ネイルハンマーとは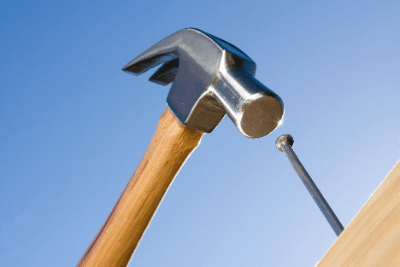
西洋から入ってきたハンマーの一種で、釘(ネイル)を打つためのハンマーの総称です。頭部の重心が打撃側にあるので釘を打ち込む際に手元がブレにくい造りになっています。
打撃側と逆側には、バールの様な釘抜き部がついています。同様の工具である金づちがよりも重心が打撃面に偏っているため、安定感が高く、初心者にも使いやすい構造です。
似ている道具に、仮枠ハンマーがあります。板厚が厚い木枠からの釘抜きを想定し、柄が長い造りになっています。一般的な作業であれば、ネイルハンマーの方がハンドリングしやすいため多用されています。
ネイルハンマーの使用用途
釘を打ち込む、打ち損じた釘を抜くという2通りの使い道が1本でできるため、幅広い場面で利用されます。学校での「工作」や「DIY」での作業、プロの職人にまで使われている工具です。
釘を打ち込む工具であるため、木材やプラスチックを多用した作業で使用されます。例えば「住宅建築」や「日曜大工」の場面で多用されています。
逆に「解体作業」にも力を発揮し、釘で結合している資材の分解に釘抜き部が活用されています。テコの原理を応用し、一般的な釘だけでなく又釘であったり、カスガイの引き抜きにも利用されています。
ネイルハンマーの選び方
- 頭部形状
打ちたい釘のサイズの3、4倍程度が丁度良い大きさです。打ち込まれるベースである石材や木材は、素材の方が柔らかい場合があります。そのため、対象より大きな槌面を持つハンマーは、釘周囲の資材を叩き、凹凸や破損などの原因となります。 - 全長
全長は200mm未満、200から300mm、300mm以上の大きく分けて3分類です。全長が長いほど打撃が強くなり、短いほど軽く取り扱いがしやすくなります。使用者の体型に合わせたサイズを選ぶことが大事でです。
また、短いと収納が楽です。逆に長いと、取り扱いが難しいデメリットがあります。さらに、壁など地面から垂直な位置にある釘を対象とする場合、力の入れ方が難しく、打ち損じを誘発する可能性があります。 - 材質(硬度)
炭素鋼(S45C)焼入れ、炭素鋼(S-45C)ミラーポリッシュ(鏡面加工)、TPE(サーモプラスチックエラストマー)が使われています。金属であれば、焼き入れをすると、強度が上がり、耐久性もupします。 - 打撃面の溝
溝があるタイプとそうでないタイプがあります。溝があると、釘と接触した際に滑りにくく、打撃が釘に伝わる可能性が高まります。
逆に溝がないと、釘が資材に食い込んだ際に、打撃面による資材への跡が残りにくい利点があります。 - 柄の素材
木材は、釘を強打した際に反動が少なく、手がしびれにくい良さがあります。逆に、スチールパイプは手への振動は伝わり易い反面、耐久性が高いのが特徴です。一方、グラスファイバは軽量で、手に馴染みやすくすっぽ抜けにくいため、初心者向きです。