ドラフトチャンバとは
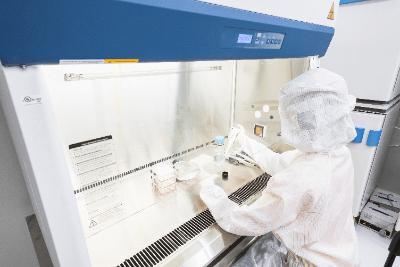
ドラフトチャンバとは、化学実験や生物実験などにおいて人体に影響を及ぼす可能性のある有害物質を取り扱う際に用いる、局所排気装置の1種です。
局所排気装置は大きく分けると、有害物質を覆うような形の囲い式と、開放状態で有害物質の側に吸い込み口(フード)が置かれた外付け式の2種類があります。ドラフトチャンバは囲い式の局所排気装置に分類されます。
囲い式の中でもカバー型、グローブボックス型、ドラフトチャンバ型、建築ブース型の4種に分類されます。
ドラフトチャンバ型は作業台が広く、前面に大きく開く上下(または左右)スライド扉からの操作性が良いのが特徴的です。
ドラフトチャンバの使用用途
事業者は下記3つの法律または規則に基づいて、労働者の健康と安全を守るためにドラフトチャンバ(または適切な局所排気装置)を取り付ける義務が生じます。
- 労働安全衛生法第二十二条(要約)
ガスや排気から労働者の健康障害を防止するため必要な措置を講じなければならない
- 特定化学物質障害予防規則 第二章(要約)
第1類および第2類特定化学物質を取り扱う事業場では局所排気装置を設置しなければならない
- 有機溶剤中毒予防規則 第五条 (要約)
第1種および第2種有機溶剤を取り扱う作業場所には局所排気装置を設置しなければならない
ドラフトチャンバ内に有害物質を置き、作業者は前面のスライド扉を少し開け、手のみ中に入れて作業します。
この時、決してドラフトチャンバ内に頭を入れてはいけません。正しい使い方をすることで、気化・飛散した有害物質の吸い込みだけでなく、万が一爆発が生じた場合に作業者の安全を守ることができます。
なお、ドラフトチャンバを含む局所排気装置を設置・移設・変更する際には、工事開始の30日以上前までに所轄の労働基準監督署に届出を行う必要があります。
ドラフトチャンバの原理

図1. ドラフトチャンバの原理
ドラフトチャンバは単に換気を行うだけではありません。排気ダクトを通った空気はスクラバーを通ることで有害物資が除去され、屋外へ排気されます。
従来の定風量方式ドラフトチャンバでは、扉の開閉に関わらず定量の空気を排気します。そのため、適切な給気を行わなければ排気と給気のバランスが崩れ、ドラフトチャンバが稼働している部屋の陰圧を保てなくなります。
また、定風量方式では空調された空気が多量に外に排気されることから、省エネの観点から問題視されてきました。
これらの欠点を補うものが、変流量(VAV: Variable Air Volume)方式です。
変流量方式では、扉の開閉度に応じて必要な排気風量を自動的に算出して排気するため、空調された空気を無駄に排気することを抑えることができます。
なお、ドラフトチャンバの扉の前面の風速については、有機溶剤中毒予防規則および特定化学物質障害予防規則によってて定められています。
有機溶剤中毒予防規則では制限風速が0.4m/s以上、特定化学物質障害予防規則では0.5m/s以上の排気をしなければなりません。
ドラフトチャンバのその他情報
1. スクラバーの役割
ドラフト内の空気には揮発した溶媒や試薬、微細な粒子などが混入しているため、そのまま待機中へ排出することはできません。そこで、排ガス中に含まれる有害な物質をトラップするため、スクラバーという設備を通します。スクラバーはトラップの方法によって、乾式と湿式に分類されます。
- 乾式スクラバー
排ガス経路に活性炭フィルターや不織布フィルターが設置されており、粉塵や揮発した有機溶媒を捕集します。フィルターの種類を変えることで、様々なガスに対応できます。
- 湿式スクラバー
シャワーノズルからアルカリ性の洗浄水を噴射し、水溶性ガスを溶解・中和します。酸性の蒸気を中和できる点は乾式にないメリットですが、非水溶性蒸気を捕集できないのがデメリットです。
なおドラフトの定期的な自主点検では、スクラバーの詰まりや破損の有無も確認が必要です。点検の際は、フィルターや洗浄水に有害物質が含まれていることを前提に、保護具を着用して作業を行います。
2. 簡易ドラフトチャンバー
卓上に置いて使用できる簡易ドラフトチャンバーも存在します。透明なボックス形の本体に送風装置と排気ダクトホースがついており、機種によっては排ガス処理のためのフィルターも備わっています。使用時は水平な台の上に置き、排気ダクトホースを局所排気設備につないで送風します。
ドラフトチャンバーを導入できない場合の代替品として使えますが、あくまで簡易的なものであるため、以下の点に注意が必要です。
- 作業スペースが狭いため、作業中に試薬瓶やビーカーに手が当たって倒し、内容物が飛散する恐れがあります。必要最小限の試薬のみをボックス内に入れる配慮が必要です
- 排気ダクトホース内にガスや蒸気が滞留し、片付ける際に吹き出して吸引する恐れがあります。使用後もしばらく局所排気を回し続け、ホース内の空気を十分に置換する必要があります。
- 排気フィルターも簡易的なものであるため、多量のガスが発生する場合は処理しきれない可能性があります。排気はスクラバーを通してから処理するか、少量の試薬のみ扱うよう制限を設けます。
3. ドラフトチャンバの自主点検義務
ドラフトチャンバを設置する事業者は、1年以内ごとに1回の定期自主点検を行わなければなりません。これは特定化学物質等障害予防規則第三十条に記載されており、義務付けられています。
点検内容としては、下記が挙げられています。
- フード、ダクト及びファンの摩耗、腐食、くぼみその他損傷器具の有無及びその程度
- ダクト及び排風機におけるじんあいのたい積状態
- ダクトの接続部における緩みの有無
- 電動機とファンとを連結するベルトの作動状態
- 吸気及び排気の能力
- 上記以外に、性能保持するため必要な事項
事業主は上記を満足するための自主点検を行い、その結果を検査表に記載する必要があります。また、この検査表は3年間保存することが義務付けられていますので、ドラフトチャンバを導入する際には留意してください。(同法令三十五条に規定されています。)
異常が生じた場合は、メーカーに相談のうえ対策方針を確定させる必要があります。また、修繕が必要な場合はその結果を同じく保存しておく必要があります。
4. ドラフトチャンバの点検に用いる風量計
点検項目の中に排気能力確認というものがあります。ドラフトチャンバの排気が正しく行われているかを確認するためのものです。
法令によれば、
- 有機溶剤中毒予防規則の適用範囲では、最低0.4 m/s以上
- 特定化学物質等障害予防規則にてガス状の排気を行う場合は、0.5m/s以上
- 同法令にて粒子状の排気を行う場合は、1.0m/s以上
を満足している必要があります。
これらの排気能力を点検するために風量計(風速計)を用います。
風速計には、熱線式風速計やベーン式風速計などの種類がありますが、規定はありませんのでいずれかを任意で選択可能です。
ただし問題となるのが、風速計が正しく値を測定しているのかどうかというものです。点検に用いる風速計が全く機能していなければ点検結果に虚偽の内容を含むことになりますので、風速計そのものの校正を忘れないように留意してください。
参考文献
https://www.jaish.gr.jp/anzen/hor/hombun/hor1-1/hor1-1-1-4-0.htm
https://www.jaish.gr.jp/anzen/hor/hombun/hor1-2/hor1-2-29-2-0.htm
http://ehs.k.u-tokyo.ac.jp/_src/259/fh_lecture_handout200828091129.pdf
https://www.jaish.gr.jp/anzen/hor/hombun/hor1-2/hor1-2-29-5-0.htm
https://www.testo.com/ja-JP/products/flow-meter