砥石とは
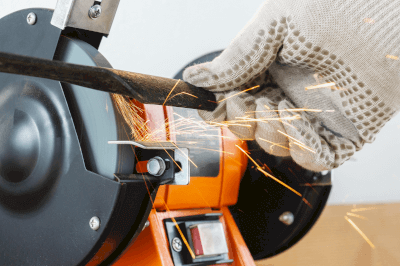
砥石は研削材料を砥粒 (粒子状の研削剤) に結合させて作られる工具です。一般的には、酸化アルミニウムやシリコンカーバイトなどの研削剤をバインダーに混ぜて固めて砥石の形状に成形しています。砥石は形状や粒度により多種類に分類されています。
砥石は主に金属加工において使用されますが、ガラス、セラミック、プラスチック、石材などの研磨にも使われます。また手動でも使用されますが、高速回転するモーターに取り付けられた研磨盤に装着して使用されることも多く、使用目的や機械の規格に適した砥石を選ぶことが必要です。
砥石の使用用途
1. 切削工具の研ぎ直し
切削工具には刃物の部分があり、使用すると刃が鈍くなってしまいます。砥石を使って刃を研ぎ直すことで、再び鋭い状態に戻せます。例えばナイフやノコギリやドリルビットや鋸やハサミや旋盤の切削工具などが挙げられます。
2. 金属製品のバリ取り
金属を切削する際に、切削部分の周囲にバリ(ガタつきや鋭利なとげ) が発生ことがあります。砥石を使ってバリを取り除けます。金属板やアルミ板やステンレスなどの加工品でよく使用されます。
3. 金属製品の磨き
金属の表面を滑らかにするために、砥石を使って磨けます。車やバイクのエンジンパーツや家具の金属フレームなどが挙げられます。
4. 切れ味の良い刃物の製作
砥石を使って新しい刃物を作れます。例えば日本刀や包丁やハサミやカミソリや剪定バサミなどです。
5. その他
その他にも、砥石は様々な用途に使用されます。例えば陶器の表面を研磨したり、磨きをかけていないステンレス鋼の表面を砥石で磨いたりして美しく仕上げられます。
砥石の原理
砥石の原理は「砥石の表面に固着している砥粒を加工対象物の表面に押し付けた状態で、回転運動や直線状の往復運動によって、加工対象物の表面を削り取ること」です。
1. 刃物の研磨
刃物の切れ味が悪くなった場合は砥石を使って研磨します。刃物を砥石に対して角度をつけて押し付けることで、砥石の表面に固着している砥粒が、刃物の切れ味を悪くしている鈍い部分を削り取ります。理想的な刃先の形状を作り出すために、刃物を角度をつけて砥石に押し付けることで、砥粒が刃先にかかる角度をコントロールすることが必要です。
2.金属の表面の研磨
金属の表面には不純物や凹凸があり、研磨前は滑らかでない場合があります。この場合、砥石を使って研磨することで、不純物や凹凸を削り取り、滑らかな表面を作り出します。
3. 条件の考慮が必要
砥石の表面には砥粒が多数固着しています。砥粒は硬質の鉱物から作られており、砥石の種類によって砥粒の大きさや硬度、形状が異なります。
砥石を使って研削したり研磨したりする際は、砥粒の種類や粒度や硬度、砥石の種類や形状、加工対象物の種類や形状、押し付ける角度や力など、さまざまな条件を考慮することが必要です。
砥石の種類
砥石を砥粒の材質によって分類すると、以下のように種類があります。
1. アルミナ砥石
アルミナ砥石はアルミニウム酸化物 (Al2O3) を主成分とした砥粒を使用した砥石です。アルミナ砥石は比較的柔らかくて加工対象物に対する摩擦が少ないため研削作業に適しています。例えば鋼材の研削や金属部品の表面仕上げなどに使用されます。
2. シリコンカーバイト砥石
シリコンカーバイト砥石は炭素とシリコンを主成分とした砥粒を使用した砥石です。シリコンカーバイト砥石は、硬くて高温にも耐えられるため、鋳鉄や非鉄金属やセラミックなど硬質な素材の研削に適しています。
シリコンカーバイトは、炭素繊維やガラス繊維を含浸させたシリコンカーバイド (SiC) の一種で、高温での使用に適した非常に硬く耐久性が高い素材です。
3. ダイヤモンド砥石
ダイヤモンド砥石は、天然ダイヤモンドまたは人工合成ダイヤモンドを砥粒として使用した砥石です。ダイヤモンド砥石は、非常に硬く、研削作業において高い削り取り力を持ち、耐久性にも優れています。例えば刃物やハードディスクのヘッドやレンズなどの研削に使用されます。
4. CBN砥石
CBN砥石は、窒化ホウ素 (BN) を主成分とした砥粒を使用した砥石です。CBN砥石はダイヤモンド砥石と同様に硬く、研削作業に高い削り取り力を持ち、さらに耐久性に優れています。例えば鋳鉄、工具鋼、ハードメタルなど、硬質な素材の研削に使用されます。
CBNとは、「cubic boron nitride(立方晶窒化ホウ素)」の略称です。CBNは、ダイヤモンドと並んで超硬物質として知られており、非常に高い硬度と熱安定性を持っています。
BNとは「boron nitride (窒化ホウ素) 」の略称です。BNは、ダイヤモンドと同様に砥石や工具の材料として利用されますが、ダイヤモンドよりも比較的軟らかく、加工性が良好であることが特徴です。
ハードメタル (Hardmetal) は、主にタングステンカーバイトとコバルト等の金属から成る合金材料のことを指します。
砥石の特徴
長所
(高い剛性)
砥石は硬くて非常に剛性が高いため、加工時の振動が少なく高精度な加工が可能です。
(多様な加工対象物)
砥石は硬度や形状の異なる材料を加工できます。
(精密加工が可能)
砥粒の細かい砥石を使用することで、高精度で滑らかな加工面を得られます。
(耐久性に優れる)
砥石は研削材料であるため、磨耗して交換が必要な場合がありますが、適切な取り扱いとメンテナンスを行うことで、寿命を延ばせます。
(切れ味が良い)
適切な砥粒の選択と砥石の形状により、高品質の切れ味を得られます。
短所
(磨耗が激しくて比較的短い時間で交換が必要になる場合がある)
特に金属加工においては、砥石の目詰まりが進むことにより砥石の研削能力が低下して効率が悪くなるため、交換が必要になる場合が多い。
(粉塵の発生)
研磨した後に多くの粉塵が発生することがあるため、作業場所の清掃が必要になることがあります。特に、粉塵が健康に悪影響を与えることがあるので、適切な安全対策が必要です。
(砥石を使用する際には、安全面にも十分注意する必要がある)
砥石が割れたり、破損したりすることがあるため、適切な保護具の着用や、砥石が飛散しないような対策が必要です。また研削作業中に発生する熱により、砥石や加工対象物が変形することがあるため、十分な冷却が必要になります。
砥石のその他情報
砥石には砥粒の種類による分類以外にも、以下のような分類方法があります。
1. 形状による分類
円筒形、平板形、円盤形、錐形、棒形などに分類されます。
2. 結合剤による分類
砥石の砥粒同士を結合する結合剤の種類によって、陶磁器結合、樹脂結合、ゴム結合、金属結合などに分類されます。
3. 粒度による分類
砥石の砥粒の大きさによって、粗粒砥石、中粒砥石、細粒砥石、超細粒砥石などに分類されます。