圧縮ばねとは
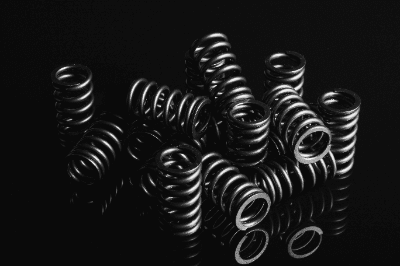
圧縮ばね (または圧縮コイルばね) とは、一般的に金属製のバネであり、物体に力をかけて圧縮することでその力を蓄える機構です。
物体を押し返す力を生み出すために使用されることが多いです。ばねの反力を利用することで、荷重方向への衝撃や重みを緩和させたりすることに利用されます。
圧縮ばねの使用用途
圧縮ばねはさまざまな用途で使用されます。
1. 文房具
最も身近な使用例は文房具で、ノック式ボールペンの芯先ばねが圧縮ばねです。ボールペンの芯が戻るように圧縮ばねの反力を利用しています。
2. 家具
ドアクローザーやバネマットレス、ソファなどのクッション機構にも利用されます。
3. 自動車産業
自動車産業では、自動車のサスペンションシステムに使用されます。これにより、車体とタイヤの間の振動や衝撃を吸収し、乗り心地を改善します。
4. 工業機械
工業機械や装置のバッファや振動吸収装置としても使用されます。工業機械は高速で動作するため、機械要素の衝撃や振動が生じます。圧縮ばねは、機械の運動部品や機械構造に衝撃を緩和するための緩衝材として配置されます。
5. 遊具・娯楽施設
遊具や娯楽施設にも使用されます。遊園地のジャンプ台やブランコ、トランポリンなどに利用されます。これらの遊具では、圧縮ばねが体重や力を受けて圧縮され、その反発力が楽しさや遊びの要素を生み出します。
圧縮ばねの原理
圧縮ばねの動作原理は、フックの法則によって説明されます。フックの法則は、ばねが受ける力 (F) と伸びや圧縮量 (x) との間に比例関係があることを示しています。ばね定数 (k) を用いて式で表すと「F = kx」です。
フックの法則では、ばねの変位が増えるとばねにかかる力も増えることが示されています。また、変位が減ると力も減少します。ばね定数kはばねの剛性や硬さを表し、大きいばね定数ほどばねはより堅くなります。
圧縮コイルばねは、静荷重下で使用されることが一般的です。静荷重とはばねが使用される状態で荷重変動がほとんどない状態です。このような静荷重で使用される場合には、ばねの許容応力は材料の弾性限度内におさまっていれば問題ありません。
線材の直径に対する許容ねじり応力の関係は、材質ごとに定められてます。圧縮コイルばねにおいてはばね使用時の最大応力が、定められる許容ねじり応力の80%以下となる環境下で使用されることが推奨されます。
圧縮ばねの種類
圧縮ばねには、主に等ピッチコイルばねと不等ピッチコイルばねの2種類があります。加わる荷重や必要となる機能によって使い分けられています。
1. 等ピッチコイルばね
完全な円柱状のばねです。ばねに加える荷重とたわみの関係は、一般的に線形の関係になります。荷重とたわみの関係が線形であることから、両者の関係を数式化して設計を行うことも容易です。
ただし、実際のばねでは全たわみの30%以下および70%以上の領域では計算値から外れる傾向にあるため、注意が必要です。これはばねが圧縮した際に両端部から接着が始まり、有効巻数が変化していくために起こります。
等ピッチコイルばねは自動車のサスペンションやコンピューターのキーボードなどに使用されています。
2. 不等ピッチコイルばね
完全な円柱形状ではなくいばねです。円錐コイルばね、たる形コイルばね、つづみ形コイルばねなどがあります。基本的にバネに加える荷重とたわみの関係は非線形の関係になります。
円錐コイルばねは円錐状になっているコイルばねで、圧縮されたときにコイル部分が干渉しないという特長があります。たる形コイルばねはたるのような形をしたコイルばねで、両端のスペースを小さくしたい場合などに用いられます。
つづみ形コイルばねはつづみのような形をしたコイルばねで、圧縮したときに中央付近での干渉を避けられるのが利点です。不等ピッチコイルばねは、電池ケース内の接点ばねやコーヒーフィルター用取っ手などに使用されています。
圧縮コイルばねの選び方
圧縮コイルばねを選ぶ際は、それぞれのばねが持つ諸元値を考慮する必要があります。圧縮コイルばねにおいては、ばね定数、自由長、外径が重要です。
圧縮コイルばねとして使用できる範囲は、自由長の位置から許容最大圧縮長までとなるため、これを考慮して選定を行う必要があります。 また、圧縮コイルばねは装置に取り付ける際、その両端を対象となる部品に固定しなければなりません。これらの部品の形状等に応じて選定します。