押出成形機とは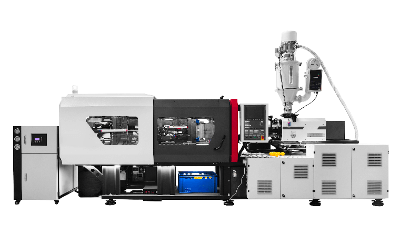
押出成形機とは、投入された原料を加熱により軟化し、シリンダのスクリューで押し出すことで、チューブやシートといった成型品を生産する装置です。
ペレット状やミンチ状の原料から、ダイの形状に応じて丸形や角型のパイプやチューブ、ダクト、シート状といった種々の形状へと加工します。原料はホッパーから逐次投入されているため、連続的な生産が可能です。大量生産する際に重宝されています。
押出成型はダイで形状を与え、水冷や空冷といった冷却工程で硬化させることで形状を保持します。十分硬化した状態で引き取られ、切断されることで製品となります。押出成形の歴史は長く、用途も食品加工から金属・プラスチック成型まで幅広いです。
押出成形機の使用用途
押出成形機はアルミニウム、銅のような金属や熱可塑性のプラスチック原料を、一度加熱溶融した後にダイによって形状を与え、成型品へと加工する際に使用されます。プラスチックを原料とする合成繊維の製造を例にすると、押出機出口から得られた溶融プラスチックを冷却しながら、引き延ばすように引き取ることで、ストランド状のプラスチックが得られます。
また、押出成型機は発泡体の連続生産も可能です。溶融した樹脂に発泡剤を圧入することによって溶融させます。ダイ出口から常圧に押し出される際に、圧力差によって発泡剤が抜けていくので発泡体が得られます。
工業分野以外に、ソーセージ、パスタやビーフン、ペットフードといった食品の加工も押出成形機の用途の一つです。押出成形機では、蒸気を加えて熱することが可能で、食品中の微生物を軽減し、でんぷんの糊化も同時に行うことができます。
押出成形機の原理
押出成形機の役割は、溶解させた原料に形状を与えるというシンプルなものに見えます。しかし、安定した製品を作るためには、原料や目標とする形状に応じて、各所の条件を最適化することが重要です。
まず、ホッパーに投入された原料を目詰まりを起こさないよう重量フィーダーなどを用いて一定の速度に調節して、シリンダに原料を充填していきます。 シリンダのヒーターで原料を加熱して柔らかくし、スクリューのスピードを調節しながら、適切な圧力をかけながら押し出すことで、チューブ状や棒状といった目的の形状を得ることが可能です。
押出物は冷却装置で形状が保持できるほど十分に冷やされた後、引き取られて切断されます。重要となるのは、各工程における温度管理です。押し出した材料の温度が高すぎると、粘度が高く冷却に時間を要するため、ダイ出口で与えた形状が保持できない恐れがあります。
また、冷却工程においても、冷却速度が早すぎると、成型品にひずみが生じるため、破断の原因になりかねません。押出機の加熱はヒーターからの加熱に加えて、スクリュと材料や材料同士間で生じる摩擦熱も発生します。
そのため、設定温度と実際の温度をモニタして、装置が自動で調整した場合でも、温度の振動 (ハンチング) が生じてしまいます。
押出成形機の種類
押出成形機は、押出機の構造やダイの形状、また後処理方法によって分類されます。さらに、押出機はスクリュの本数によって、一軸方式と多軸方式にわけることができます。
原料が複数の場合、溶融だけではなく、均一な混錬が求められるため、混錬性能の高い多軸の押出機が用いられることが多いです。原料に応じて、スクリュの構成や回転方向を決める必要があります。
原料の成型品の形状は、押出機のダイと呼ばれる口金の形によって大きく決まります。そのため、押出成型の種類は、このダイの形状や後工程によって呼びわけされることが多いです。代表的な成型として、チューブ状や棒状、シート状が挙げられます。
スタンダードな形状の他にも、複雑な形状に成型したり、多層化した成型品も得たりすることができます。また、発泡剤を投入することで押出発泡品も製造可能です。
参考文献
https://www.keyence.co.jp/ss/products/sensor/plastic-molding/glossary/#die