振動試験とは
振動試験とは、製品や部品が振動に耐えるかどうかを確認するために行われる試験です。
製品や部品に振動を与え、その振動に対する応答を観察し、性能や耐久性を評価します。この試験は、電子機器の部品だけでなく、構造に関する部品に対しても行われます。確認する項目は、振動による動作の不具合やねじのゆるみ、共振の有無、折損が発生する可能性の有無などです。
自動車などの機械をはじめ、スマートフォンなどの電子機器に至るまで、さまざま業界で振動試験が適用されます。電子部品などの製品は、振動が加わる場所に使用されていることも多く、振動により内部部品ねじのゆるみや割れ、回路の折損などが生じる場合があります。
そのため、振動が起きる環境でも正しく作動させる製品を作る際に振動試験を行います。振動試験とは、製品の品質向上や信頼性の確保に不可欠な試験です。
振動試験の使用用途
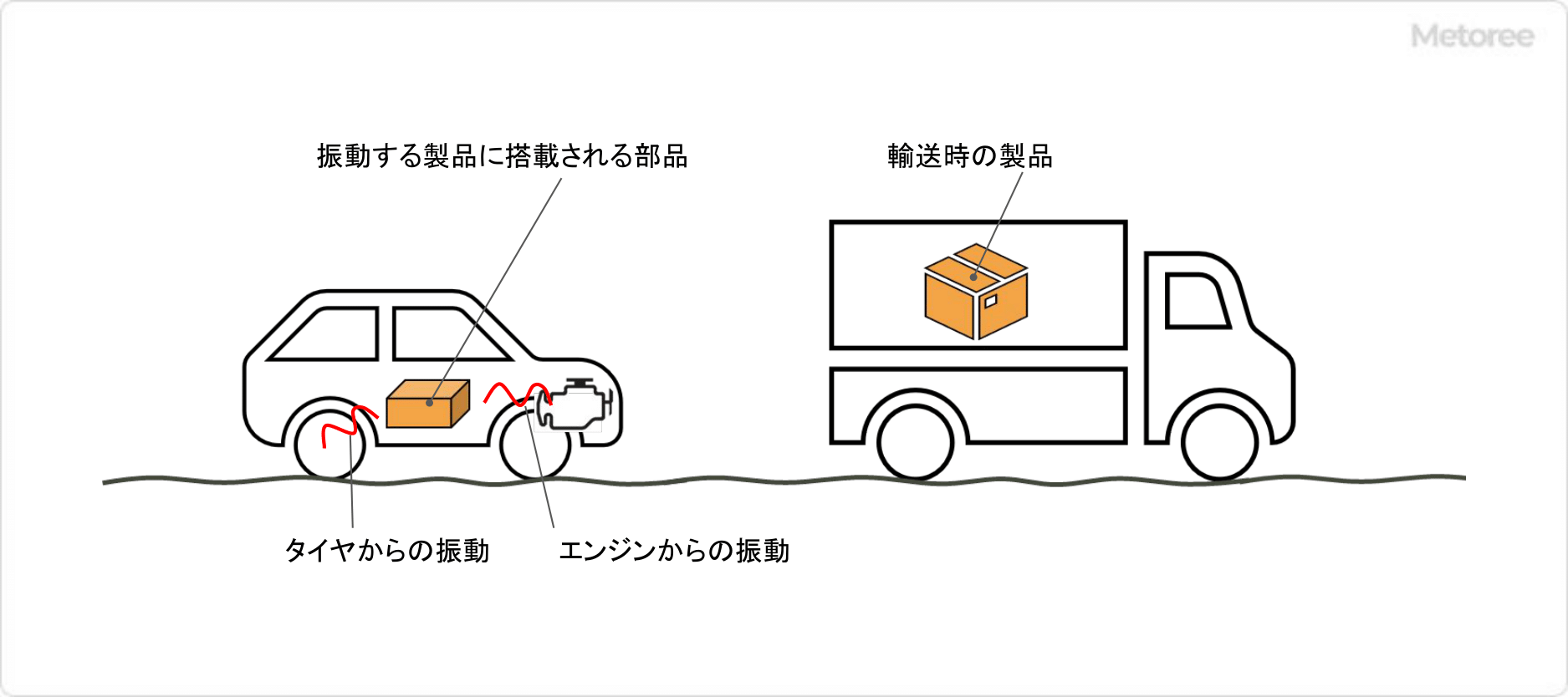
図1. 振動試験を実施する製品や対象部品の例
振動試験は、自身が振動する機械 (自動車や航空宇宙産業) 、土木、電子機器に至るまで、幅広い業界で実施されます。自身が振動する機械やそれに装備される部品だけでなく、自身が振動しない製品に対してもこの試験が行われる背景には、輸送時や使用時に受ける振動を考慮しているためです。
1. 自動車
自動車では、構造部品の耐久性・信頼性が重要です。自動車が走っている時は、エンジンによって車体の各部が絶えず振動しています。
振動が激しく中の部品に不具合が出てしまうと車自体が故障し身の安全が守られなくなる可能性があります。
2. スマーフォン
スマートフォンなど、リチウムイオンバッテリを内蔵する電子機器で最も懸念されるものは火災です。これらの電子機器は、輸送時・携帯時に振動を受けます。
振動により、リチウムイオンバッテリの内部回路に不具合が発生した場合、火災発生の可能性につながります。
振動試験の原理
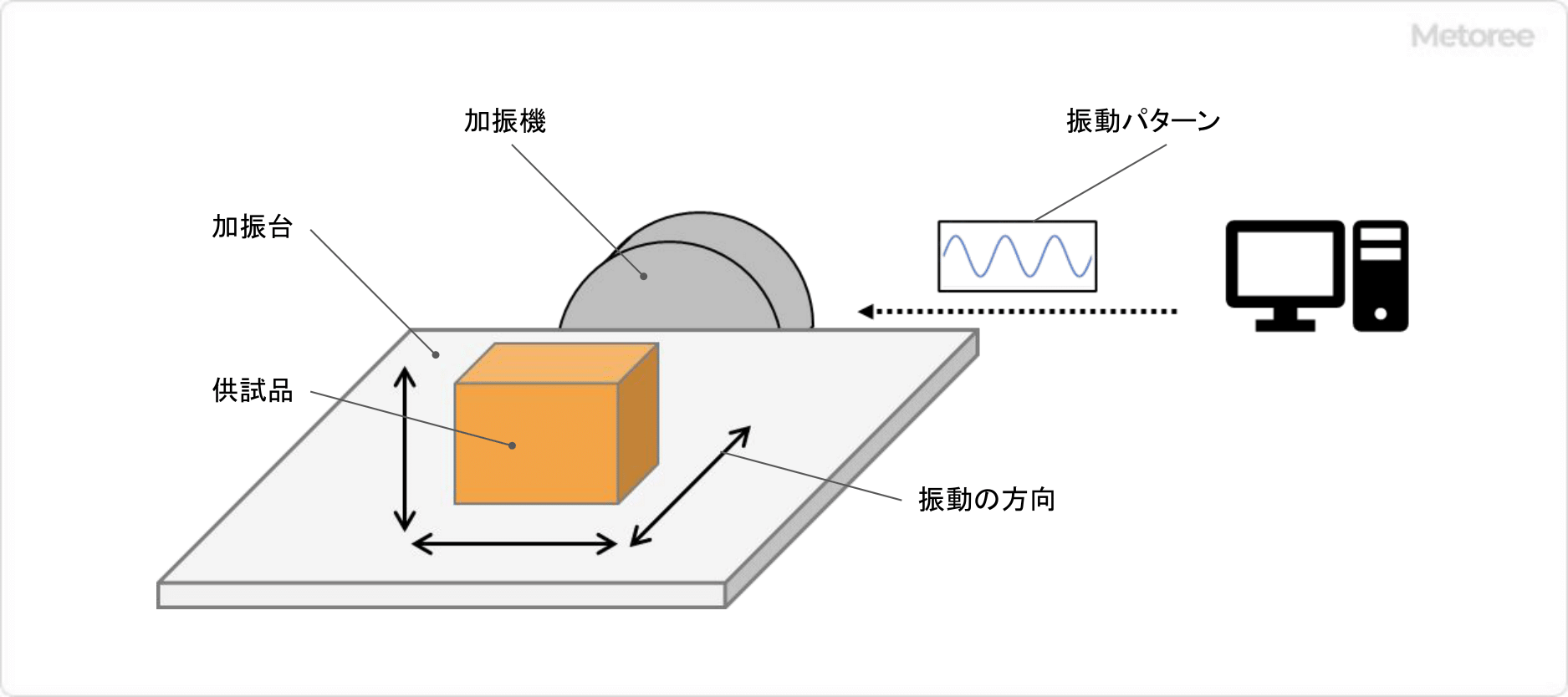
図2. 振動試験の実施
振動試験は、製品に対して垂直方向の振動と水平方向の振動の両方を評価します。加振台の上に試験サンプルを設置し、加振機によって振動を発生させます。
加振機とは、特定の振動パターンや周波数で物体を振動させるための機械です。振動の条件には、周波数、加速度、計測時間などさまざまなパラメータが存在します。振動の条件は、各製品によって受ける振動が異なるためさまざまです。
振動を受ける部品のうち主な製品 (鉄道や自動車に搭載される製品、輸送される製品など) は、それぞれの環境を想定した試験条件が記載されたJIS規格を参考にすることが推奨されます。振動の種類も数種類あるため、精査しながら試験を行います。
振動試験の種類
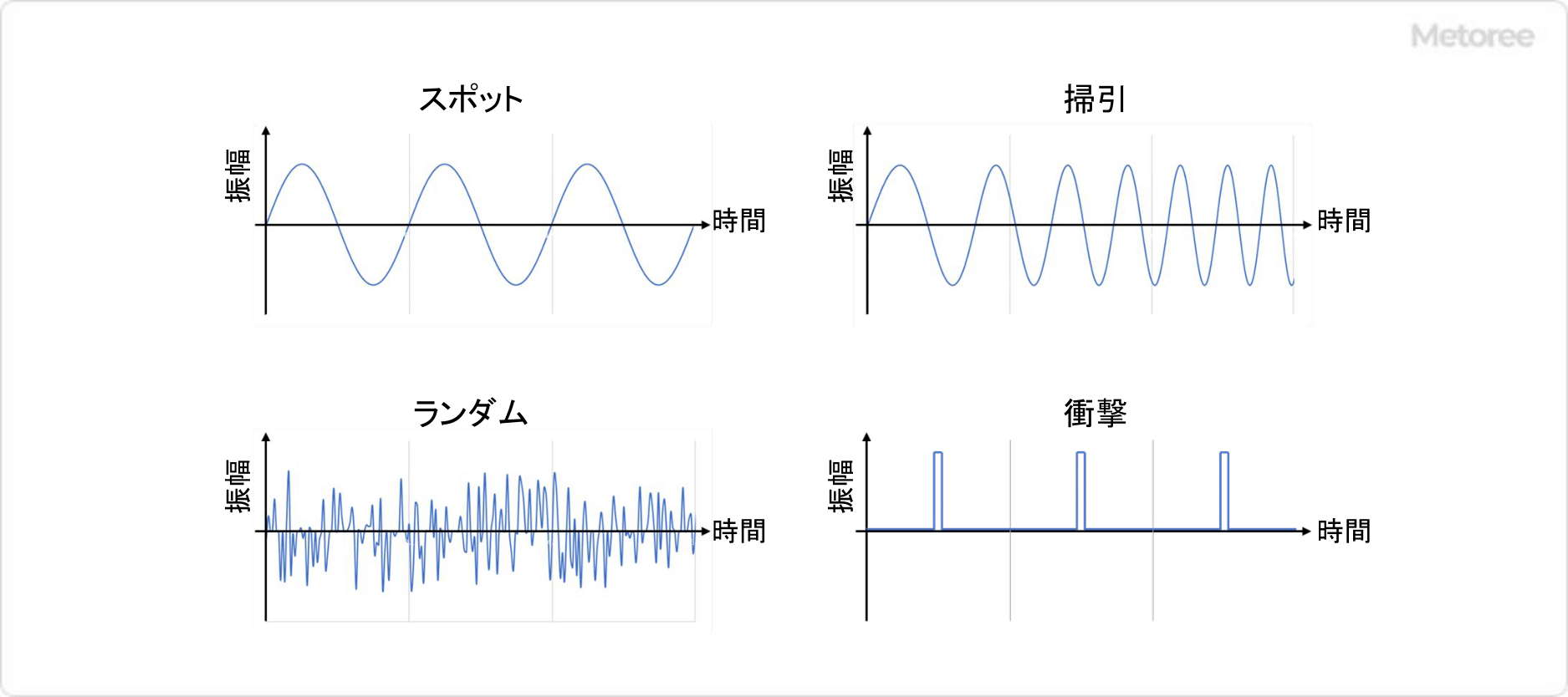
図3. 振動試験に用いる波形の例
1. スポット試験
スポット試験は、正弦波を用いた試験です。使用環境で発生する周波数が明確な場合に使用されます。
2. 掃引試験
掃引試験では、連続的に周波数を変化させていきます。あらかじめ変化させる周波数の上限と下限を決めておき、計測が開始されます。
ここで確認するものは、対象となる周波数域において、製品が内包する部品の閾値を超えていないか、または想定される使用環境下における共振の有無などです。
3. ランダム振動試験
ランダム振動試験では、周波数や振幅を指定しません。さまざまな振動をランダムに与えます。この試験では、新製品自身や、部品搭載時の実際の振動に近いとされ、信頼性評価に活用されます。
4. 実機振動試験
あらかじめ計測した実際環境の波形をパターン化したものを使用した試験です。製品・部品の信頼性の評価や不具合が発生した場合の再現などに活用されます。
5. 衝撃試験
一般的には、瞬間的に大きな振幅・加速度が発生するような衝撃が対象です。パルス波形を供試品に加えます。耐衝撃性の評価に活用されます。
振動試験のその他情報
振動試験の主な目的
1. 製品耐久性の評価
例えば自動車部品、航空機部品、電子機器などの製品は、運用中に振動にさらされることがあります。振動試験によって、これらの製品が長期間にわたって正常に機能することが確認されます。
2. 製品の信頼性評価
製品の信頼性をテストし、設計上の欠陥や問題を特定するのに活用します。これにより、不具合の早期発見と修正が可能となり、製品の信頼性向上に寄与しています。
3. 品質管理
振動試験は品質管理の一環としても使用されます。製品の一部として提供される部品や材料の品質を確保するために、振動試験が行われます。これにより、不良品の供給を防ぎ、高品質の製品を提供できます。