板金ブラケットとは
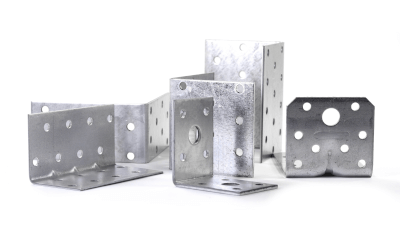
ブラケットとは、機械装置や部品を固定するための支持具や取り付け金具のことです。
その中でも板金ブラケットとは、機械装置や部品を固定するための支持具や取り付け金具の一種で、板金加工によって製造された製品のことです。その特性として、形状や用途に応じた多彩な加工が可能であり、幅広い産業分野で使用されています。
加工内容には、形状を整えるための曲げ加工、固定用の穴加工やタップ加工、安全性を考慮したC面取りやR加工などが含まれます。また、重量物や高負荷に対応するため、リブ構造の溶接加工や三角リブ加工といった補強を施せる点も特徴です。
板金ブラケットの設計では、固定対象物の特性や用途を十分に考慮し、コストを抑えつつ高い機能性を実現することが求められます。設計段階から効率的な加工法を採用することで、全体のコスト削減が可能になります。
板金ブラケットの使用用途
板金ブラケットは、産業用機械、光学機器、計測機器、自動車、家電製品など、多様な分野で利用されています。主な用途は、比較的強度が必要とされない部品や機器の固定です。
また、単なる固定にとどまらず、長丸穴のような調整可能な取付穴を設けることで、固定部品の位置を柔軟に調整できる設計も可能です。強度が必要な箇所では機械加工品が使われることが多いものの、板金ブラケットはコストを抑えやすく、リブ構造や溶接加工を加えることで重量物の固定にも対応できます。
板金ブラケットの原理
近年では、レーザー加工機が普及し、厚い板金の切断も可能になっています。例えば、9mm厚の板金でも安価に製作できるようになり、従来の機械加工品と同等の性能を持つ板金ブラケットが製造可能です。
大量生産の場合、タレットパンチプレス (通称タレパン) や専用金型によるプレス加工を用いることで、さらに製造コストを削減できます。1mm以下の薄い板金の場合でも、バーリング加工 (絞り加工) を併用したタップ加工により、十分な強度を持つタップを作ることが可能です。
また、板金専用の溶接ナットや溶接スペーサを活用することで、簡単に付加機能を追加でき、より多機能な板金ブラケットの製造が可能になります。ただし、曲げ加工を施す場合、曲げ部周辺の穴が引き伸ばされて形状に影響することがあるため、設計段階での注意が必要です。
板金ブラケットの種類
板金ブラケットの種類としてL型ブラケット、三角型ブラケット、スクエア型ブラケット、I型ブラケット、Z型ブラケット、凸型ブラケット、A型ブラケットの7種類が挙げられます。
1. L型ブラケット
L型ブラケットは最も一般的で、「アングル」とも呼ばれます。棚の受け金具としてよく使われるほか、工作機械や電気機器の内部部品にも使用されています。
シンプルな形状のため扱いやすく、汎用品として安価で手に入るのが特徴です。ただし、強度面では他の種類に劣る場合があり、重い荷重がかかる場面では注意が必要です。棚受けや軽量部品の固定に適しています。
2. 三角型ブラケット
L型ブラケットに斜めの筋交いを追加した形状で、三角形を形成することで強度を大幅に向上させたタイプです。重い物を支えるために適しており、壁面への取り付けや産業機械の補強に利用されます。
また、デザイン性の高い筋交いを加えたり、モノを掛けるフックを追加したりするなど、用途に応じたカスタマイズが可能です。ただし、L型よりも大きなスペースが必要になるため、設置場所に注意が必要です。
3. スクエア型ブラケット
筋交いを四角形にしたタイプで、棚板を複数取り付けられる設計が可能です。内部に棚やパイプを通しやすく、整理整頓に便利な構造となっています。
ただし、三角型ブラケットと比較すると強度は劣るため、軽い荷重に適した用途で使用されることが一般的です。家具や収納設備での使用が多く、効率的な空間活用を求める場面に適しています。
4. I型ブラケット
壁面から突き出したシンプルな形状で、設置面積を最小限に抑えられるデザイン性の高いブラケットです。棚受けや装飾品の固定に使われることが多いですが、設置面が小さいため、強度が必要な場合は壁自体を補強する必要があります。
I型ブラケットは見た目がすっきりしており、デザイン重視の空間にも適している一方で、耐荷重には注意を払う必要があります。
5. Z型ブラケット
Z字型の形状を持つブラケットで、高さの異なる部分を連結する用途に適しています。センサーや小型部品の固定、自動車部品の装着、棚板の設置などに活用されることが多いです。
Z型の特徴は、厚みのある部品を固定しやすい点や、細かな調整が必要な場面に対応できる点です。一方で、強度が求められる場合は補強が必要になることがあります。
6. 凸型ブラケット
凸型は、「凸」の形をしたブラケットで、2つの面で固定できるため、Z型よりも高い強度を持っています。自動車部品や木工製品の固定に使用され、振動が少なく、重い物を保持する場面に最適です。
ただし、2面分の設置面積を必要とするため、スペースに余裕がない場所では不向きです。耐荷重を確保しながら安定した固定が可能です。
7. A型ブラケット
A型ブラケットは、洋服のポールやハンガーを固定する用途で用いられる特殊な形状です。「a」の文字のように穴が空いており、パイプや棒状の部品を支えられます。
軽量で見た目がすっきりしているのが特徴ですが、過剰な荷重をかけると壁や取り付け部分に負荷がかかるため、設置には注意が必要です。
参考文献
https://jp.meviy.misumi-ec.com/info/ja/howto/33499/