ファインメッシュとは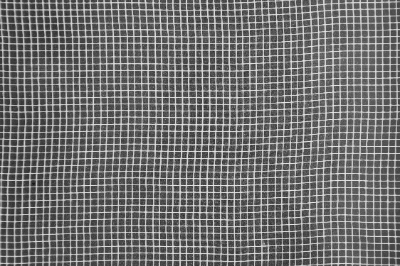
ファインメッシュは線径0.5~2mmの金属線を格子状に電気抵抗溶接して網目を形成した溶接金網と、最小線径0.02mmまでの極細線による平織り金網があります。溶接タイプは溶接接合により、従来の平織りの金網や線に屈曲を施したクリンプ金網に比べて、金属線の抜けがなく、グラツキやヒズミもなく、加工性に富んでいます。極細線平織りタイプは、その極小の網目によるフィルタ効果が活用されています。
金属線には用途に応じて鉄線、亜鉛メッキ鉄線、ステンレス鋼線等、真ちゅう線、銅線等が用いられます。
ファインメッシュの使用用途
ファインメッシュはメッシュサイズおよび金属線線径により、幅広い分野で、さまざまな用途に用いられています。
極細線平織りタイプは、フィルタとして、家電製品の防塵フィルタ、自動車関連のエアフィルタ、オイルフィルタに使用されています。
小サイズの溶接タイプは、収納用として、家庭用のラックやかご類、工業用には部品の搬送コンテナや化学処理用の部品トレー、洗浄カゴ等に使用されています。大サイズの溶接タイプは、住宅用のフェンス、農業用の防鳥ネット、建築用のコンクリート心材のような補強材として利用されています。
ファインメッシュの原理
ファインメッシュは使用される金属線の線径と網目のサイズで規定されますが、規格表においては、網目サイズはピッチ、目開き、メッシュのいずれかで記されます。
ピッチは、網目を形づくる四角形の対辺に当たる金属線の線間距離であり、目開きは網目の内寸法、つまりピッチから1本分の線径をマイナスした値と等しくなります。メッシュは25.4mm(1インチ)の距離にある網目の数であり、25.4mm/ピッチの値と等しくなります。
溶接タイプのファインメッシュで使用される金属線の線径は0.5~2.0mmの範囲であり、網目サイズはメッシュ1~4、ピッチで6.35~25.4mmとなります。極細線平織りタイプは最小線径0.02mm、最大メッシュ635(ピッチ0.04mm)のものもあります。
ファインメッシュにおいては、縦と横の金属線が重なるため、メッシュの厚みは金属線径の2倍になります。溶接交点において完全に縦横の金属線を溶かし込んだフラットなメッシュもあり、その場合は、厚みは金属線径径と等しくなり、せん断強度は2倍になります。
参考文献
https://ishikawa-kanaami.com/wp-content/uploads/wire-mesh.pdf