切断砥石とは
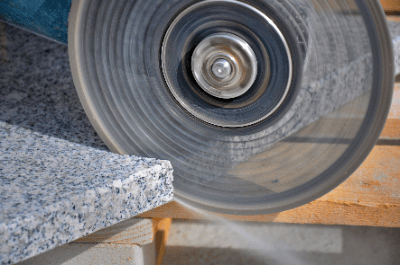
切断砥石 (せつだんといし) は、金属やコンクリート、タイルなどの硬い素材を切断するために使用される砥石の一種です。
一般的に直径が大きく薄い円盤状で、刃物のように回転して素材を研磨しながら切断できます。砥石の主成分 (砥粒) はアルミナやシリコンカーバイトなどの硬質材料であり、樹脂などの材質 (結合剤) で結合されています。主にグラインダー、切断機、チップソーなどの電動工具に装着して使用されます。
切断砥石には金属用や石材用やコンクリート用など素材によって使い分ける必要があります。また粗目のものから細目のものまで様々な種類があり、切削能力が異なります。
切断砥石の使用用途
切断砥石は、さまざまな分野で利用されています。以下に代表的な使用用途を挙げます。
1. 金属加工
アルミニウム、鉄、ステンレス鋼、銅、真鍮などの金属材料を切断したり、切削加工するために使用されます。金属切断砥石には、金属に合わせた硬度の異なる砥石があり、適切な硬度の砥石を選択することが必要です。
2. 石材加工
石材やタイルやセラミックなどの切断や加工に使用されます。切断砥石には、刃こぼれしにくいダイヤモンドなどの砥粒を使用しているものがあります。
3. コンクリート加工
コンクリートやレンガなどの切断や加工に使用されます。コンクリート切断砥石は、硬度が高く、抵抗があるコンクリートを切断するために開発されたものであり、特殊な結合剤を使用しているものがあります。
4. 自動車整備
自動車部品の切断や加工に使用されます。車両のシャーシ、エンジン部品、フレーム、排気管などを切断する際に使用されます。
5. 建築現場
建築資材の切断や加工に使用されます。鉄筋や鋼材や管材などを切断する際に使用されます。また、アスファルト舗装のカットにも用いられます。
切断砥石の種類
切断砥石を砥粒の種類で分類した場合、ボンド (結合剤) で分類した場合を以下に示します。メーカーによって名称が異なる場合があります。
1. 砥粒の種類による分類
アルミナ砥粒
アルミナを主成分とする砥粒で耐久性があり、一般的な金属 (鉄・鋼・ステンレス) の切断や加工に適しています。
シリコンカーバイト砥粒
シリコンと炭素を主成分とする砥粒で高い硬度と耐久性があり、金属加工に適しています。
ダイヤモンド砥粒
天然あるいは合成のダイヤモンドを砥粒として使用しているため、高い硬度と耐久性があります。石材加工やコンクリート加工や超硬材料の加工に適しています。
セラミック砥粒
セラミックスを砥粒として使用しているため硬度が高く、金属加工や石材加工や木材加工に適しています。
CBN砥粒
立方晶窒化ホウ素を砥粒として使用しているため硬度が非常に高く、金属加工に適しています。CBNとは、Cubic Boron Nitride (立方晶窒化ホウ素) の略語です。
2. ボンドによる分類
レジンボンド砥石
砥粒を樹脂 (レジン) で固めたもので金属加工に適しています。耐久性が高く高速切断に適しているので切削能力も優れています。一般的な切断砥石の多くがこのタイプです。
メタルボンド砥石
銀や銅やニッケルなどの金属 (メタル) で砥粒を接着したもので、石材加工やコンクリート加工に適しています。硬度が高く熱にも強いため、高負荷や高温度での作業に適しています。メタルボンドは主にダイヤモンド砥粒やCBN砥粒の結合剤として使用されます。
切断砥石の原理
切断砥石は、高速回転することで砥粒が対象物に接触し、摩擦熱と研削作用を利用して材料を削りながら切断します。その基本的な原理は以下の通りです。
1. 研削作用
砥粒が対象物に接触し、表面を削り取ることで切断します。砥粒は硬度が高く、耐摩耗性に優れているため、金属やコンクリートのような硬い材料でも加工できます。
2. 摩擦熱
切断時には大量の摩擦熱が発生します。砥石の材質や結合剤 (ボンド) の種類によっては、耐熱性や冷却性が異なります。過度な熱を発生させると、材料の焼き付きや砥石の早期摩耗につながるため、適切な砥石選びが重要です。
3. 遠心力と回転速度
切断砥石は高速回転するため、遠心力によって安定した切断が可能となります。ただし、回転速度が高すぎると砥石の破損や飛散の危険があるため、適正な回転数で使用することが重要です。
切断砥石の特徴
1. 長所
高い切削能力
硬質な砥粒により、短時間で正確な切削が可能です。
多様な材質に対応
金属、コンクリート、ガラス、石材など、さまざまな材料を切断できます。
高い耐久性
硬質な砥粒と適切な結合剤により、長寿命で耐久性が高いことが特徴です。
高精度の切削
精密な切断が可能で、細かい加工作業に適しています。
大量生産に適応
高速切削により、大量生産の現場で活用される。
2. 短所
粉塵や騒音が発生
切削時に大量の粉塵が発生するため、防護対策が必要です。
砥石の消耗
使用するにつれて砥石が消耗するので、定期的な交換が必要です。
熱による変形
高速回転による摩擦熱で素材や砥石が変形することがあります。
適応素材の制限
柔らかい素材には向かない場合があり、適切な砥石の選定が必要です。
切断砥石のその他情報
目付け (粒度) によって、切断砥石を分類することがあります。目付けとは、砥粒の大きさを表す指標です。数字が小さいほど砥粒が粗く、大きいほど細かいことを意味します。目付けが大きいものは表面の仕上がりがきれいな仕上げ用途に向いていて、目付けが小さいものは素材を効率的に切断できるため、金属加工などに適しています。
目付けが大きくなると、仕上げ面は良くなりますが、研削能力が低下します。また、研削熱の発生が多くなり、研削焼けやビビリが生じることがあるので注意が必要です。