超硬エンドミルとは
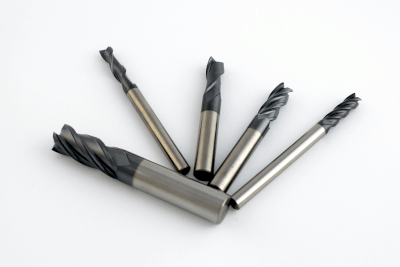
超硬エンドミルとは、工作機械で使用する切削工具の一種です。
非常に硬くて耐摩耗性に優れた超硬質材料で作られています。超硬エンドミルは金属や非金属の材料を加工する際に使用され、高い精度で加工できます。超硬エンドミルの主な材質は、カーバイドやコバルト合金、ダイヤモンド、立方晶窒化ホウ素 (CBN) などの超硬質材料です。
これらの素材は通常の鋼や切削工具よりもはるかに硬く、耐摩耗性や耐熱性に優れています。超硬エンドミルの切削刃は、一般的に高速回転で切り込みます。この高速回転は、高速度加工のために非常に重要です。
超硬エンドミルの使用用途
以下は超硬エンドミルの代表的な使用用途の一部です。
1. 金属加工
鋼材の切削、アルミニウムの溝切り、銅や真鍮の加工など
2. 金型加工
プラスチック成形用の金型やプレス金型の加工など
3. 造船・船舶部品製造
船体や舵の形状加工、ネジ穴の開け方向、船舶部品の切削など
4. 自動車産業
エンジン部品の切削、歯車の切削、車体部品の穴あけなど
5. 航空産業
航空機のフレーム加工、エンジン部品の切削など
6. 電子機器製造
基板の穴あけや加工、マイクロチップの製造など
7. 医療機器製造
人工関節や歯科インプラントの形状加工、医療用器具の穴あけなど
超硬エンドミルの原理
超硬エンドミルは、切削工具の一種であり、フライス盤やCNCマシンなどの工作機械で使用されます。超硬エンドミルが切削する一般的な過程は以下の通りです。
1. 位置調整
超硬エンドミルを工作機械のスピンドルに取り付けます。切削する材料を正確に配置し、超硬エンドミルの先端を材料の表面に適切な位置に配置します。
2. 切削条件の設定
切削する前に切削条件 (回転数や送り速度、切削深さなど) を設定します。材料の性質や切削目的に応じて、最適な切削条件を選択します。
3. 切削開始
切削条件を設定したら超硬エンドミルを回転させます。エンドミルは材料の表面に接触し、切削が始まります。
4. 切削液の使用
切削過程中に切削液が使用されることがあります。切削液は冷却や潤滑の目的で使用され、切削時に発生する熱や摩擦を軽減します。切削液は加工物や切削工具に供給され、品質の向上と切削工具の寿命の延長に効果的です。
5. 切削とチップの排出
超硬エンドミルの刃部分が材料を削り取ります。切削時にはチップ (切りくず) が発生しますが、エンドミルの刃部分の形状の効果でチップは効果的に排出され、切削面が形成されます。
6. 切削領域の移動
切削が進むにつれて、超硬エンドミルと工作機械の制御システムによって加工領域を移動させて切削します。超硬エンドミルは、直線的な移動や回転、曲線的な軌道など様々な動きができ、必要な切削が完了するまで、超硬エンドミルの移動と切削が継続されます。
7. 切削終了
切削が終わったら,切削過程で発生したチップや削りくずを除去します。
8. 切削結果の確認
加工物の寸法や形状、表面状態などを確認します。必要に応じて修正・仕上げ作業を行います。
9. エンドミルのメンテナンス
超硬エンドミルを清掃したり研磨したりします。また残り寿命を確認したり、必要に応じて交換したりします。
超硬エンドミルの種類
超硬エンドミルにはさまざまな形状と特性を持つ種類があり、以下に代表的な超硬エンドミルの種類を挙げます。メーカーによって名称が異なる場合があります。
1. フラットエンドミル(平刃エンドミル)
底面が平らな刃先を持ち、直線的な切削を行うための一般的なエンドミルです。一般的な加工や溝切りなどに使用されます。
2. ボールエンドミル
球状の刃先を持ち、曲線的な切削や凹凸面の加工に使用されます。円形の切削面を作成したり、曲線の形状を形成したりするのに適しています。
3. コーナーラジアスエンドミル
刃先に丸み (コーナーラジアス) を持ち、角やエッジのある加工に使用されます。フラットエンドミルよりも滑らかな曲線を形成できるため、表面仕上げや複雑な形状の加工に適しています。
4. Tスロットエンドミル
T字型の刃先を持ち、Tスロットや溝などを形成するために使用されます。工作機械のテーブル上でボルトやナットを固定するためのスロットを作成するのに適しています。
5. その他
フェースミル、ホールミル (ドリルエンドミル) などがあります。
超硬エンドミルの特徴
1. 長所
超硬エンドミルの主な長所は「高い硬度と耐摩耗性」、「優れた切削性能」、「多様な材料に適用」、「高い精度と品質」、「長寿命と経済性」です。以下にて説明します。
高い硬度と耐摩耗性
超硬エンドミルは非常に硬度が高い工具であり、硬い材料や難削材料を効果的に切削できます。また耐摩耗性も高いため長時間の使用にも耐えられ、切削性能を維持できます。
優れた切削性能
超硬エンドミルは鋭い切削刃を持っていて切削性能が優れているため、高速かつ精密な切削が可能であり生産性が高くなります。また微細な加工や複雑な形状の切削にも対応できます。
多様な材料に適用
超硬エンドミルは、金属やプラスチック、セラミックスなど、様々な硬度や特性を持つ材料を加工できます。また異なる切削条件や刃先の選択により、材料に最適な切削性能を発揮できます。
高い精度と品質
超硬エンドミルは高い剛性を持っていて加工時の振動や歪みを最小限に抑えられるため、精密な加工が可能であり加工品質が高くなります。また切削時の切りくずが少ないため、加工表面の品質が向上して滑らかで精密な仕上がりになります。
長寿命と経済性
超硬エンドミルは耐摩耗性に優れていて寿命が長くなるため、交換頻度が少ないことが利点です。作業を中断する回数が減り、また交換用の超硬エンドミルを購入する頻度が減るためコストの削減につながります。また高い切削性能と耐久性により、生産性が向上し経済的な加工が可能です。
2. 短所
超硬エンドミルの主な短所は「高コスト」、「脆性」、「切削速度の制限」、「加工できない材料」、「切削液の必要性」です。以下にて説明します。
高コスト
超硬エンドミルは高度な材料と製造工程が必要であり、他の一般的な切削工具に比べて価格が高くなるため、初期投資や交換コストが高いことが短所です。
脆性
超硬エンドミルは非常に硬い材料であり、脆い性質を持っています。誤った使用や衝撃、過剰な負荷などが加わると、エンドミルの刃先が欠けたり破損したりする可能性があるため取り扱いには注意が必要です。
切削速度の制限
超硬エンドミルは高硬度材料を切削ができますが、切削速度が制限されることがあります。特に大径の切削や硬い材料の加工においては適切な切削速度を維持することが難しい場合があり、加工時間が増加する可能性があります。
加工できない材料
超硬エンドミルは多様な材料に対応できますが、非常に脆弱な材料や熱に敏感な材料に対しては、使用が制約される場合があります。これらの材料では、エンドミルの寿命や加工品質に悪影響を及ぼす可能性があります。
切削液の必要性
超硬エンドミルでの切削時には、切削液の使用が推奨されます。切削液は冷却や潤滑の役割を果たし、切削時の摩擦や熱を制御しますが、切削液を使用すると環境への影響を配慮する必要があり、その管理や廃棄物処理が必要となることが短所として挙げられます。
超硬エンドミルのその他情報
超硬エンドミルの刃先に使用される材質
一般的に超硬エンドミルの刃先材質には、タングステンカーバイド (Tungsten Carbide) とコバルト (Cobalt) から構成されるものが使用されます。
タングステンカーバイドは、タングステンと炭素の化合物であり、非常に硬い材料です。非常に高い硬度と耐久性を持ち、切削時の高い熱および摩耗にも耐えられます。しかしタングステンカーバイド自体はもろくて衝撃や振動に弱いため、刃先材質として単独では使用されず、コバルトなどの金属がバインダーとして使用されます。
コバルトはタングステンカーバイドと結合し、刃先を強固に保持するバインダーです。コバルトは硬くて摩耗に強い性質を持っており、タングステンカーバイドと組み合わせることで、エンドミルの刃先に必要な強度と耐久性が備わります。またコバルトはタングステンカーバイドと比較して比較的柔らかいため、切削時の衝撃や振動を吸収することも可能です。
タングステンカーバイドとコバルトの組み合わせにより、超硬エンドミルは高速での切削や硬い材料の削り取りに優れた性能を発揮します。刃先材質は、切削条件や材料の種類に合わせて選択され、例えば硬度の高い材料を切削する場合には、より硬いタングステンカーバイドの割合を増やすことが一般的です。また切削速度や切削力の要求に応じて、刃先材質の組成を調整することもあります。
さらに刃先の形状やコーティングも切削性能に影響を与えます。例えば刃先にチップ状の交換可能なカッターを使用すれば、刃先の磨耗が生じた場合には交換が容易です。また刃先に特殊なコーティングを施すことで、摩擦を低減し、切削時の熱や摩耗を軽減する効果があります。