What Is a Polyethylene Pipe?
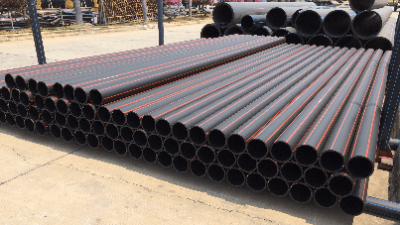
Polyethylene pipes are made of polyethylene (Figure 1). They are used for gas piping, chemical piping in chemical plants, and water supply and distribution pipes.
Polyethylene has excellent weather ability and chemical resistance, so there is no need to worry about red water caused by rust as is observed with steel piping. In addition, because polyethylene is a resin material, it is flexible, which has the advantage of making buried piping networks more resistant to earthquakes and other disasters. One of the major manufacturers of polyethylene pipes is Sekisui Chemical, which specializes in manufacturing and processing resin materials.
Uses of Polyethylene Pipes
Polyethylene pipes have been attracting attention in recent years mainly as infrastructure piping for delivering water and gas. Polyethylene pipes can be used in all applications except high-temperature fluids, such as water distribution pipes because they are rust-resistant and have excellent water hygiene properties, sewage pipes because they are chemically stable and do not cause blockages in pipes due to red rust, and air conditioning pipes because they are lightweight and can be quickly installed.
In addition, cross-linked polyethylene pipes can be used at temperatures of 95°C or lower for hot water supply without deterioration over a long period.
Features of Polyethylene Pipes
Compared to steel pipes conventionally used for buried pipes, polyethylene pipes are superior in that they do not rust, do not corrode even in corrosive soil or salt-affected areas, have excellent electrical insulation properties, do not cause electrical corrosion, and are less likely to become blocked due to scale adhesion.
The resin material also has the advantages of being lightweight for efficient transportation and installation, easy bending, and earthquake resistance due to its flexibility.
Pipe joints for polyethylene pipes include fusion joints, mechanical joints, and electro-fusion joints. Infusion joint joining, the insertion point on the polyethylene pipe side, and the receiving end on the joint side are heated in a heating machine to melt them and then joined.
Since this method requires control of the heating temperature, it is desirable to use a dedicated heating machine, and there are some problems in terms of workability. Electrofusion (EF), a type of electrofusion joining, is a method that overcomes this difficulty.
This method is very superior in terms of simplicity of operation, and heating is performed by energizing a joint with a built-in electric heating wire, which simultaneously melts and fuses the pipe and the joint, thereby completing a completely integrated joint.
Because of these advantages, polyethylene pipes are often introduced as an alternative to conventional steel piping and are expected to help build disaster-resistant cities, which have recently become more important in society, and ultimately help realize a sustainable society.
Polyethylene Dual Layer Pipes
A polyethylene dual-layer pipe is a polyethylene pipe consisting of two layers: an outer layer (polyethylene with carbon black) with high weather resistance and an inner layer (natural polyethylene) with high chlorinated water resistance, and is widely used mainly for water supply pipes, drainage pipes, temporary piping, and other water supply applications.
Its excellent flexibility allows it to flexibly follow ground subsidence, earthquakes, etc. It also has excellent chemical stability. It also has excellent chemical stability, so there is no risk of corrosion to the soil in which it is buried.
Furthermore, it is hygienic because no harmful additives are used. In this regard, the pipes are ideal for drinking water piping in terms of water quality retention and hygiene, as there is no rusting and very little scale adhesion.
The inner surface of this piping is extremely smooth and has low frictional resistance, resulting in very little scale adhesion. This pipe has an excellent characteristic of extremely low flow reduction over time.
Differences Between Polyethylene and PVC Pipes
Because both types of piping are made of plastic materials, these two materials are often confusedly understood, but it is important to note that their characteristics and applications are different.
As explained at the beginning of this article, polyethylene pipes are made of polyethylene and have excellent flexibility, making them very earthquake resistant when buried underground.
On the other hand, PVC pipes are pipes made of polyvinyl chloride, and although they have a certain degree of flexibility, the degree of flexibility is not as high as that of polyethylene pipes. Structural differences between polyethylene and polyvinyl chloride
Service Life of Polyethylene Pipes
Polyethylene pipes are known for their long service life. In Japan, there is a demand for water pipelines with a service life of 100 years or longer, and polyethylene pipelines for water distribution are also required to have high durability.
An example of a study in this regard is a 2013 report by the Polyethylene Pipe System Association for Water Distribution (POLITEC). This study examined verification against internal and external pressure, earthquakes (seismic resistance), and residual chlorine (chlorinated water resistance). As a result, the results of all verifications exceeded 100 years under the specified assumed conditions, indicating that polyethylene pipelines for water distribution have a service life well in excess of 100 years.
High-Density Polyethylene Pipes
Polyethylene pipes made from high-density polyethylene (polyethylene with a density of 0.942-0.970) have excellent impact resistance and flexibility (bending and flexing characteristics).
Therefore, the pipes are resistant to damage even in the event of a disaster. Because of these excellent physical properties, the material is used in the fields of civil engineering, agriculture, and mining, including drainage pipes for longitudinal road crossings, canal rehabilitation, small-scale canal culvert conversion, various rainwater drainage works, and industrial waste disposal sites.