フレキシブルプリント基板とは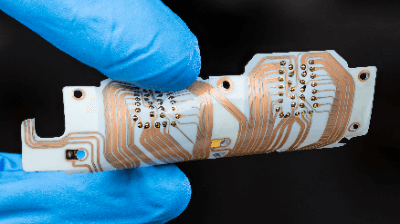
フレキシブルプリント基板とは、ベースフィルムの上に屈曲可能な銅よって配線パターンを形成した基板です。
ベースフィルムは、絶縁性があり屈曲可能な樹脂で構成されています。フレキシブルプリント基板は、厚さを薄くすることが可能で、電気的な特性を維持したまま自在に屈曲できる特徴を持ちます。
フレキシブルプリント基板の使用用途
フレキシブルプリント基板は、部品などを搭載して回路基板として使用されるほか、配線パターンのみを形成してケーブルのように接続部材としても使用可能です。
薄く柔らかいという特徴から、曲げる、折りたたむなどの動作が必要な可動部分や、接続部分に多く使用され、フレキシブルリジット基板と共に立体的回路などにも用いられています。フレキシブルプリント基板は、当初の使用目的である宇宙開発分野や軍事的分野のほか、薄型および軽量化が要求されるスマートフォンや携帯電話、タイピングキーボードや電卓などの身近な分野でも使用されることが多いです。
フレキシブルプリント基板の原理
フレキシブルプリント基板は、ポリイミドなどの屈曲可能な樹脂製のベースフィルムの上に屈曲可能な銅によって配線パターンを形成したものです。
プリント基板としては、硬質で屈曲しない絶縁性のあるベース板の上に配線パターンをもつリジット基板もあります。フレキシブルプリント配線板は、リジット基板と異なり、ベースが薄いフィルム状とされていること、ベースが屈曲可能であることから、リジット基板よりも厚さを薄く加工できる上、屈曲可能な点が特徴です。なお、リジット基板と同様に、配線パターン上に部品を実装できます。
フレキシブルプリント基板の種類
フレキシブルプリント基板には、配線パターンがベースフィルムの片面に1層のみ形成された片面構造と、ベースフィルムの両面に1層ずつ形成された両面構造があります。また、ベースフィルムの両面それぞれに2層以上の配線パターンが積層された多層化フレキシブルプリント基板もあります。
1. 片面構造
フレキシブルプリント基板の片面構造は、1層の配線パターンがベースフィルムの片面のみに形成されているものです。片面構造は軽く柔軟性に優れており、可動への耐久性が強いため、可動部分でよく用いられます。
2. 両面構造
フレキシブルプリント基板の両面構造は、1層の配線パターンがベースフィルムの両面にそれぞれ形成されているものです。両面構造は小型で高密度に配線パターンを形成できる点に優れ、より多くの機能を搭載できます。しかし、片面構造と比較すると、柔軟性や耐久性に劣るため、可動部分での使用には不向きです。
3. 多層化フレキシブルプリント基板
多層化フレキシブルプリント基板とは、フレキシブルプリント基板を多層化させたものです。フレキシブルプリント基板においても、リジット基板と同様にベースフィルムの面上の配線パターンを2層以上に積層することができます。
この場合、効率よく多層化するために、ベースフィルムの両面に2層以上の配線パターンを絶縁層を挟んで積層します。この多層化フレキシブルプリント基板に保護層を設けたものをフレックスリジット基板などと呼びます。
この多層化フレキシブルプリント基板 (フレックスリジット基板) は、軽量ながら、リジッド基盤と同様の高い機械強度と回路形成をすることができるため、立体的回路などへの使用が可能です。電子機器をコンパクトにサイズダウンするには必要不可欠な部品となっています。
フレキシブルプリント基板のその他情報
1. フレキシブルプリント基板の製造方法
フレキシブルプリント基板の製造方法として、片面構造のフレキシブルプリント基板を例に解説します。
- フォトレジストの塗布
ポリイミドフィルムなどの絶縁ベースフィルムに銅箔が貼り合わされたCCLにフォトレジストを塗布します。
- フォトマスクの形成
これに所定の配線パターン形状を作製したフォトマスクをかぶせます。このとき、フォトマスクは、印刷や写真の技術と同様に、配線パターン部分を除去した形のものです。
- フォトマスクの紫外線硬化
フォトマスクの上から紫外線を照射し、配線パターンに対応した部分のみ紫外線硬化させます。
- フォトレジスト除去
フォトマスクを除去し、薬液を用いて未硬化のフォトレジストを除去します。
- 銅箔の除去
次の工程は、エッチングと呼ばれる工程です。エッチング工程では、薬液により銅箔の除去をおこない、フォトレジストに保護されている部分、すなわち配線パターン部分の銅箔のみが残り、配線パターンが形成されます。
- 硬化フォトレジストの除去
配線パターンを覆う硬化したフォトレジストを薬液により除去します。
- カバーレイの形成
配線パターンを保護するカバーレイと呼ばれる絶縁層を形成します。
このようなフレキシブルプリント配線基板の製造には、多くの化学的知識が必要です。配線パターンのみを残すエッチング工程や、配線パターンを保護するカバーレイの形成工程には無機化学の知識が必要となります。
各工程間では、水洗がおこなわれますが、この水洗工程における廃液には多種多様の有害物質が含まれるため、化学的知識に基づいた高度の排水処理技術が必要です。
2. フレキシブルプリント基板の世界動向
西暦2000年以前には、多くの分野でメイドインジャパンは品質が良いとされており、日本の製造業は世界的にも高い競争力を誇っていました。しかし、現在では必ずしもそうではありません。フレキシブルプリント基板の製造分野においても、日本はかつてトップでしたが、現在は大きく様変わりしています。
フレキシブルプリント基板は、世界中で製造され、約2,500社が製造しています。2018年では台湾のメーカーがトップで、次いで日本や韓国、中国など東アジアの一部の有力メーカーです。フレキシブルプリント基板は、官民の軍需及び産業機械、宇宙産業や自動車、通信分野など様々な分野で、今後も需要が高まると予想されています。
技術力向上への投資やレアメタル資源が潤沢であることから、中国が最も勢いがあると予測する見方もあります。トップグループの台湾・日本・韓国はより高単価のニッチ分野に向かい、中国は現在でこそ低価格帯のプリント基板中心の売上を伸ばしていますが、技術力の差は縮まっており、将来的に中国がトップグループに入るのは時間の問題です。
参考文献
https://www.p-ban.com/about_pcb/flexible.html
https://www.mektron.co.jp/product/fpc/
https://www.elephantech.co.jp/pickups/what-is-flex-pcb/
https://www.okidensen.co.jp/jp/prod/fpc/flexible/fpc_setumei.html
https://www.p-ban.com/about_pcb/flexible.html
https://www.jstage.jst.go.jp/article/jiep1998/7/5/7_5_367/_pdf