、基本的な方法や仕上がりは同じです。 同様に、「フェルマイト処理」「SOB処理」「アルカリ処理」と呼ばれる加工方法も、黒染め加工との違いはありません。
使われる薬剤の調合や設備によって色味に違いはありますが、黒染め加工自体に種類の分別はないといえます。
黒染め加工のその他情報
黒染め加工に使用する薬剤
黒染め加工の各工程で、使用する薬剤があります。
1. 脱脂工程
脱脂工程では、水溶性アルカリ脱脂材が使用されます。非イオン界面活性剤の水溶性脱脂・洗浄剤であり、不燃・無臭です。塩素化合物溶剤と同等の強力な脱脂・洗浄力があります。また、排水する時は、アルカリ濃度が低いので、中和用稀硫酸を使用します。
2. 錆取り工程
鉄錆・スケール除去剤を使って錆取りを行います。塩酸に、錆びやスケール除去を促進する酸、安定化する界面活性剤、水素脆化やオーバーピーリングを防止する抑制剤等を添加したものです。
3. 黒染め工程
黒染めには、加温黒染め剤が使われ、鋼材を漆黒の四三酸化鉄被膜で覆います。赤味を帯びがちだった鋳物や、特殊鋼も漆黒に仕上げが可能です。米国防省MIL規格 、米国航空宇宙材料規格、国際標準化機構規格、ドイツ工業規格などに適合した薬剤です。
4. 防錆工程
黒染め後、防錆剤を使用します。水置換性の中期防錆剤であり、水置換性に優れ、濡れた状態の部品や湿度の高い環境下での防錆処理に適しています。防錆の目安期間は、6~12か月です。