電球フィラメントとは
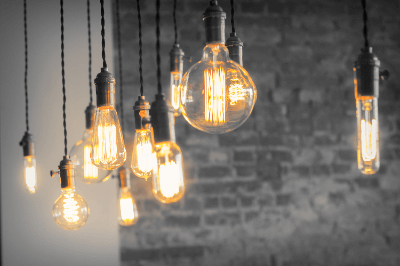
電球フィラメントとは、白球電球などの照明機器の発光する部分のことです。
ガラス球の内部にあり、細長い線状の形をしている抵抗体です。フィラメントは、電流が流れて加熱されることで発光します。
発明当初のフィラメントは、素材に炭化した紙が使用されていたため、炭素電球と呼ばれていました。しかし、約1分光るとすぐにフィラメントが燃えてしまい、普段の生活で使用できるレベルではありませんでした。
そこで、現在ではほとんどタングステンという金属が使用されています。
電球フィラメントの使用用途
電球フィラメントは、照明用電球の光源として使用されています。
1. 白熱電球
主な使用用途として、白熱電球が有名です。フィラメントの素材には、コイル状にした細いタングステン線が使用されます。しかし、最近の一般照明用電球では、熱を奪われにくくするために二重コイル状になっているものが多く使用されています。
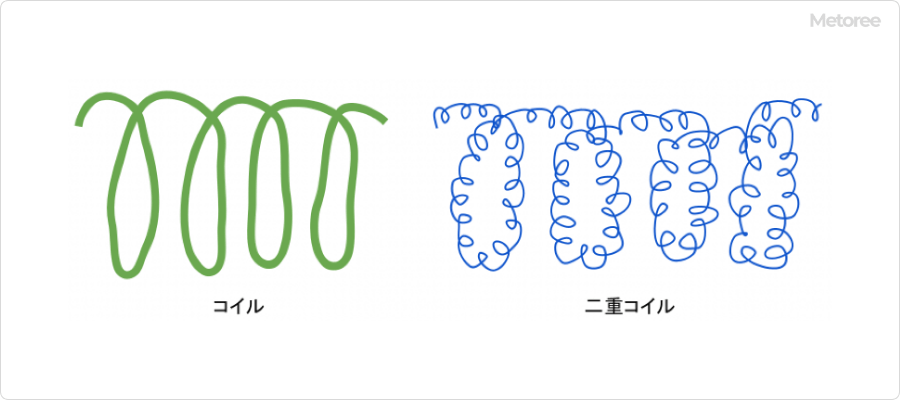
図1. コイルと二重コイル
白熱電球には、ハロゲン電球やミニクリプトン電球、蛍光電球などの様々な種類があります。ガラス球の内部には、フィラメントの蒸発を防ぐために不活化ガスが充填されています(例:アルゴン、窒素、クリプトン、キセノン)。
また内部が真空のものも存在し、白熱電球はガスの種類によって光の発色や強さが異なります。近年では、白熱電球はエネルギー効率が悪いという理由から、ハロゲン電球やミニクリプトン電球以外の白熱電球は生産が中止となっているものもあります。
またこのようなエネルギー効率の観点から、最近ではLED(Light Emission Diode)と呼ばれる発光ダイオードが使用されることが多くなっています。
2. フィラメントLED電球
フィラメントLED電球とは、フィラメントをLEDで再現した電球のことです。フィラメントLED電球は、明るさが暗いという特徴があります。
理由は、細長い糸状のLEDを用いているからです。また、ヒートシンクと呼ばれる放熱部分を持たない機種が多く存在します。そのため、あまりパワーの大きいLEDを使用できないというデザイン上の制約もあります。主な用途として、補助的な照明や関節照明に使用されています。
一方、一般的なLED電球は大きなLEDチップを使用できるため、フィラメントLED電球より明るいものが多く作られています。
フィラメントLED電球の寿命は、白熱電球や蛍光灯電球より長いが、一般的なLED電球より短い長さです。具体的には15,000時間前後です。一般的なLED電球が30,000〜40,000時間であるため、約半分の寿命となります。
電球フィラメントの原理
白熱電球は、フィラメントに電流を流してジュール熱を発生させ、熱放射して発光する原理を用いています。ジュール熱とは、導体に電流を流した時に発生する熱エネルギーのことです。
したがって、長時間利用可能な電球にするためには、フィラメントは抵抗が強く、熱に強い素材である必要があります。そうでないと、フィラメント自体が熱に耐えられずに燃えてしまい、光源として使えなくなってしまうためです。
タングステンは融点が3,653K(3,379℃)と非常に高く、金属元素の中では最高値です。したがって、ジュール熱によって高温になっても溶けることがありません。そのため、フィラメントにはよくタングステンが用いられるのです。
電球内部は不活性ガスが封入されていることで、電球は長寿命を保つことができます。しかし、不活性ガスはガス自体の熱伝導や対流により、フィラメントの熱を奪う動き(熱損失)もします。封入ガスと熱損失の関係は図2のように、原子量の大きい元素ほど熱損失が小さくなる傾向があります。
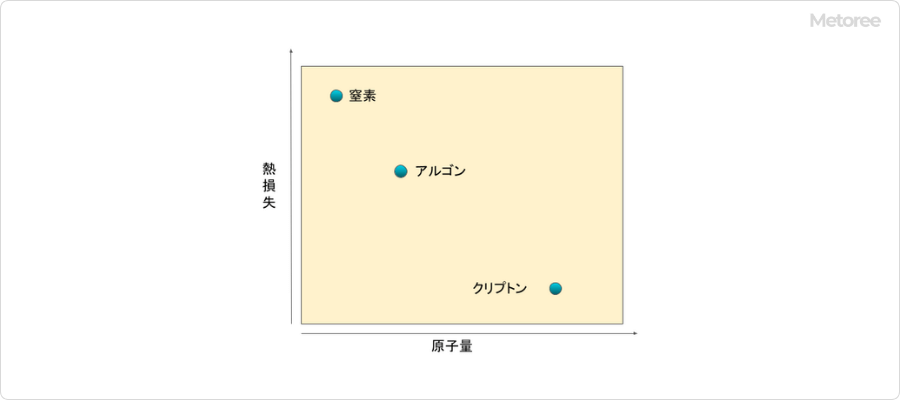
図2. 封入ガスと熱損失
電球フィラメントのその他情報
1. 竹のフィラメント
1879年、エジソンが実用的な白熱電球を発明しました。当時、フィラメント材料として使用されていたのは日本の竹でした。竹は繊維が太く、丈夫で長持ちするので、フィラメント材料に適していました。
電球開発当初、エジソンは木綿糸に煤とタールを塗って炭素化させたフィラメントを使用し、電球を40時間継続して点灯させることに成功しました。しかし、実用性を考慮すると、もっと長く点灯し続ける電球の開発が必要不可欠でした。
そのため、紙や糸などの身近にある様々な材料をフィラメントにして、点灯時間を調べる実験を繰り返しました。その過程で、日本からのお土産の扇子を見つけ、その骨組として使用されている竹をフィラメントにして電球をつくりました。
その電球で点灯実験を行うと、今までの材料よりも点灯時間が長くなり、実用性のあるレベルまで到達することがわかりました。その後、エジソンはフィラメントに最適な竹を探すために、世界中の様々な種類の竹を使って点灯実験を進めていきました。
そして、日本の京都産の八幡竹を使うと、平均1,000時間以上点灯し続けることがわかり、実用化するに至りました。
2. フィラメント糸とスパン糸
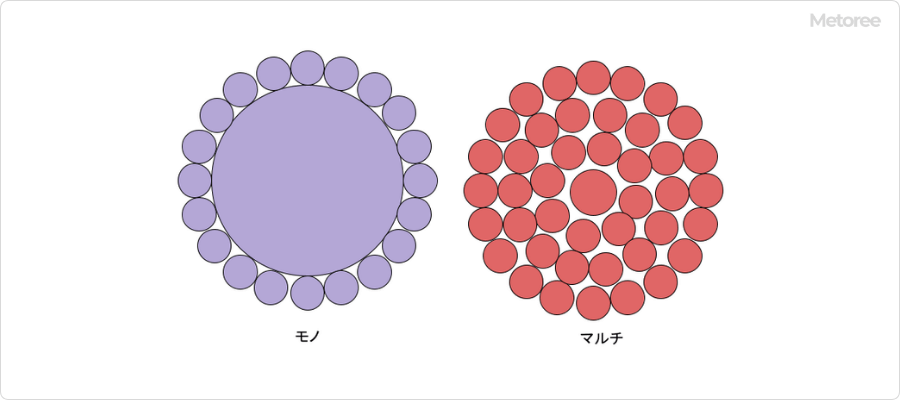
図3. モノフィラメントとマルチフィラメント
フィラメントという言葉は電球の光源部分を指すときに使用しますが、絹のように連続した長い繊維のことをフィラメント糸といいます。フィラメン
ト(英語: filament)は、元々繊維状のものを意味する英単語です。一方で、綿糸のように短い繊維同士を平行にしてそろえて、撚りを加えて一本の糸に紡績したものをスパン糸といいます。
フィラメント糸には、モノフィラメントとマルチフィラメントの2種類があります。前者は、釣り糸のように長い一本の糸のことをいいます。後者は、数十本の糸を撚り合わせて1本の糸にしたものをいいます。天然繊維では絹糸が該当します。蚕が吐き出した繭を解いたものが生糸、それをきれいにしたものが絹糸です。
スパン糸には、特に種類はありません。綿、麻などのほとんどの天然繊維が該当します。
参考文献
https://www.ushio.co.jp/jp/technology/glossary/glossary_ha/filament.html
https://www.ushio.co.jp/jp/technology/glossary/glossary_ta/tungsten.html
https://www.ushio.co.jp/jp/technology/glossary/glossary_ta/tungsten_filament_lamp.html
https://eguchi-hd.co.jp/enelabo-filament-edison/
https://www.cradle.co.jp/glossary/ja_S/detail0132.html
https://news.only-1-led.com/filament_led_info