What Is a Raman Microscope?
A Raman microscope (or Raman microscope) is a measurement instrument that combines a Raman spectrometer and an optical microscope.
It allows non-destructive analysis of detailed information on materials such as chemical structure, intermolecular interactions, and crystallinity. By combining a Raman microscope with a Raman spectrometer, it is possible to observe an object under the microscope and measure selected points, or to obtain an image visualizing the distribution of composition.
Uses of Raman Microscopes
Since Raman spectroscopy is based on chemical bonding, the following information can be obtained by measurement
- Chemical structure
- Phase, polymorphism
- Strain
- Impurities, contamination
Since Raman spectra are unique to each substance, they can be used to quickly identify a substance or distinguish it from other substances. Raman microscopes can also be used to analyze many different samples. In general, it is not suitable for the analysis of metals and alloys, but for the analysis of:
- Solids, powders, liquids, gels, slurries, and gases
- Inorganic, organic, and biological materials
- Pure chemicals, mixtures, and solutions
- Metal oxides and corrosion
Typical examples of where Raman microscopes are used include:
- Characterization of pigments, ceramics, and gemstones in the fields of art and archaeology
- Evaluation of the structure and purity, defects, and disorder of carbon material nanotubes
- In chemistry, structure, purity, and reaction monitoring
- In the life sciences, single cells and tissues, drug interactions, and disease diagnosis
Structure of Raman Microscopes
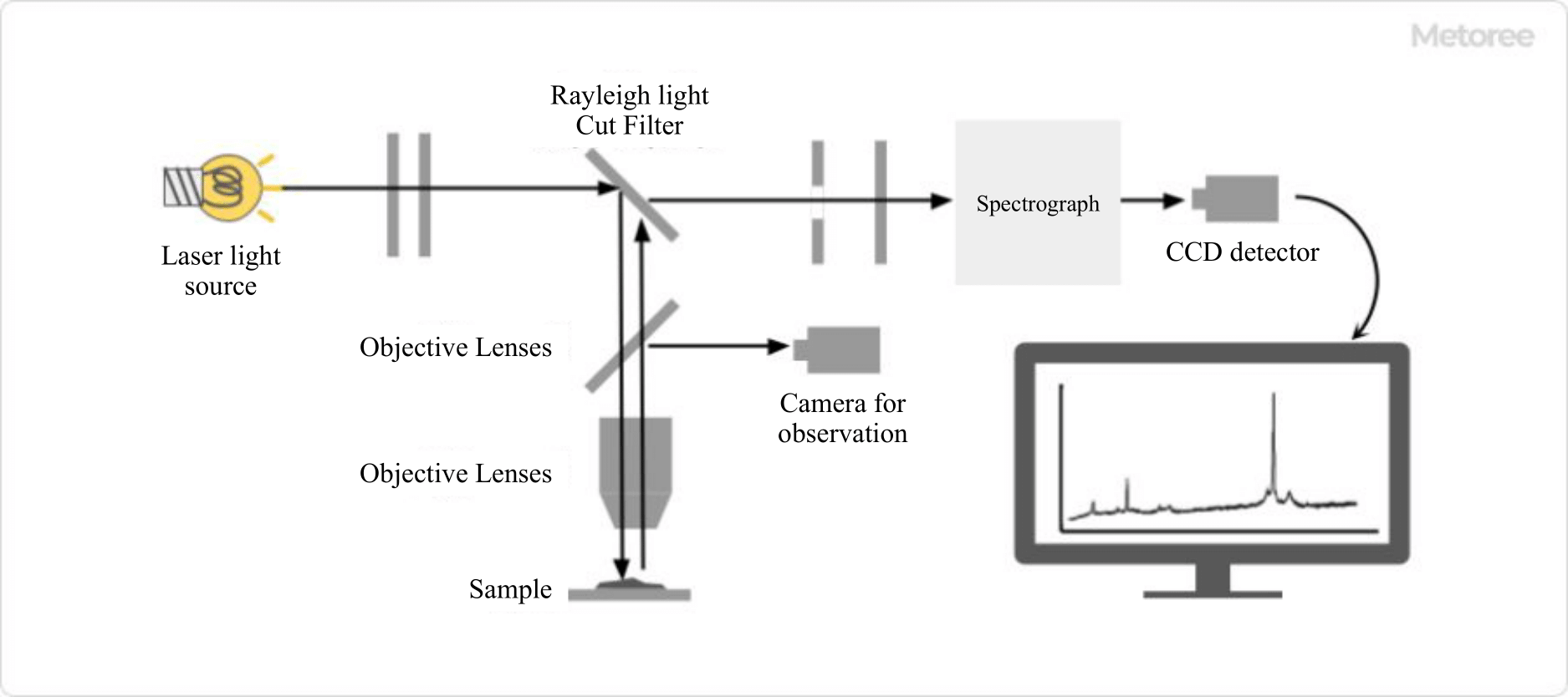
Figure 1. Structure of Raman microscope
The Raman microscopes are measuring instruments that combine a Raman spectrometer and a microscope.
Irradiated light from a laser source is guided to the sample through the objective lens of the microscope and irradiated onto the sample. The scattered light generated from the sample is focused by the objective lens, and only the Raman scattered light is detected through a Rayleigh light cut filter.
Principle of Raman Microscopes
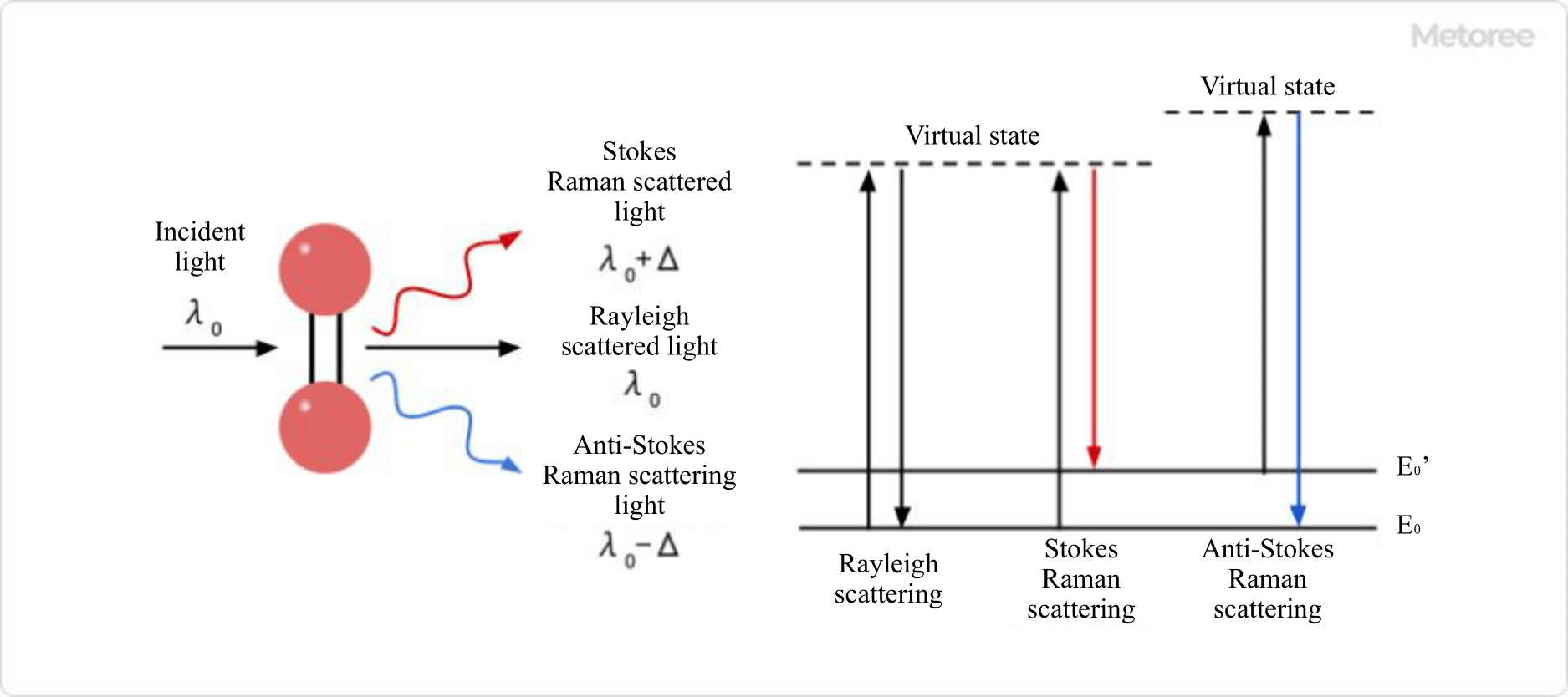
Figure 2. Raman scattering
When a material is irradiated with light, a scattering phenomenon occurs. Most of the scattered light is Rayleigh scattered light with the same wavelength as the irradiated light, but some scattered light with slightly different wavelengths from the irradiated light is included, and this scattered light is called Raman scattered light.
There are two types of Raman scattering light: Stokes scattering light, which has a wavelength longer than that of the irradiated light, and anti-Stokes scattering light, which has a shorter wavelength.
Raman scattering light is produced as a result of the interaction of irradiated light with a material, and the difference in wavelength between Rayleigh scattering light and Raman scattering light corresponds to the energy of molecular vibration of the irradiated material. It is known that only Raman-active vibrational modes are responsible for Raman scattering, and it is possible to infer or simulate Raman-active vibrational modes from molecular structures.
A similar analytical instrument that uses molecular vibration is the infrared spectrophotometer, but there are differences in the molecular vibrations that can be measured, making it a complementary analytical instrument.
Different types of molecules and different bonding states produce different molecular vibration energies, resulting in different Raman spectra. Substances can be identified by comparing the peak positions and relative peak intensities of the Raman spectra with those of known substances. It is also often used for qualitative analysis by interpreting the following:
- Peak position
Chemical bond information
- Peak Shift
Information on intermolecular interactions, stress, and strain
- Spectral waveform
Molecular structure information, crystal structure differences
- Half value width
Difference between crystalline and non-crystalline
Quantitative analysis is also available by utilizing the fact that the intensity of the spectrum is proportional to concentration.
Other Information on Raman Microscopes
1. Cautions for Raman Microscopes
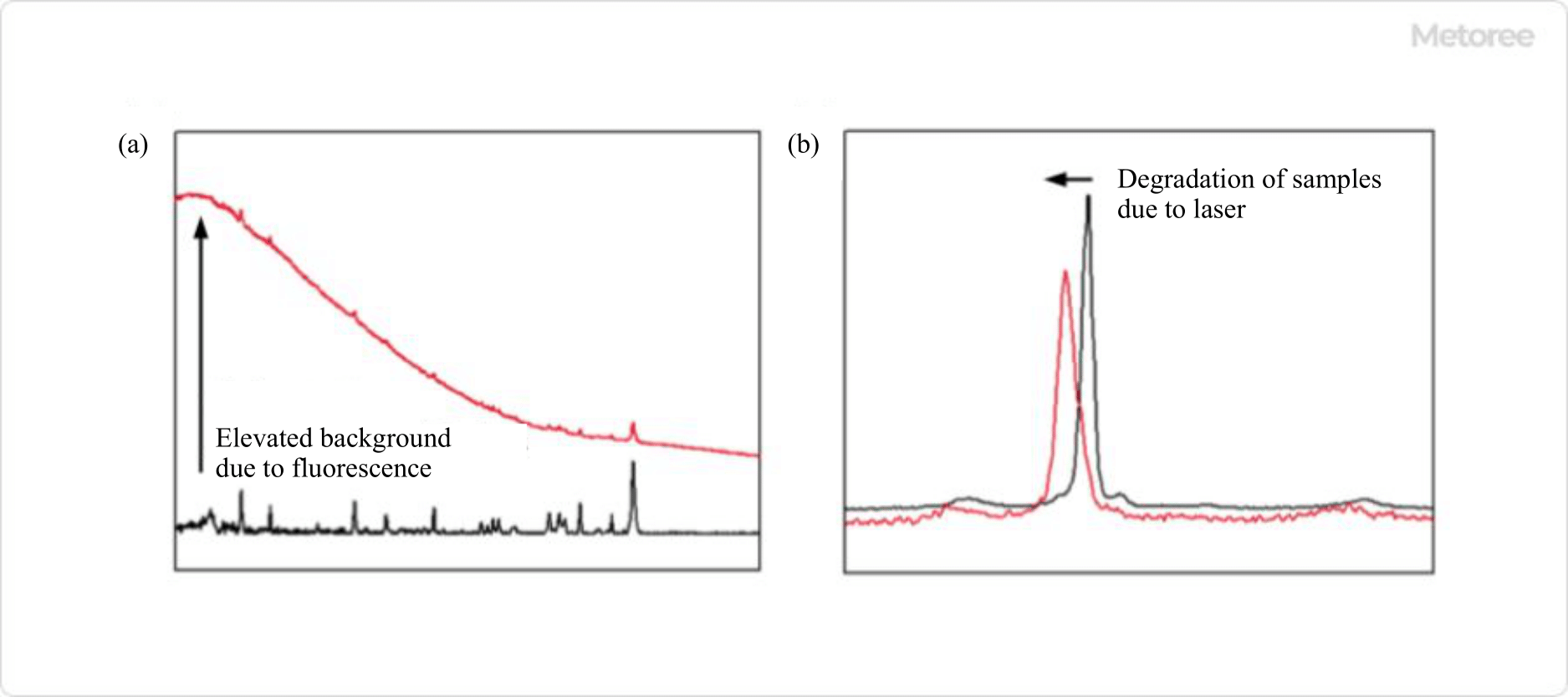
Figure 3. (a) Effect of laser irradiation on fluorescence generation (b) Degradation due to laser irradiation
Since Raman scattering light is weaker than Rayleigh scattering light, a certain intensity of laser light is necessary, but the laser light may cause problems. If the wavelength of the laser light overlaps with the absorption region of the molecule to be measured, the molecule will fluoresce and the background of the Raman spectrum will increase, burying the spectrum to be obtained.
To avoid this, it is necessary to take measures such as adjusting the exposure time and other measurement conditions, adjusting the depth of focus, narrowing the spectral slit, and using a confocal filter (DSF). Other ways to suppress fluorescence include changing the laser source.
For organic materials, fluorescence often occurs when using the common 532 nm laser light, so a longer wavelength laser light, such as 785 nm, is sometimes selected. However, care must be taken when changing to a longer wavelength laser light, as the sensitivity of some monochromators and detectors may decrease drastically.
If the material to be measured is organic or carbon material, depending on the intensity and duration of the laser light, the material may be “burnt” and degraded. To prevent degradation of the measured material, the measurement conditions can be adjusted by lowering the laser intensity or shortening the exposure time.
In addition, some carbon materials are photo-reactive, meaning that they react to the irradiated laser light. Such materials can be handled by adjusting the measurement conditions in the same way, or by changing the wavelength of the laser light to suppress the photoreaction.
2. New Raman Microscopes Technology
Various techniques have been developed to improve the sensitivity and resolution of Raman microscopes.
Surface-enhanced Raman (SERS) and Tip-enhanced Raman (TERS) make use of a phenomenon called localized surface plasmon resonance that occurs at metal surfaces, allowing measurement of larger intensity of Raman scattered light and higher sensitivity and spatial resolution.
Coherent Anti-Stokes Raman Scattering (CARS) and Induced Raman Scattering (SRS) are types of nonlinear Raman scattering, in which two different wavelengths of light are used simultaneously to obtain spectra with signal intensities that are many orders of magnitude higher.
Other techniques have also been developed that allow Raman imaging to be performed more quickly, such as using a beam splitter to obtain a Raman spectrum in a linear or planar form with a single laser pulse.