コバルト磁石とは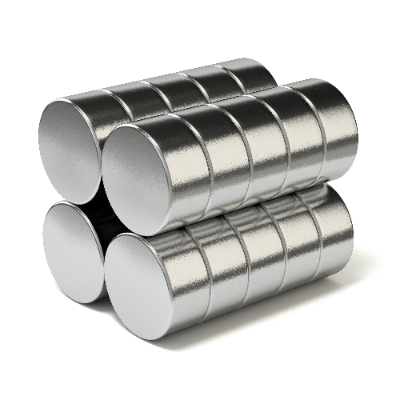
コバルト磁石とは、コバルトが含有された磁石です。
多くはサマリウムコバルト磁石のことを指します。強磁性を有するコバルトと希土類のサマリウムを1:5や2:17の組成の合金にすると、強力な磁石としての性質を持ちます。ネオジム磁石の次に強い磁力を持っており、温度特性に優れているため、産業界では重要な磁石です。
コバルト磁石の使用用途
コバルト磁石は温度特性の面でネオジム磁石よりも優れています。高温下でも磁力が減少しないので、温度安定性が必要とされる用途に適しています。一方、もろく壊れやすいため、強度が求められる場合の使用には注意が必要です。
以下はコバルト磁石の使用用途の一例です。
- OA機器などの電装モーター
- 電気自動車駆動用などの産業モーター
- 回転センサー
- 医療用精密部品
- 音響機器や発電機
コバルト磁石の原理
コバルト磁石とは、コバルトを主成分とする磁石の総称です。コバルトとその他の金属元素を合金化することで作成されます。
コバルトは原子番号27、元素記号Coで表される遷移金属元素で、強磁性を有しています。周期表では鉄と同じ9族に属しており、銀白色で鉄に似た性質を持ちます。ただし、硬く酸化されにくい特徴も有します。
コバルト磁石の種類
アルニコ磁石とサマリウムコバルト磁石の2種類に分類されます。
1. サマリウムコバルト磁石
サマリウムは原子番号62、元素記号Smで表される希土類元素です。灰白色でやわらかい性質を持っています。サマリウム自体には強磁性はありません。コバルト組み合わせ、SmCo5 (1-5系) やSm2CO17 (2-17系) 合金にすると、高い磁力を発揮するようになります。
ネオジム磁石よりも熱安定性や耐食性に優れているため、磁気センサーなどの車載製品、スマートフォン用カメラのアクチュエータ、医療機器などに使用されています。一方で、機械的強度が弱いため、使用可能な箇所が制限されます。
開発当初はサマリウム1に対してコバルトの組成比を5にした磁石でしたが、日本の物理学者である俵好夫博士がサマリウムとコバルトに加え、鉄・銅・ジルコニウムなどの複数の遷移金属元素を加えたコバルト磁石を開発しました。この磁石はコバルト系統の磁石の中で非常に高い性能を示すということが研究結果により明らかになりました。
現在市販されているサマリウムコバルト磁石の組成の一例として、コバルト 51wt%、サマリウム 26wt%、鉄 17wt%、銅 6wt%が含まれているものがあります。耐熱性という点で他の磁石よりも優れていますが、コバルトを多く含んでいるので、価格が高くなる傾向にあります。
2. アルニコ磁石
アルミニウム、ニッケル、コバルト、鉄、およびチタンを含む合金によって形成される磁石です。アルミニウム (Aluminum)、ニッケル (Nickel) 、コバルト (Cobalt) の頭文字から名づけられました。
高い磁気感受性と耐熱性を持つ点が特徴です。一般的には音響機器やモーター、発電機などの産業機器に使用されます。温度によって磁気特性が変化するため、高温環境で使用されることが多いです。
アルニコ磁石にはアルニコ2、アルニコ5、アルニコ8などの種類があります。
アルニコ2はアルニコ磁石の中で最も強い磁力を持ち、音響機器のピックアップに使用されます。アルニコ5は高温で安定した磁力を持ち、モーターや発電機などの産業機器に使用されます。アルニコ8はアルニコ5よりも強い磁力を持ち、高い磁気エネルギーを発生させるため、モーターや発電機の高性能化に使用されます。
コバルト磁石のその他の情報
コバルト磁石の発火
コバルト磁石は条件によっては発火するため、取り扱いに注意が必要です。特に、磁石表面が乾燥している状態やきれいに研磨されている状態では発火しやすく、低い温度で燃えてしまう可能性があります。
また、コバルト磁石は衝撃によって欠けやすく、コバルト合金の微粉末が生じる場合があります。この金属粉末は自然発火の危険性があるため、消防法における危険物第二類の可燃性固体に指定されています。コバルト磁石が摩耗して合金粉末が生じるような使い方を避け、安全に使用する必要があります。
参考文献
https://www.jstage.jst.go.jp/article/jinstmet/76/1/76_1_96/_pdf/-char/en
https://www.neomag.jp/mag_navi/column/column002.html
https://www.neomag.jp/products_navi/smco/smco_introduction.html
https://www.neomag.jp/mag_navi/mames/mame_seibun.html