What Is a Flexible Hose?
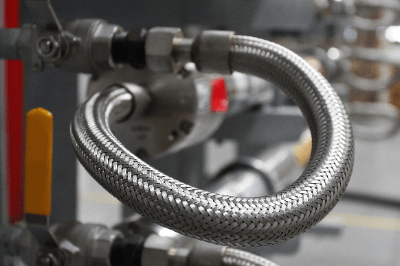
A flexible hose (flexible tube) is a hose that can be bent freely.
The materials used include rubber, plastic, and fluoroplastic, but in most cases, the term “flexible hose” refers to hoses made of metal. Most flexible hoses made of metal have a wavy structure called bellows.
Bellows are piping made by bending metal into a jagged shape, which allows even hard-to-bend metal pipes to be bent flexibly.
Uses of Flexible Hoses
Flexible hoses are used for piping in factories and for connection to vibrating devices such as mobile equipment and pumps. They are used not only for industrial applications but also for household gas and water piping.
Other applications include the middle section of automobile exhaust pipes, vacuum piping for semiconductor manufacturing equipment, and sprinkler connections for firefighting piping.
Flexible hoses are used not only for water but also for other liquids and gases. Because it can be bent, the hose can be freely installed. The material of the hose is selected according to the liquid or gas to be flowed through the hose, and flexible hoses made of fluorocarbon resin may be used for highly corrosive liquids or gases.
Principle of Flexible Hoses
Flexible hoses are used in a wide range of situations by taking advantage of their flexibility, as described above. The following characteristics are demonstrated in each usage scenario.
1. Simplification of Piping Work
Used in locations where straight piping cannot be connected or where intricate piping connections are required. Even a slight misalignment in rigid piping makes it difficult to connect, but flexible hoses make it easy to do so.
2. Displacement Absorption
When a hose expands, contracts, or becomes eccentric due to aging deterioration of equipment or ground subsidence, the connection part or the hose itself is loaded if it is a normal hose. (Elongation refers to a change in the length of a straight hose relative to the direction of extension, while eccentricity refers to a change in the direction perpendicular to the direction of hose extension.) The use of flexible hoses can absorb such displacement.
3. Vibration Absorption
When a hose is connected to equipment that constantly vibrates, such as a pump, the vibration places a load on the hose itself and its connections. Flexible hoses absorb the vibration, thereby reducing the load on the equipment and, as a result, contributing to extending the service life of the equipment. It also absorbs shaking during earthquakes to reduce damage to equipment.
4. Absorption of Thermal Expansion of Piping
Rigid metal piping does not appear to expand or contract at first glance, but it actually expands and contracts slightly due to rapid temperature changes. Because it is a rigid structure, the slightest change in size can lead to loading. Since flexible hoses are themselves expandable and contractible components, they can accommodate such expansion and contraction.
Structure of Flexible Hoses
Normally, metal is too rigid to be bent and stretched, but flexible hoses can be bent freely and used as hoses.
Typical flexible hose structures and features are described below.
1. One-Pitch Type
As mentioned at the beginning of this section, it has a structure called bellows. It is a thinly stretched piping formed into a structure with continuous peaks and valleys like an accordion. It is easy to understand if you imagine a folded straw. Each mountain is independent and separated by a valley.
2. Annular Type
Similar to the one-pitch type, there are mountains and valleys, and each mountain is independent. However, in the one-pitch type, the mountains are U-shaped, whereas in the annular type, the mountains are omega-shaped. The feature of this type is that each mountain is independent, which reduces twisting at the neck.
3. Spiral Type
The U-shaped mountains are formed in a continuous spiral shape. The spiral structure is characterized by its resistance to liquid accumulation.
4. Blade Type
Instead of the structure of peaks and valleys, as described so far, this type has a tubular structure made of thin metal wires woven together like fibers of clothes.
Not only the above structures but also combinations of them are made. In many cases, a one-pitch or spiral type hose is reinforced on the outside with a braid type to create a double structure, making the hose both flexible and durable.
Other Information on Flexible Hose
1. Features of Flexible Hoses
Flexible hoses are characterized by their strength and pressure resistance, improved heat resistance, flexibility, ability to accommodate large displacements and effectiveness in preventing the transmission of equipment vibration.
- High Performance
By covering the outer surface of the flexible tube with a braided metal layer, strength, and pressure resistance are increased without compromising flexibility. Applicable fluids include gases such as air, various gases, and steam; liquids such as water, oil, solvents, chemicals, blood, and seasonings; and various powders. They can also be used in a wide range of temperatures, from low to high. Some can be used at several hundred degrees.
- Capable of Handling Large Displacements
Flexible hose blades can handle large displacements. These include hydraulic and pneumatic equipment with moving parts, robots, and automobile wheel brakes. They can also be used in seismic isolation equipment and underground piping to reduce damage caused by ground movement during earthquakes.
- Vibration Countermeasures
Flexible hoses are used in connection pipes for pumps, compressors, exhaust pipes, etc. Vibration transmission from equipment is suppressed.
2. Blade Type
When the blades are stainless steel, three main types are used.
- Wire Blades
Wire blades are made of stainless steel wire, with several wires bundled in parallel and braided into the outer surface of the tube. It has excellent flexibility and can absorb displacements that are frequently repeated. Also called round wire braid or wire braid.
- Strip Braid
Strip braid is made of stainless steel plates cut into strips and manually braided into the outer surface of the tube in the shape of a bamboo basket. Compared to wire braid, it has superior strength against internal pressure, but less flexibility, making it suitable for absorbing displacements with low repetition frequency. Also called plain wire braid or ribbon braid.
- Twill Weave Braid
The Twill weave braid is made by braiding the wire into flat plates, which are then woven into the outer surface of the tube. It has high durability and flexibility. It can be used for long lengths of piping but is the most expensive type of braid.