バイオマスボイラとは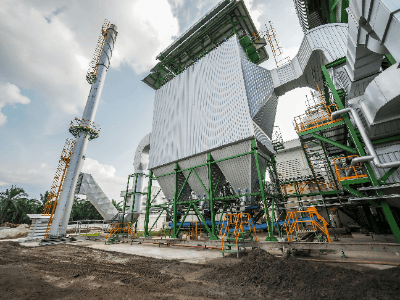
バイオマスボイラとは、木屑や紙屑、廃タイヤなどの産業廃棄物を燃料とし、水蒸気および温水などを生成する熱源機器です。
バイオマスボイラの使用用途
バイオマスボイラは様々な分野で使用されています。中でも代表的な使用用途は、小規模な発電システムです。
バイオマスボイラを使用した発電システムは、バイオマスボイラを利用して蒸気やガスを生成し、この蒸気やガスで発電機内のタービンを回転させて発電しています。水蒸気を生成するバイオマスボイラでは、例えば、1時間におよそ4トンの水蒸気を生成し、発電タービンを駆動させて300キロワットの電力を作り出すことも可能です。
バイオマスボイラでは蒸気だけでなく温水を作り出すことも可能で、農業施設の暖房や温浴施設への温水の供給に利用されています。さらにバイオマスボイラは、大規模な化学工場における蒸気や温水および熱水の供給源として、製材工場における乾燥装置の熱源としてなど、様々な工場に導入されています。
バイオマスボイラの原理
バイオマスボイラの燃焼方式は大きく分けて「直接燃焼方式」「熱分解ガス化方式」「生物化学ガス方式」の3種類です。それぞれの方式のバイオマスボイラが発電に利用されています。
1. 直接燃焼方式
直接燃焼方式は、木屑や間伐材、可燃性ごみなどのバイオマス燃料を直接燃焼させて蒸気および温水を生成する方式です。この方式のバイオマスボイラを発電機に利用した場合は、バイオマスボイラに生成された蒸気がタービンを回転させて発電します。
2. 熱分解ガス化方式
熱分解ガス化方式は、木くずや間伐材および可燃性ゴミなどを燃料として使い、直接燃焼させるのではなく加熱することによってガスを生成します。この方式のバイオマスボイラを発電機に利用した場合は、生成したガスによってガスタービンを回して発電します。
3. 生物化学ガス方式
生物化学ガス方式では、燃料として家畜の糞尿や生ゴミまたは下水の汚泥などを使用します。これらを燃やすのではなく発酵させることが特徴です。発酵によりメタンなどの可燃性のバイオガスを発生させ、これを燃焼させることで蒸気および温水を生成します。この方式のバイオマスボイラを発電機に利用した場合は、生成したガスによってガスタービンを回して発電します。
バイオマスボイラの大きな特徴は、燃料として化石燃料ではなく直接生物圏内にあるものを使用していることです。すなわち、燃料となる木くずなどが成長のために吸収した二酸化炭素と燃焼時に発生する二酸化炭素はプラスマイナスゼロになると考えられ、「カーボンニュートラル」を達成していると言えます。
バイオマスボイラのその他の情報
1. 木質バイオマスボイラ導入の留意点
木質バイオマスボイラを導入する際の留意点は、「燃料費」「設備費用」「燃焼灰の処理」の3つです。順番に説明します。
燃料費
木質バイオマスボイラは化石燃料ボイラと比較して、燃料費が安いといわれています。燃料は、林業から発生するもの、製造業 (木材加工) から発生するもの、建設業 (主に一般家屋建設) から発生するもの、産業廃棄物処理業から調達可能です。
設備費用
木質バイオマスボイラは、化石燃料と比較すると木材燃料の熱量が小さく品質にバラツキがあるため、同じ出力を得るためには設備費用が大きくなることになります。今後普及させるためには、技術的向上とともに、行政からの補助金を拡充することが望まれます。
燃焼灰の処理
木質燃料の場合、投入する燃料に対して10%前後の燃焼灰が発生します。日本の法律では、燃焼灰は産業廃棄物の分類です。このため、燃焼灰の処理のコストが掛かる問題が生じます。しかしながら、実際の判断は各自治体に委ねられており、自治体により異なる判断がされています。
2. 木質バイオマスボイラの燃料について
木質バイオマスボイラの燃料には、薪、木質チップ、木質ペレットなどがあります。薪は、伐採した木材を扱いやすい大きさに切断したもので、燃焼効率を上げるために乾燥させたものです指します。木質チップとは、林業や製造業、建設業から発生した木材端材を破砕したもので、薪よりも輸送し易くしたものです。
木質ペレットは、木質チップやおがくず等を小さく成形し燃焼しやすく加工したものです。それぞれ加工に係わる工数により価格が変わります。
3. 木質バイオマスボイラの可能性
木質バイオマスボイラは、風力発電や太陽光発電と同様に再生可能エネルギーに該当します。今後は世界的に再生可能エネルギーの割合増加が求められますが、他の再生可能エネルギーと比較して天候に左右されない点がメリットです。燃料調達他の課題が解決できれば、非常に有望なエネルギー源となります。
参考文献
https://www.jwba.or.jp/explanation/electricity/
http://www.kankyo.icross.co.jp/biomass/
https://www.jwba.or.jp/explanation/heat/
https://www.jwba.or.jp/database/list-small-woody-biomass-boiler/
https://w-pellet.org/pellet-2/