六角穴付き皿ボルトとは
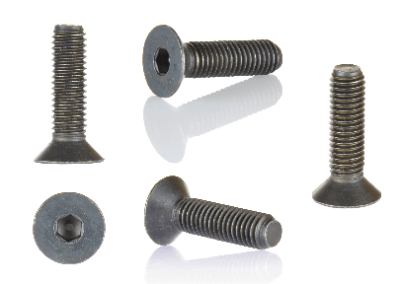
六角穴付き皿ボルト (英: Hexagon Socket Flat Head Bolt, Hexagon Socket Countersunk Head Screws) とは、ボルト頭部の形状がねじ側にテーパー状の円すい形で、上端面に六角形状の穴があけられているボルトです。
横から見ると皿のような形状をしています。締め付けは六角レンチを使用し、頭部上面に六角穴に差し込み使用します。
一般的な総称として、「皿ボルト」も同義語です。六角穴付き皿ボルトの形状は、ネジの呼び径が同じであれば、皿小ねじと同じですが、六角穴付き皿ボルトは皿小ねじより大きい呼び径があります。
なお、六角穴付き皿ボルトの規格は下記の通りです。
- JIS B 1194 六角穴付き皿ボルト
- ANSI/ASME B 18.3.5M Metric hexagon socket countersunk head screws
六角穴付き皿ボルトの使用用途
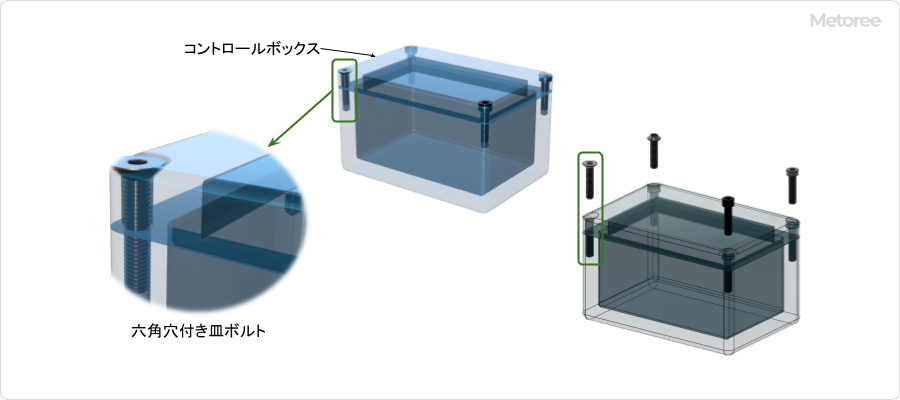
図1. 六角穴付き皿ボルトの使用例
六角穴付き皿ボルトは、主に取り付け作業のスペースが狭く、小さな機械や装置などへ部品を取り付け、固定するために使用します。
六角穴付き皿ボルトを取り付ける相手側に、ボルト頭部の円すい形より少し大きく、頭高さより少し深いザグリ穴あけを施工します。これにより、ボルト頭部は、完全にはみ出さずに取り付けることが可能です。
ボルト頭部と他部品との干渉を避け、すっきりとした状態になります。ボルト取り付け部の突出が無くフラットになるため、蝶番の取り付け部などに使用されています。
なお、ザグリ穴とは、ボルト頭部が隠れるように、取り付け部に穴あけ加工することです。
六角穴付き皿ボルトの原理
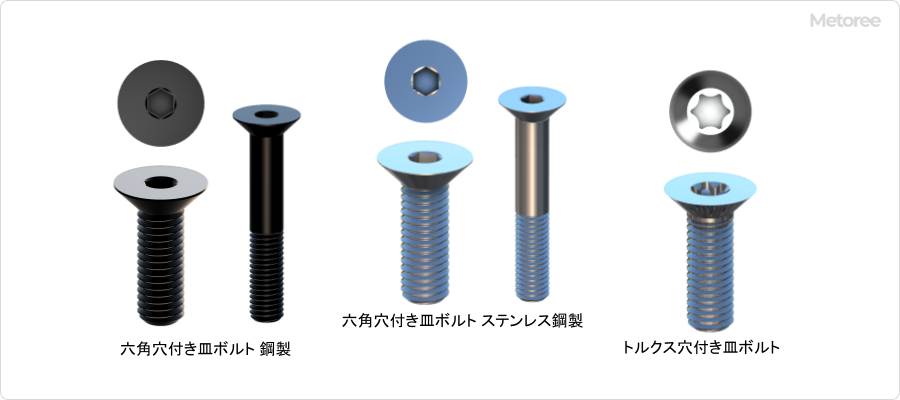
図2. 六角穴付き皿ボルトの原理
六角穴付き皿ボルトは、一般の六角ボルトと同じで、ねじ (この場合の「ねじ」は、スクリュー状の形状だけを示します) により締結します。六角穴付き皿ボルトは、ナットを使用して締結せずに、タップ加工したメスねじに直接ねじ込み締結する方法に多く使用されています。
六角ボルトのように、ボルト頭部にレンチをはめ込むのではなく、断面が六角状のレンチを六角穴に差し込み締め付けます。そのために、ボルト頭同士や他部品との間にスペースの確保が必要です。
しかし、六角穴付き皿ボルトの締め付け工具は、六角レンチのためボルト頭外側のスペースは不要で、密接して六角穴付き皿ボルトを配置することができます。その結果、小さい寸法で設計が可能でコンパクトな部品や装置が実現できます。
なお、六角穴付き皿ボルトの長さ表示は、ボルト頭部を含む全長で表されています。六角ボルトなど一般のボルトの長さは、ボルト頭部の高さを除きねじ部を含む軸部の長さで表されています。それぞれの長さ表示の違いは注意が必要です。
六角穴付き皿ボルトのその他情報
1. 六角穴付皿ボルトの主な材質と主な表面処理
六角穴付き皿ボルトの材質は、比較的強度区分の高い材質を使用しており、鋼製の場合 JIS B 1051 8.8, 10.9, 12.9、ステンレス鋼の場合 JIS B1054 A2-70, A2-50 を採用しています。高い締め付け力と高い強度が必要な場合に使用されています。
使用箇所や用途に適した材質や強度区分の選定が重要です。ステンレス鋼は、耐食性が求められる箇所に使用されます。
なお、ボルトの強度区分と材質は下記の通りになります。
鋼製
- 強度区分8炭素鋼 (焼き入れ・焼き戻し、合金元素で強化) 、S45C (熱処理で強化) など
- 強度区分8炭素鋼 (焼き入れ・焼き戻し、合金元素で強化) 、SNB7、SCM435
- 強度区分9合金鋼、SCM435、SCM440
- 強度区分9合金鋼、SCM435
ステンレス鋼製
- 強度区分 A2-50, 70 SUS304、SUS304L、SUS XM7
六角穴付皿ボルト材質選定において、電蝕を防止することは重要です。ボルトの材質と被締結物の材質が異なる場合、それぞれの金属間に電位差が生じて腐食することがあります。
特に、アルミやステンレスの場合は注意が必要です。六角穴付き皿ボルトの表面処理は、鋼製の場合、耐食性を目的として電気メッキ、無電解メッキ、アルマイト処理、黒染めなどの施工が一般的です。
2. 六角穴付皿ボルトの使用上の注意点
基本的な六角穴付皿ボルトを使用する際、注意するべき点は以下の2つです。
- 六角穴付皿ボルトと被締結物のねじ穴部が壊れないよう、締め付ける力が許容範囲内であること
- 六角穴付き皿ボルトと被締結物もねじ穴部に加わる、繰り返しの力 (振動などによる) が許容範囲内であること
3. 六角穴付き皿ボルトのゆるみ止め
皿ボルトや皿ねじは、一般的なボルトやナット、なべ小ねじ、フランジねじなどの座面が平らなねじと比較して、ゆるみやすいことが挙げられます。
六角穴付皿ボルトのゆるみ防止として、ゆるみ止め用接着剤の使用、ゆるみ止め施工されたボルトの採用などが有効的です。
4. 締め付け工具
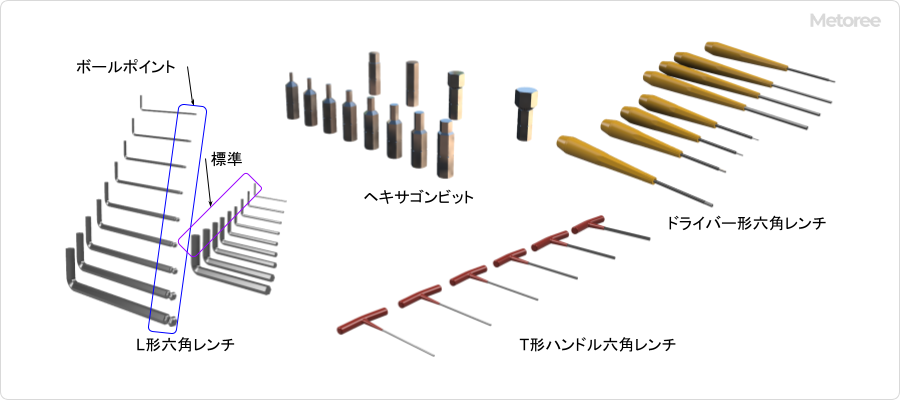
図3. 六角穴付き皿ボルト締め付け工具の種類と形状
六角穴付き皿ボルトの締め付けは、ボルトのサイズに合った六角レンチ (六角棒レンチ) などの締め付け工具を使用します。六角レンチは、スパナやモンキーなどと比較して、小さい力で強い締め付け力を加えることが可能で、締め付けるときにボルト周辺の作業スペースが狭くて済むなどのメリットがあります。
ただし、六角レンチには、ミリサイズとインチサイズがあり、六角レンチの選定には注意が必要です。締め付け工具の種類は、L形六角レンチ (六角棒レンチ) 、T形ハンドル六角レンチ、ドライバー形六角レンチ、ヘキサゴンビットなどがあります。
また、六角レンチとヘキサゴンビットの六角穴付き皿ボルト差し込み側の先端形状は、「フラット」と「ボールポイント」があります。ボールポイント先端の形状は、角部をR加工しているため、六角レンチが斜めの状態でも締め付けが可能です。
参考文献
https://www.urk.co.jp/contents/elements/element24.html
https://www.akaneohm.com/column/denshoku2/
https://www.nbk1560.com/