ラックギアとは
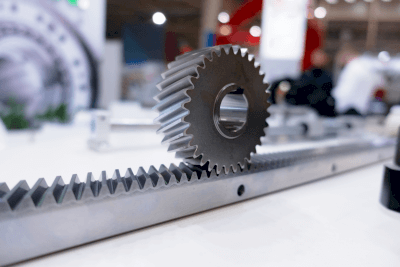
ラックギア (英: Rack Gear, Gear Rack) とは、角もしくは丸棒や板材に、同形状の歯が等間隔に並べられた無限大直径の歯車です。
ピニオンギア (小径歯車) と組み合わせて使用します。ラック&ピニオンと呼ばれ、回転運動と直動運動を双方向に変換可能です。
JIS B0102 歯車用語-第1部: 幾何形状に関する定義 では、ラック (英: Rack) として「1つの面に一連の同じ形状の歯を等間隔にもつ、平らな板又はまっすぐな棒」と定義されています。
なお、ラックは直径が無限に大きな歯車の一部分とみなすことができます。
ラックギアの使用用途
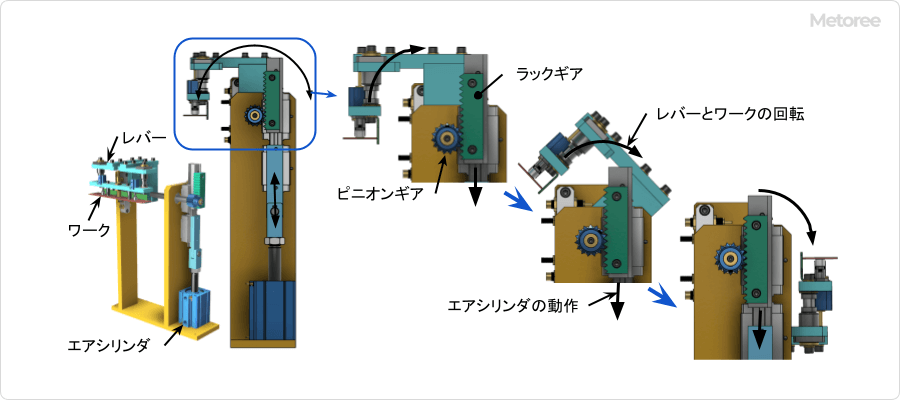
図1. ラックギア (ラック&ピニオン) の使用例
ラックギアは単体で使用することはなく、主にピニオンギアとの組み合わせで使用し、用途は回転運動と直動運動が行われる機械や装置です。図1は工場の製造ラインの使用例で、搬送されたワーク (対象物) をレバーのマグネットで吸着し、180度反転後に脱着して、ワークを次の工程に渡す機構です。
エアシリンダーの直線運動をラック&ピニオンによって回転運動に変換しています。また、自動車のラック&ピニオン式ステアリング機構があり、ステアリングシャフトの回転をタイロッドの直線運動に変換しています。下記は、その他の代表的な使用例です。
- 望遠鏡や顕微鏡の光学機器のピント合わせ機構
- ボール盤のスピンドルとテーブルの上下位置調整機構
- 工作機械の位置決め調整機構
- 工事用エレベーターの昇降機構
ラックギアの原理
1. 寸法と仕様
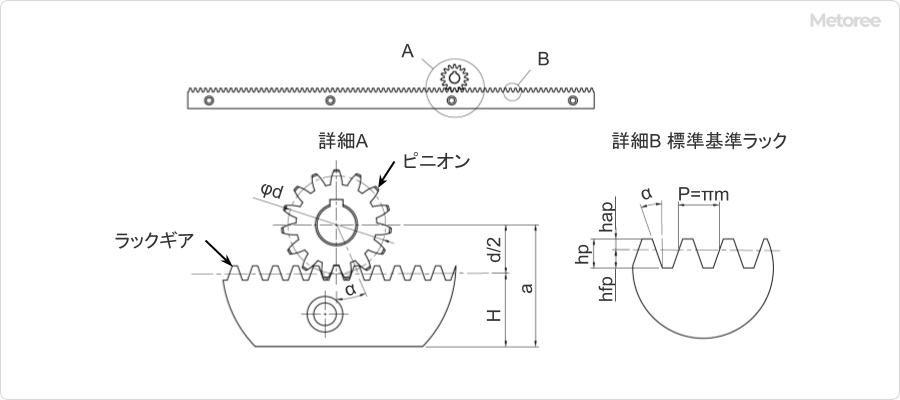
図2.ラック&ピニオンの寸法
ラックギアは、歯車の歯を直線状に並べた無限大直径の歯車で、減速比という概念がなく減速比は1となります。ラックギアの基本寸法は、標準基準ラックとして下記JIS規格で規定されています。
- JIS B1701-1 円筒歯車-インボリュート歯車歯形- 第1部: 標準基準ラック歯形
図2は標準基準ラックとピニオンギアの寸法および相互の位置関係、下表は寸法図の記号説明です。
項目
|
記号
|
計算式
|
説明
|
モジュール
|
m
|
P/n
|
歯の大きさをミリメートル単位で表したもの
|
ピッチ
|
P
|
Nm
|
基準線上の隣接する歯間の距離
|
圧力角
|
α
|
20度など
|
基準線の法線に対する歯の角度
|
歯末のたけ
|
ha
|
1.00m
|
基準線と歯先の距離
|
歯元のたけ
|
hf
|
1.25m
|
基準線と歯底の距離
|
歯たけ
|
hp
|
2.25m
|
歯底と歯先の距離
|
歯数
|
z
|
–
|
歯の数
|
転位係数
|
x
|
–
|
転位量をモジュールで割った値
|
ピッチ線高さ
|
H
|
–
|
ピッチ線までの高さ
|
組立距離
|
a
|
zm/2 + H + xm
|
|
基準円直径
|
d
|
zm
|
|
ラックギアの移動量
|
L
|
πmz
|
ピニオンギア1回転におけるラックギアの移動距離
|
2. 長さ
ラックギアの歯数は理論的には制限がありませんが、歯数が多くなり長尺になるほど曲がりや変形が大きくなり、製作精度が低下します。また、歯切り加工機により製作可能な長さが限定されます。
そのため、長尺ラックギアの場合は、ラック両端面を加工し歯ピッチが合うように、複数本を連結します。連結したラックギア全長には制限はありませんが、ラックギア単体長さは、一般的に2,000mm程度です。
ラックギアの種類

図3.ラック&ピニオンの種類
1. 歯すじ形状による分類
ラックギアの歯すじ形状は、すぐ歯ラックギアとヘリカルラックギア (はす歯ラックギア) があります。
すぐ歯ラックギア
歯面がラックギアの長手方向に対して直角で、歯は平行で等間隔に並んでいます。形状がシンプルで製作しやすいことが特長です。
ヘリカルラックギア (はす歯ラックギア)
歯面がラックギアの長手方向に対して斜めで角度 (ねじれ角) があり、歯は平行で等間隔に並んでいます。強度が高く、優れた静粛性で、高速度の使用に適しているのが特長です。ただし、ピニオンの軸中心方向にスラスト荷重がかかり対策が必要です。
なお、ラックギアとピニオンギアの歯ピッチは同一であり、ヘリカルギアの場合は、ラックギアとピニオンギアの歯は同一のねじれ角で、逆のねじれ方向の必要があります。
2. 断面形状による分類
代表的なラックギアの断面形状は、矩形形 (角棒) と円形 (丸棒)の2つがあります。
3. 材質による分類
ラックギアに使用する代表的な材質は下記のとおりで、材質によって強度や特性に応じて熱処理を行うことがあります。
- JIS G4051 機械構造用炭素鋼鋼材 Carbon steels for machine structure use, S45Cなど
- JIS G4053 機械構造用合金鋼材 Low-alloyed steels for machine structure use, SCM415、SCM440など
- JIS G4303 ステンレス鋼棒 SUS304など
- ポリアセタール (POM) 、MC901 (エンジニアリングプラスチック) などの樹脂材
- JIS H3250 銅及び銅合金の棒 Copper and copper alloy rods and bars, C3604 (快削黄銅) など
4. その他
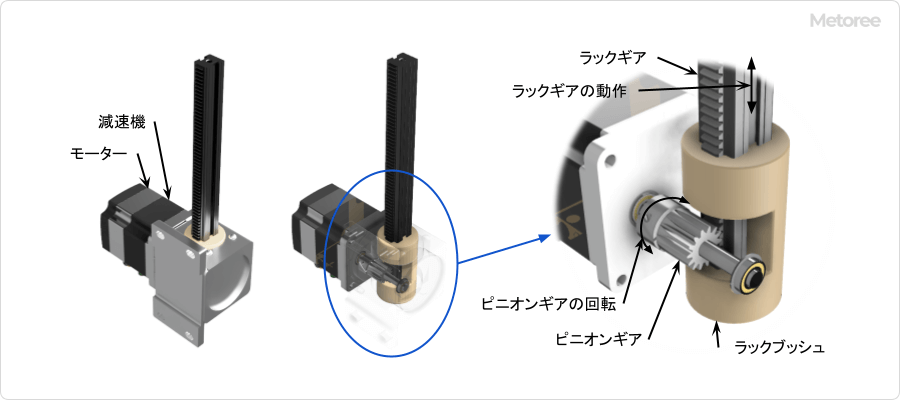
図4. リニアドモーター
上記以外に、ラック&ピニオンと減速機があらかじめ組み込まれているリニアヘッドに、モーターが付属しているリニアドモーターがあります。
ラックギアのその他情報
ラック&ピニオンの特徴
長所
- ロングストロークに対応可能
- モジュールを変更し大きな荷重にも対応可能
- 高速搬送に対応可能
- 材質、研磨や焼入れの有無、形状等を変更しさまざまな用途に対応可能
短所
- 高い負荷 (摩擦力) を受ける
- 騒音が大きくなる傾向が強い
- バックラッシを避けることができない
参考文献
https://www.khkgears.co.jp/khk_products/Rack_cp.html