監修:日本カンタム・デザイン株式会社
AFM (原子間力顕微鏡) とは
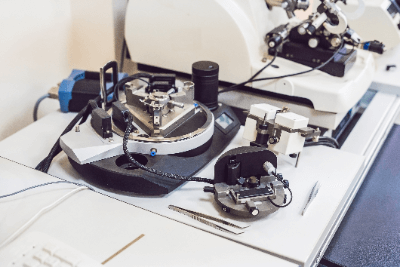
AFM( 原子間力顕微鏡 、英: Atomic Force Microscope) は SPM( 走査型プローブ顕微鏡 ) の一種で、ナノメートルサイズの試料の形状を観察できる顕微鏡の総称です。試料にプローブ(探針)と呼ばれるナノメートルレベルの先鋭な針を近づけ、表面の相互作用にもとづいて表面形状をナノスケールの分解能で測定できます。
もっとも一般的な用途は、ナノメートルスケールの高さ像を得ることです。光学顕微鏡やレーザー顕微鏡では見えなかった形状や正確な高さ情報が得られます。また、電子顕微鏡のように測定環境や試料の導電性も選びません。また、イメージングだけでなく、プローブを試料との間の力学応答(力学 – 距離曲線)をピコニュートンからナノニュートンの分解能で得ることができます。
AFM (原子間力顕微鏡) の使用用途
AFMは、ナノスケール (1nm=10-9m) からオングストローム (0.1nm) レベルで、表面の凹凸構造をあきらかにできることから、産業分野では主に検査目的で使用されます。
例えば、半導体基板の表面処理の均一さや粗さを測定や、金や銅などの金属をもちいた電極のメッキの腐食や劣化を検査するのに用いられています。 また、研究用途としては、タンパク質などの生体分子の反応や構造変化を低侵襲で観察するために用いられています。
1. コンタクトモード
カンチレバーとSampleの間に働く斥力が一定になるようにフィードバックをかけながらSample表面を操作するモード。AFMでは最も標準的な測定モードです。
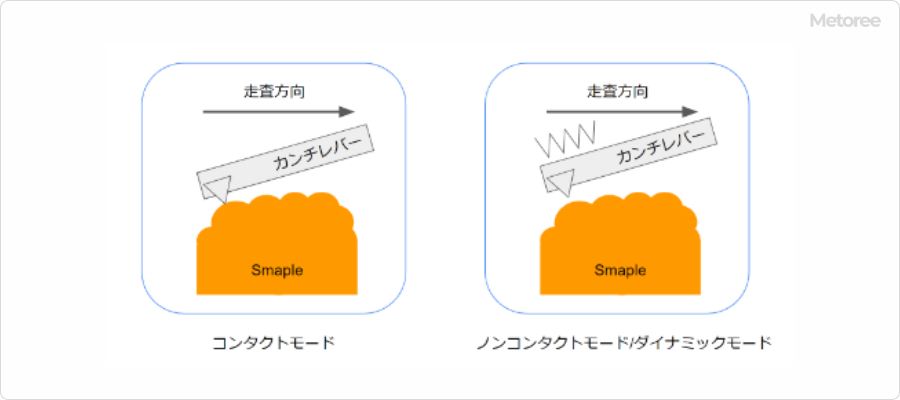
図1. AFMの使用例
2. ノンコンタクトモード/ダイナミックモード
呼称は、各メーカー事に異なりますが、カンチレバーを共振周波数付近で振動させます。この状態でカンチレバー先端が試料に接近するすると振幅が変化します。この現象を利用して振幅が一定になるように動作させ、Sample高さ方向の変位を取得するモードです。
AFM (原子間力顕微鏡) の原理
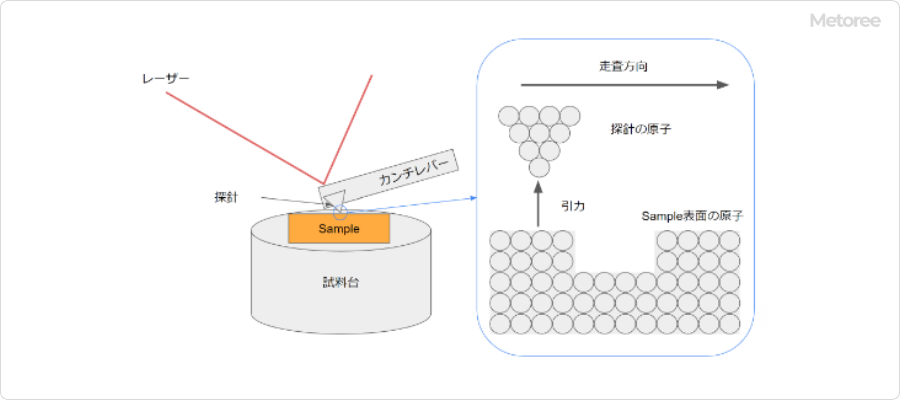
図2. AFMの原理
AFMはカンチレバーと、試料表面に作用する原子間力によって、カンチレバーの変位を検出することで測定を行います。 最も一般的な変位の検出法は、カンチレバーの変位をフォトダイオードによって検出する方法です。
カンチレバーの裏側の平面に光を照射して反射光をモニターし、原子間力によってカンチレバーが試料表面に引き寄せられると反射光の角度が変わるので、これを検知して再びカンチレバーの角度を修正するようにフィードバックがかかります。このときの制御パターンが表面の凹凸の形状として可視化されます。このような検出法を光テコ法とよびます。
もう一つは、ピエゾ素子を用いてカンチレバーを上下に振動させ、このときの振幅、位相、周波数をモニターする方法です。これらが一定になるようにフィードバックをかけカンチレバーを走査することで測定を行います。
また、カンチレバーのしなりを測定し、かかる力を直接測定する方法もあります。特に細胞などの生体試料の観察に用いられますが、この場合は表面形状の測定というより、膜タンパク質の局在や細胞の力学的な特定を測定するために用いられます。
AFM (原子間力顕微鏡) の特徴
・ SPM の一種で、正確な高さ像を高分解能で得られる
・ 試料の導電性・絶縁性を選ばない
・ 環境を選ばない(大気中・ガス中・真空中・液中)
・ 高さ像以外の相互作用も実空間マッピングできる
・ 微小な力 (pN – nN) を制御して非破壊測定が可能である
・ 力学応答によって硬さや分子間相互作用をマッピングできる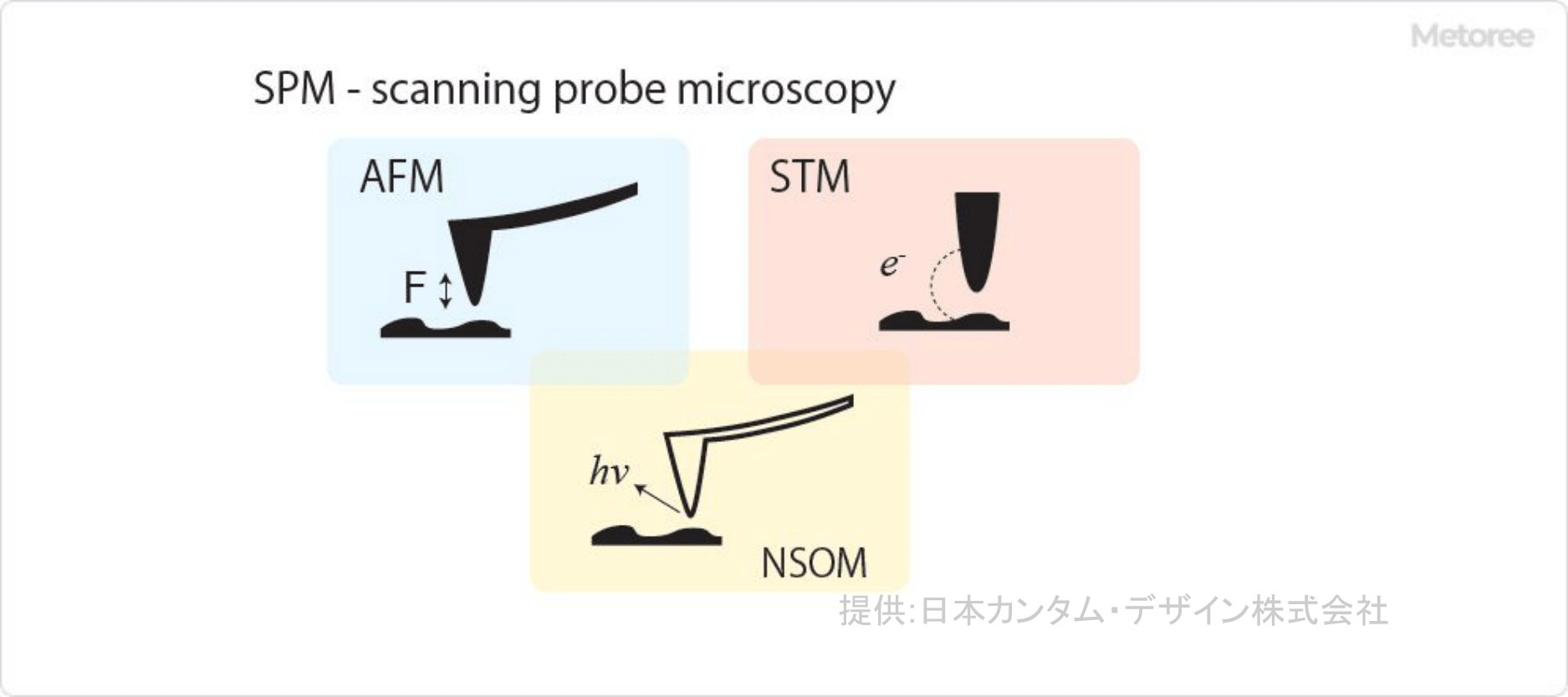
AFMの測定例
上記のような特徴からAFM は高い分解能と汎用性を持ち、材料科学、ライフサイエンス、半導体工学など幅広い分野で利用されています。産業分野でも、プロセス検討や品質管理、欠陥解析といった用途で用いられています。そのため、数多くのメーカーがさまざまな AFM を開発しており、それらをすべて網羅して比較検討することはなかなか難しいです。AFM の原理やさまざまな測定モードについては参考文献 [1],[2] などを参照ください。
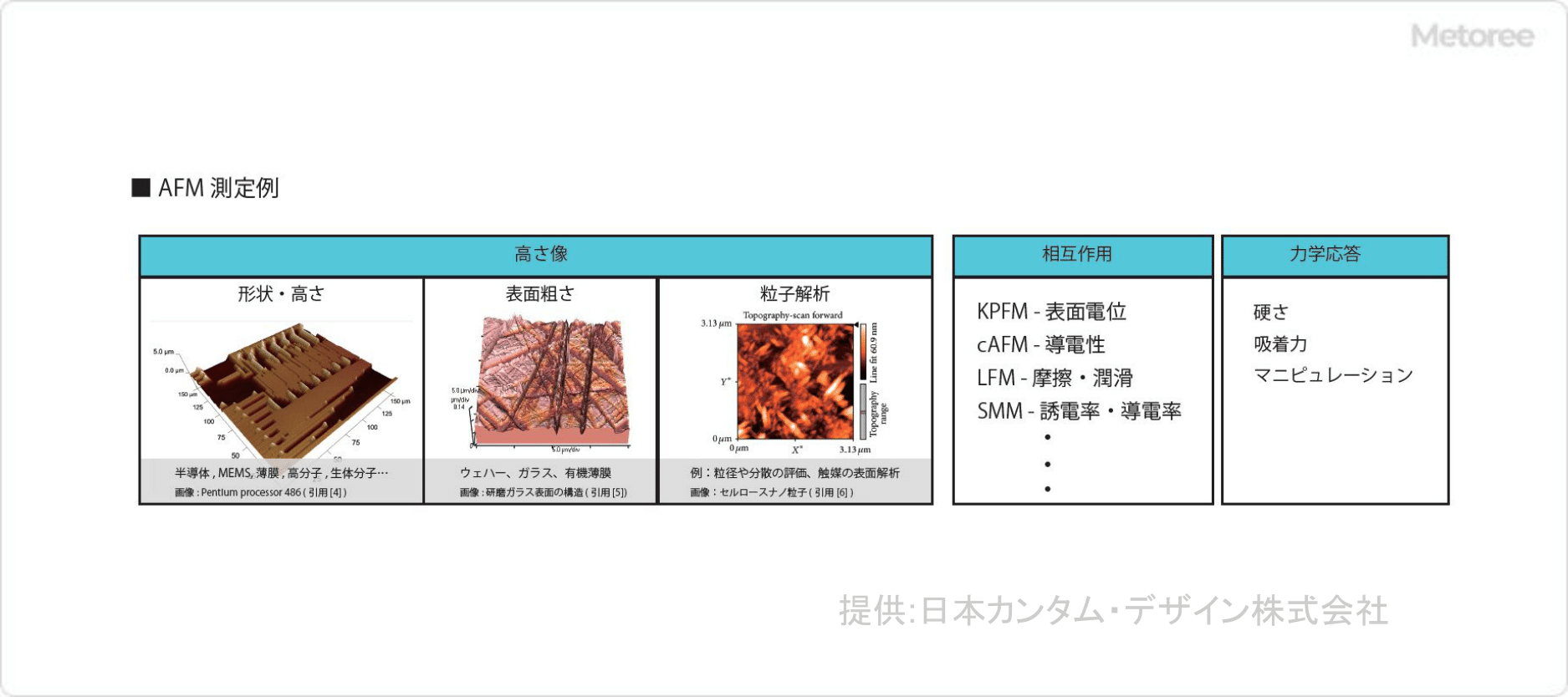
AFM (原子間力顕微鏡) の選び方
1. 必要な分解能と測定範囲
測定の目的によって、必要な分解能や測定範囲は大きく異なります。研磨加工を例にとると、研磨後の面粗さ (Rq) が数 nm 程度であれば安価な AFM でも十分に評価できます。しかし、CMP 研磨による試料の 0.1nm 未満の粗さの差まで評価するには、より高分解能・低ノイズのハイエンド機が必要となるでしょう。また、生体試料の液中測定を例にとると、XY 方向に数 10µmを超える細胞を観察したいのか、タンパク質など生体分子一つ一つを 100nm 四方の範囲で観察したいのか、によって選定するAFM は異なるでしょう。
ほとんどの AFM はナノスケールレベルの位置制御をピエゾ素子(スキャナ)を用いています。このスキャナは pm オーダーの伸縮が可能である一方、伸縮の範囲は大きくありません。市販されている AFM の XY 方向のスキャナサイズは 10 ~ 100um、 Z 方向は 1-20um 程度のものが多いです。スキャナの XYZ の範囲を超える測定はできません。試料のどれくらいの範囲を測りたいか、また、その凹凸の幅がどれくらいかを確認しましょう。範囲の異なるスキャナを交換できる装置もあります。
装置の分解能は、これらスキャナをどれくらい細かい刻みでデジタル制御できるかという計算上の分解能と、その装置内の内因ノイズの総和で決まります。計算上の分解能は、メーカーの装置仕様の中の ADC/DAC のビット数で計算することができます。しかし、これはあくまで単純計算した刻みであって、装置のノイズレベルの方が大きければ大きい方が装置の分解能となります。実際のところ、近年の半導体技術の進歩によって ADC/DAC は高速・高帯域になってきており、この計算上の分解能はノイズレベルを下回ることが多くなりました。特にハイエンド AFM の装置の分解能を比較する場合には「ノイズレベル」を参考にしましょう。
なお、高い分解能を求める場合、外因性のノイズ(建物や床の振動、周囲の音)が大きくにデータに現れてきます。AFM 用の防振台や防音箱は必須となるでしょう。
また、ピエゾスキャナの範囲を超えるミリメートル単位の移動や位置合わせも行いたい場合があります。たとえば、広いウェハー内の決まった位置を自動でスキャンしたい場合などです。その場合は電動ステージの有無とその可動範囲を確認しましょう。 200mm あるいは 300mm のウェハーをカバーできるモーターステージを備えた AFM もあります。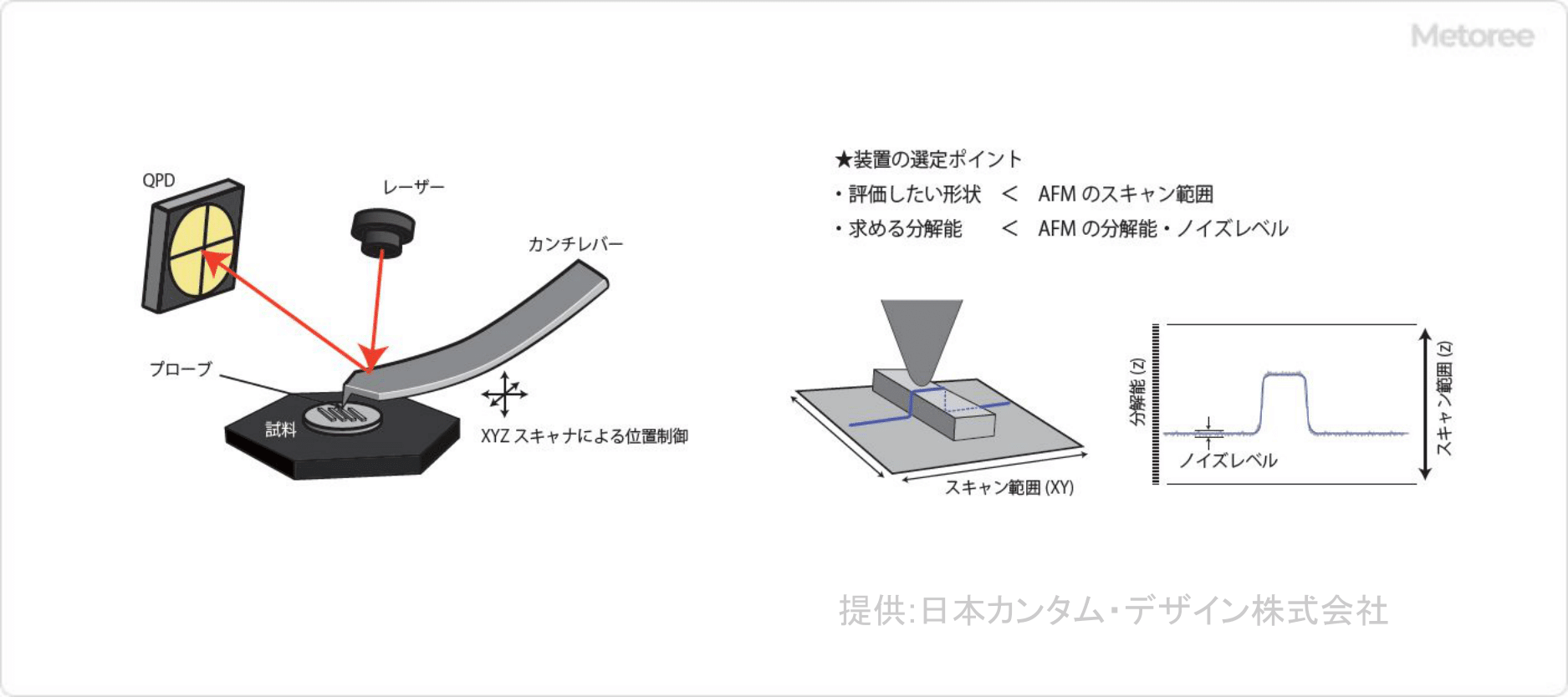
2. 装置のスキャン範囲
AFM で表面を測定するには、試料を試料ステージに安定に設置できることと、プローブ先端がその表面にアクセスできることが必要です。
・ 板状のもの
厚さが数ミリ程度の板状のものであれば、どの AFM でも測定が可能でしょう。たとえば、基板、スライドガラス、ウェハー、切片、ディッシュなどです ( 図 )。試料台に物理的に入り切らないものは、切断した小片にして測定します。磁石で固定するタイプの AFM の場合には金属の円盤に試料を固定します。
・高さ・重量のあるもの
各社 AFM のカンチレバーのマウント方法やヘッドユニットの構造はさまざまです数センチを超える厚みがある試料や、外縁のある容器内に試料を設置した場合、AFM プローブ先端以外の部分が先に接触してしまい、測定ができないことがあります。 AFM が許容する大きさ(外形と高さ)を確認しましょう。
また、重量のあるものはそのまま装置の試料台に設置できない、あるいはスキャナで走査できない場合があるので、最大荷重も確認しましょう。切断や加工によって試料自体を小さくできない場合、大型ステージを持つ AFM やカスタマイズ AFM を検討します。
3.装置の試料サイズとステージ形状

「試料大きさ(大きさ・高さ)がステージに入るか?」や「試料の大きさや容器が物理的に干渉しないか?」を考慮して選定をします。
例:測定したい試料が柔らかいサンプルや、動いたりするサンプルの場合。
AFM はプローブが 1 ラインごとの水平走査を繰り返して垂直に並べることで最終的な画像(フレーム)を得ます。もし、前のラインを走査した時にあった物体が次のラインを走査するときに動いたり、高さが変化するようだと、正しい像を得ることができません。そのため、プローブによる力によって簡単に転がってしまうもの、非常に柔らかいもの、動きのあるようなものは、AFM にとって非常に難しい試料と言えます。特にライフサイエンスの分野での液中測定でこのような試料が多く見られます。
このような試料を測定したい場合、一つの解決方法はプローブが試料に与える力が小さい測定モードを備えている AFM が選定することです。プローブを試料と間欠的に近づけることで試料へ与える垂直方向・走査方向の力を抑えます。カンチレバーを共振周波数で振るダイナミックモードは各社とも標準で備えています。さらに、非共振周波数で振動させるモードを備えている AFM は、非常に柔らかい試料や凹凸の大きな試料にも対応できるという特長があります (Bruker 社 PeakForceTapping, Nanosurf 社 WaveMode など )。
さらに進んだ解決方法は、物体や分子の動き自体を観察できるくらい高速に走査を終わらせることです。このような AFM は高速 AFM(HS-AFM) とよばれ、1 秒間に数枚から数十枚の撮像が可能です。(RIBM 社 , Bruker 社)ビデオフレームレートで像が得られる AFM は分子の動きをリアルタイム観察できることから、画期的な発見が数多く発表されています。高速性能とスキャナ範囲はトレードオフの関係なので、HS-AFM を選定する際には高速性能 (fps) とスキャナ範囲が研究や測定の目的に適しているか確認しましょう。
4. プローブの選定
使用するプローブも目的に合わせて考慮します。目的によって形状、材質、表面材質などが異なるさまざまなプローブが用いられます。特に、プローブの形状は分解能や得られる形状に大きな影響を与えます。
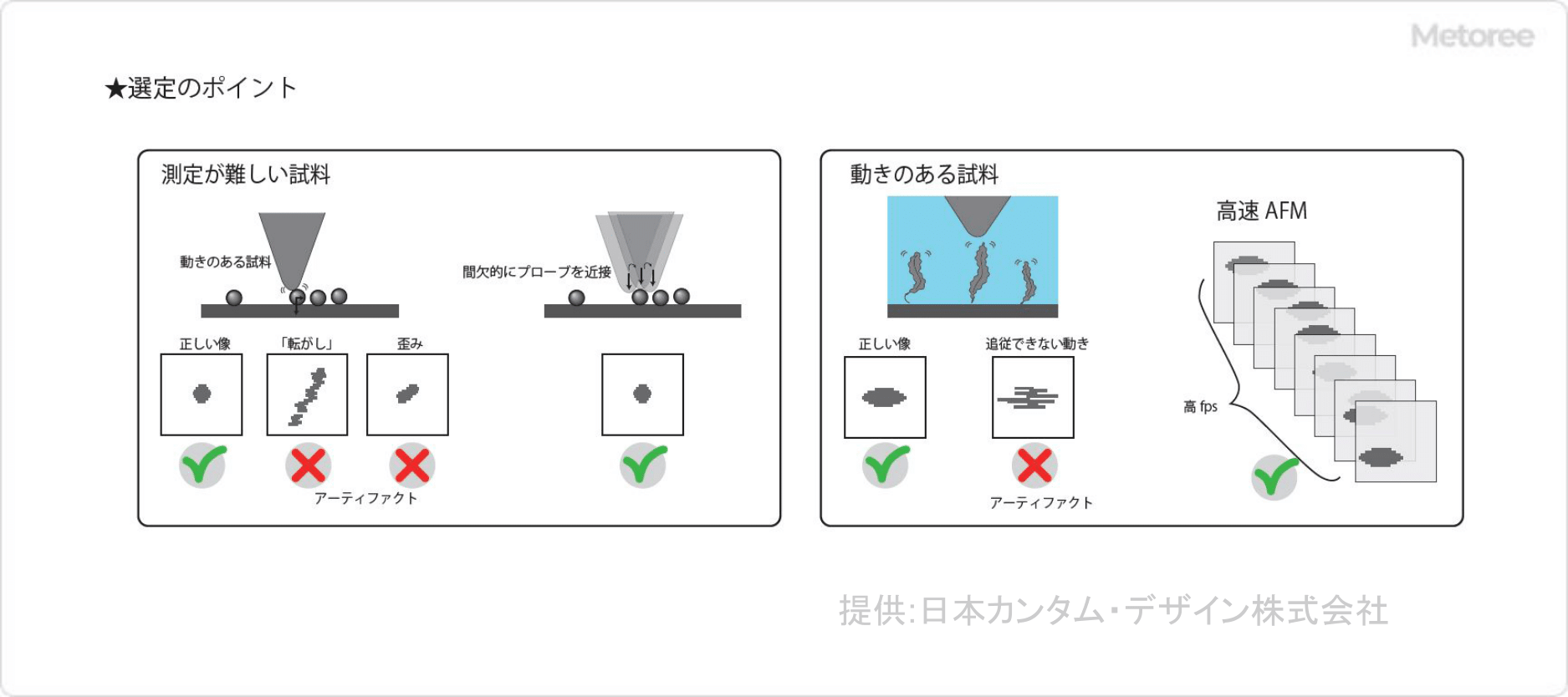
図のように、通常のプローブよりも先鋭化したプローブであれば、より分解能の高い像が得られます。アスペクト比が高いプローブであれば、深いトレンチ形状を正しく得ることができます。硬さ測定や相互作用測定ではコロイドプローブが使われることがあります。CD プローブは垂直なサンプル壁面を追跡でき、錐形のプローブでは測定出来ない臨界寸法を得ることができます。
形状以外にも、電気測定や磁気測定に用いるプローブ表面に金属膜をコートしたプローブがあります。プローブの材質自体が導電性のダイアモンドや PtSi のものもあります。目的とする測定方法と適したプローブについて、AFM メーカーあるいはカンチレバーメーカーに問い合わせると良いでしょう。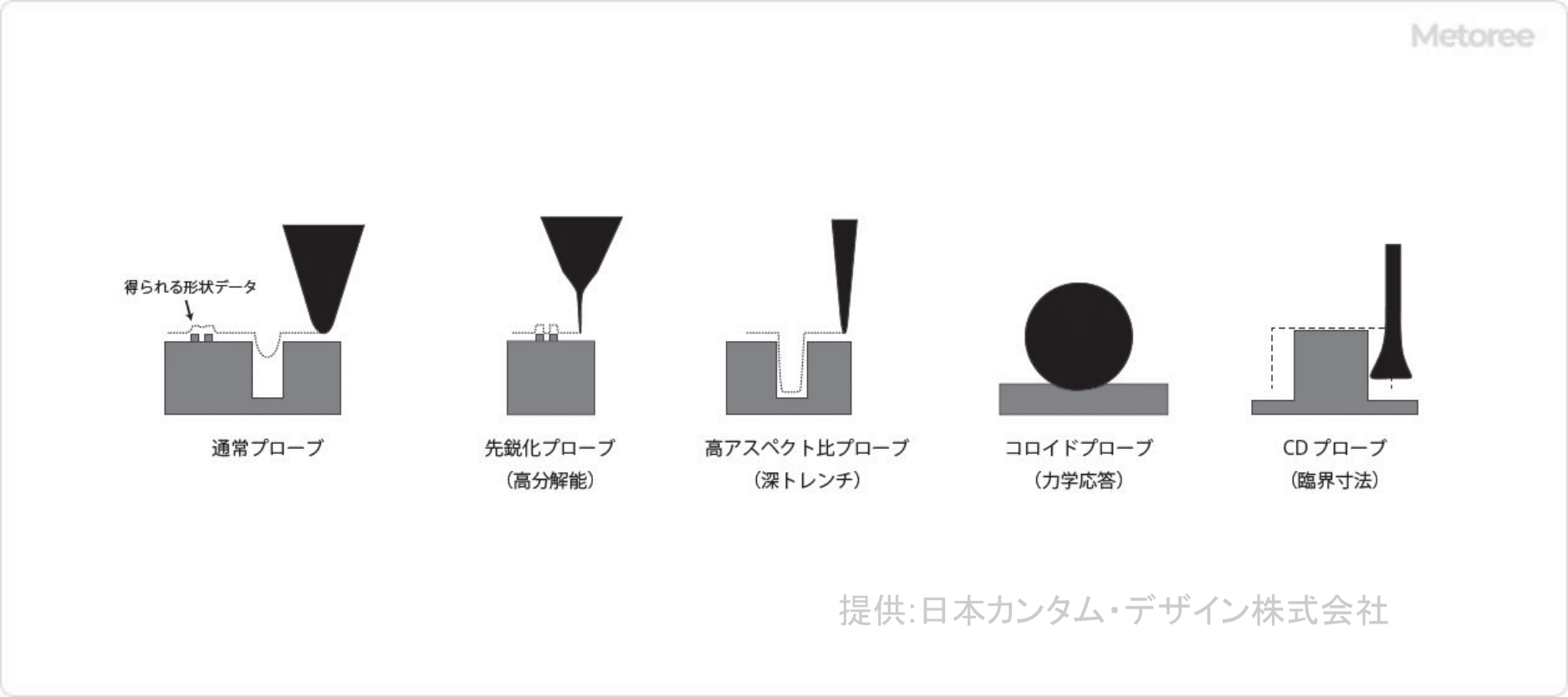
AFM (原子間力顕微鏡) のその他情報
1. AFMを使用することで分かること
AFMを活用することで検知可能な力として引力、斥力、端子先端と資料の表面の付着力、結合力が挙げられます。 AFMは触媒分野でも活用されています。活用例を下記に挙げます。
- 単結晶のゼオライトと層状の粘土鉱物の原子観察ができます。
- 原子レベルで平滑な表面を得ることができる雲母劈開面を利用して、その上に蒸着したパラジウム触媒で数nmの微小なパラジウム粒子の観察ができます。
AFMは測定をするにあたって、資料に特別な前処理を必要としないことに加え、大気・液体中などの幅広い環境で測定ができるという特徴があります。この特徴を活かして、表面局所領域での吸着現象や化学反応課程を測定する手段として使用されています。測定例として、やわらかい有機化合物の吸着過程の測定があります。 探針を修飾することで原子間力以外の力を選択的に測定することが可能です。一例として、探針に有機単分子膜で化学修飾することで化学センサとして機能させることができます。
2. AFMのフォースカーブ
フォースカーブは相互作用力の測定に活用されています。探針を往復運動させて、測定資料と探針の接触と引き離しを繰り返して測定されます。この往復運動によって探針と資料表面の間の力と距離の関数からフォースカーブを測定します。
フォースカーブはカンチレバー不安定性により本来のフォースカーブを追跡できずに、実測のフォースカーブがゆがんでしまうことがあります。この問題を避けるためには、力の配向に対して適切なカンチレバーを選択する必要があります。
空気中でのフォースカーブ測定では接触から引き離しまでにファンデルワールス力の他に表面張力に基づく凝着力とメニスカス力が測定されます。 フォースカーブ測定を固体表面の酸ー塩基の評価に応用された事例もあります。
3. AFMとSTMの違い
STMは超高真空中で高い原子分解能を持ちますが、導電性を持たない資料の測定や大気中で起こる資料表面の汚染の影響を強く受けるという点があります。 AFMは資料と探針の間に働く力を検出するので、導電性を持たない資料でも測定ができ大気中でも測定も可能です。
参考文献
[1] 分析化学実技シリーズ , 走査型プローブ顕微鏡 , 共立出版 (2017)
[2] ナノテクノロジー入門シリーズ , ナノテクのための物理入門 , 共立出版 (2007)
[3] 表面化学分析 – 走査型プローブ顕微鏡に関する用語 , JIS K 0147-2 (2017)
[4] Januszartur, CC BY-SA 3.0, via Wikimedia Commons
https://commons.wikimedia.org/wiki/File:Procesor_486_AFM_J_REBIS.png
[5] Chychderivative work: Materialscientist, Public domain, via Wikimedia Commons
https://commons.wikimedia.org/wiki/File:AFMimageRoughGlass20x20.JPG
[6] Moslem Mansour Lakouraj, Nazanin Bagheri, Vahid Hasantabar, CC BY 4.0, via Wikimedia Commons https://commons.wikimedia.org/wiki/File:Atomic-force-microscope-AFM-image-of-NCC.jpg
[7] Quantitative Data Processing in Scanning Probe Microscopy, Petr Klapetek, Elsevierhttps://www.an.shimadzu.co.jp/surface/spm/sol/faq/faq1.htm
本記事はAFM (原子間力顕微鏡)を製造・販売する日本カンタム・デザイン株式会社様に監修を頂きました。
日本カンタム・デザイン株式会社の会社概要はこちら