¿Qué son los Filamentos?
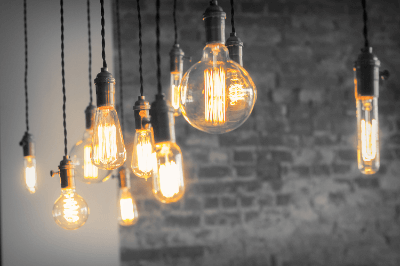
Los filamentos son las partes emisoras de luz de las bombillas blancas y otros dispositivos de iluminación. Se trata de un elemento resistivo situado en el interior de la bombilla de cristal y con forma de alambre largo y fino. Los filamentos emiten luz cuando son calentados por una corriente eléctrica.
Cuando se inventaron, los filamentos se llamaban bombillas de carbono porque el material utilizado era papel carbonizado. Sin embargo, en cuanto brillaban durante aproximadamente un minuto, los filamentos se quemaban y no alcanzaban un nivel que permitiera utilizarlos en la vida cotidiana.
Por ello, hoy en día se utiliza casi exclusivamente un metal llamado tungsteno.
Usos de los Filamentos
Los Filamentos se utilizan como fuente de luz en las bombillas.
1. Bombillas Incandescentes
Las bombillas incandescentes son bien conocidas como el principal uso de los filamentos. Estos están hechos de alambre delgado de tungsteno enrollado. Sin embargo, muchas bombillas modernas para iluminación general utilizan una forma de doble espiral para reducir la pérdida de calor.
Existen varios tipos de bombillas incandescentes, como las halógenas, las de minicriptón y las fluorescentes. El interior de la bombilla de cristal está lleno de un gas inerte para evitar que los filamentos se evaporen (por ejemplo, argón, nitrógeno, criptón, xenón).
Algunas también existen con vacío en su interior, y las bombillas incandescentes producen diferentes colores e intensidades de luz según el tipo de gas. En los últimos años, algunas bombillas incandescentes distintas de las halógenas y las de minicriptón se han dejado de utilizar porque no son eficientes desde el punto de vista energético.
Debido también a esta eficiencia energética, hoy en día se utilizan cada vez más los diodos emisores de luz, conocidos como LED (Light Emission Diodes).
2. Filamentos de Bombillas LED
Las bombillas LED de filamentos son bombillas en las que el filamento se reproduce mediante LED. Las bombillas LED de filamentos se caracterizan por su escasa luminosidad.
La razón es que utilizan LED largos y finos como hilos. Además, muchos modelos no disponen de una pieza de disipación del calor llamada disipador. Se trata de una limitación de diseño que impide utilizar LED de muy alta potencia. Su uso principal es para iluminación suplementaria o conjunta.
Por otro lado, las bombillas LED generales pueden utilizar chips LED más grandes y, por lo tanto, suelen ser más brillantes que las bombillas LED Filamentos.
Las bombillas LED Filamentos tienen una vida útil más larga que las bombillas incandescentes o fluorescentes, pero más corta que las bombillas LED generales. En concreto, es de unas 15.000 horas. Dado que una bombilla LED típica dura entre 30.000 y 40.000 horas, es aproximadamente la mitad de la vida útil de una bombilla LED típica.
Principios de los Filamentos
Las bombillas incandescentes utilizan el principio del calor Joule generado al pasar una corriente eléctrica a través de los filamentos, que irradian calor y emiten luz. El calor Joule es la energía térmica que se genera cuando una corriente eléctrica pasa a través de un conductor.
Por lo tanto, para que la bombilla pueda utilizarse durante mucho tiempo, los Filamentos deben estar fabricados con un material de alta resistencia y gran resistencia al calor. De lo contrario, los propios Filamentos no pueden soportar el calor y se queman, quedando inutilizados como fuente de luz.
El tungsteno tiene un punto de fusión extremadamente alto de 3.653 K (3.379 °C), el más alto de cualquier elemento metálico. Por lo tanto, no se funde ni siquiera a altas temperaturas debido al calor Joule. Esta es la razón por la que el tungsteno se utiliza a menudo para los filamentos.
El interior de la bombilla está lleno de un gas inerte, lo que garantiza una larga vida útil de la bombilla. Sin embargo, el gas inerte también se desplaza para llevarse el calor de los filamentos (pérdida de calor) debido a la conducción y convección del calor en el propio gas. La relación entre el gas de inclusión y la pérdida de calor se muestra en la Fig. 2, donde cuanto mayor es el peso atómico del elemento, menor tiende a ser la pérdida de calor.
Más Información sobre Filamentos
1. Filamentos de Bambú
En 1879, Edison inventó la bombilla incandescente práctica. El material de los filamentos utilizado en aquella época era el bambú japonés. El bambú era adecuado como material de filamento por sus fibras gruesas, su resistencia y su longevidad.
Cuando se desarrolló por primera vez la bombilla, Edison utilizó un filamento hecho de hilo de algodón recubierto de hollín y alquitrán y carbonizado, y consiguió mantener la bombilla encendida de forma continua durante 40 horas. Sin embargo, a efectos prácticos, era esencial desarrollar una bombilla que se mantuviera encendida durante mucho más tiempo.
Con este fin, repitieron los experimentos utilizando como filamentos diversos materiales conocidos, como papel e hilo, para investigar la duración de la iluminación. En el proceso, encontraron un ventilador de recuerdo de Japón y fabricaron una bombilla utilizando el bambú como filamentos.
Cuando realizó experimentos de iluminación con esa bombilla, descubrió que podía alcanzar un nivel de practicidad, con una duración de iluminación superior a la de los materiales anteriores. Edison procedió entonces a realizar experimentos de iluminación con varios tipos de bambú de todo el mundo con el fin de encontrar el mejor bambú para los Filamentos.
Descubrió que cuando se utilizaba el bambú Hachiman de Kyoto, Japón, la luz permanecía encendida durante una media de más de 1.000 horas, lo que dio lugar a su aplicación práctica.
2. Filamentos e Hilados
El término filamentos se utiliza para referirse a la parte de la fuente de luz de una bombilla, y las fibras largas y continuas, como la seda, se denominan hilos filamentosos.
Filamento (en inglés: filament) es una palabra inglesa que originalmente significa fibroso. En cambio, el hilo hilado se fabrica alineando fibras cortas paralelas entre sí, como el hilo de algodón, y retorciéndolas hasta formar una sola hebra.
Hay dos tipos de filamentos: monofilamento y multifilamento. El primero se refiere a una sola hebra larga de hilo, como el sedal. El segundo se refiere a un solo hilo hecho retorciendo docenas de hilos juntos. En las fibras naturales, el hilo de seda entra en esta categoría. La seda cruda se fabrica desenredando los capullos exhalados por los gusanos de seda, y el hilo de seda se fabrica limpiándolos.
No existen tipos específicos de hilo hilado. La mayoría de las fibras naturales, como el algodón y el cáñamo, entran en esta categoría.