What Are Metallographs?
Metallographs, also known as projection microscopes or falling-glass microscopes, are a type of optical microscope.
In general, most of what is called industrial microscopy refers to metallographs. Although the name metallurgy is given to it, it is used to observe the surface of samples that are difficult for light to penetrate, such as metals, ores, ceramics, semiconductors, and so on.
Metallographs use light reflected from the sample to produce a magnified image. Similarly, a stereo microscope uses light reflected from a sample to obtain a magnified image.
Uses of Metallographs
Metallographs are used to observe metallographic structures and alloys, ceramics, semiconductors, plastic electronic components, rocks, and ores.
Specific applications are as follows:
- Observation of changes in the state of raw materials before and after physical or thermal processing at metal casting, refining, metallurgy, etc.
- Inspection of defects such as minute dents and scratches that cannot be seen with a stereo microscope at processing sites for plastics and semiconductor products, etc.
- Quality control at production sites in the precision machinery industry, electrical and electronic industries, etc.
- Research or education in metallography, mineralogy, etc.
Principle of Metallograph
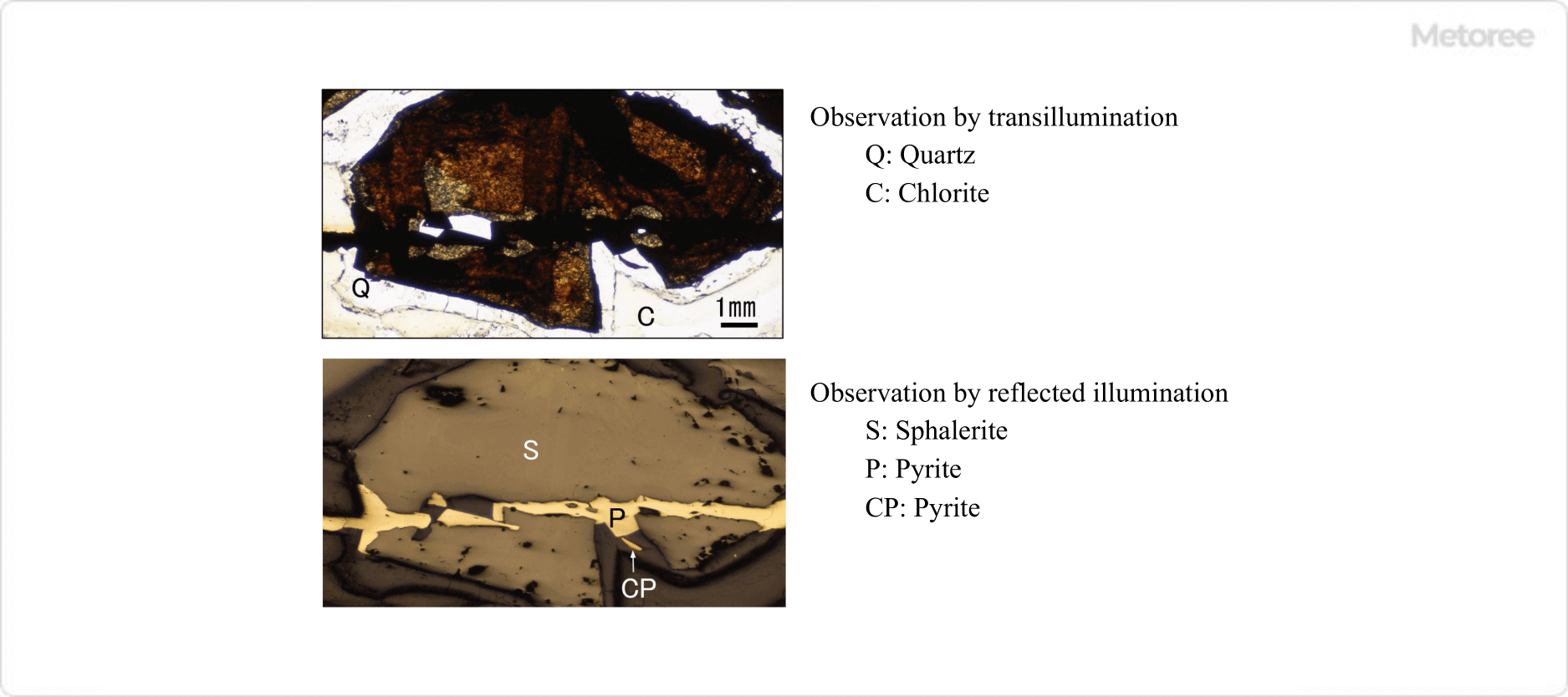
Figure 1. Images of the same field of view observed with transillumination and reflected illumination
The most significant difference between transillumination and reflected illumination observation is that areas that appear dark in transillumination appear bright in reflected illumination. Therefore, information that could not be seen with a biological microscope can be compensated for with a metallograph.
An ordinary optical microscope for observing microorganisms and cells is also called a transmission optical microscope because the light transmitted through the sample is magnified by the objective lens and eyepiece.
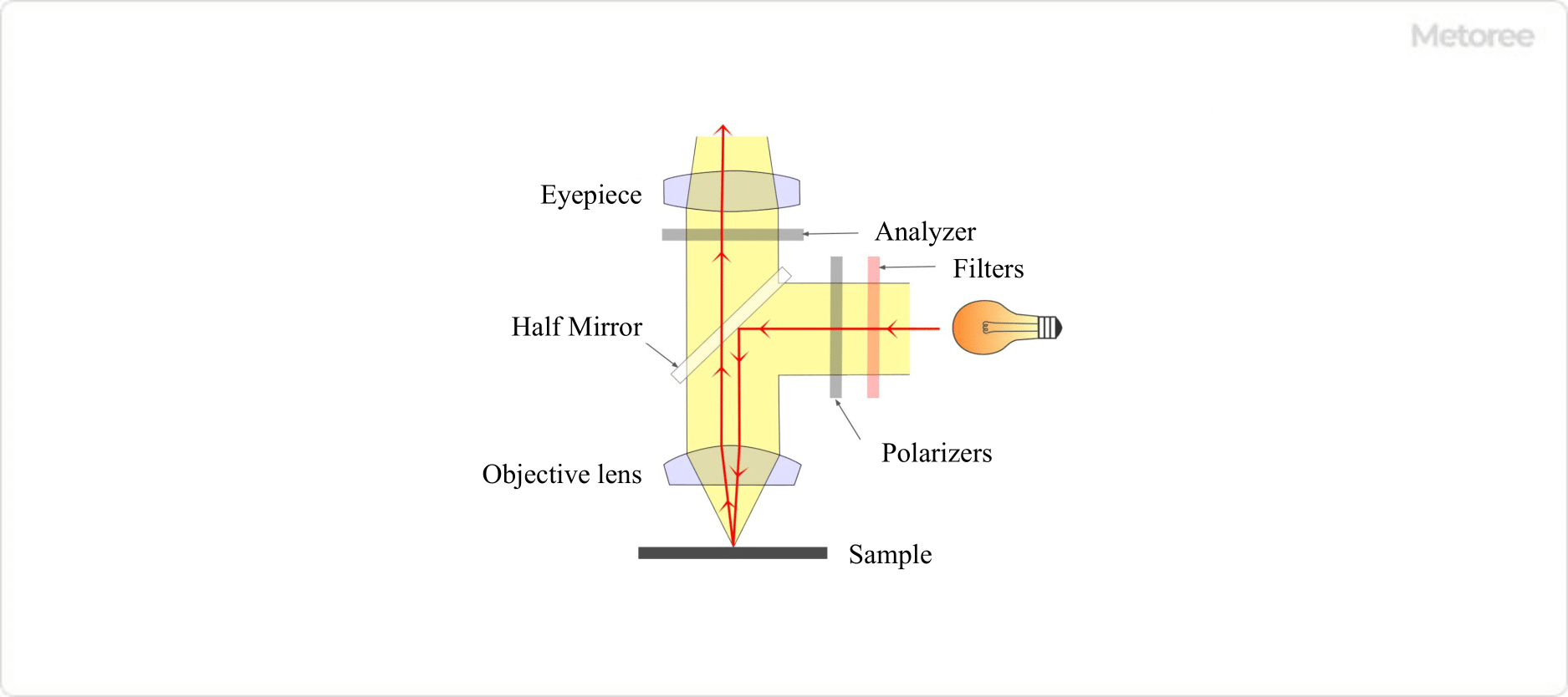
Figure 2. Illumination optics (Polarized light observation specification)
Metallographs are also a type of optical microscope and have the same general structure as biological microscopes, but they have a unique structure for observing specimens that light cannot penetrate at high magnification. In this optical system, light emitted from the light source is reflected by a half-mirror and reaches the sample for observation through the objective lens, and the reflected light from the sample is observed by the human eye through the objective lens and eyepiece.
How to Select a Metallograph
There are various types of metallographs, ranging from portable ones which can be relatively cheap to larger ones which can be expensive when options such as lens sets and imaging equipment are included.
When selecting a metallograph, it is important to first clarify the purpose of use. When making the actual selection, consider the following points:
- If you prefer the sample surface to face downwards, or if you want to exchange samples quickly, choose an inverted type with the mirror body below the sample; otherwise, choose an upright type.
- If you intend to observe polarization characteristics such as optical anisotropy of the sample, select a polarizing microscope that comes standard with a polarizing filter set.
- If you also wish to perform transillumination observation, a microscope that can instantly switch between transillumination and reflection illumination with a single touch is optimal.
- If you want to frequently take pictures and movies of the observed images, a trinocular type that allows binocular observation with a camera attached is most suitable.
- If you want to move a sample precisely at a high magnification of more than 100x, select a stage that meets your purpose, such as a mechanical stage or an XY stage.
Other Information on Metallographs
Metallographs are available with the same filters as biological microscopes to help you observe the optical properties of your samples in detail.
Color temperature conversion (LB) filters
The color temperature of a sample varies depending on the type of lamp used as the illumination source, so the color of the sample to be observed depends on the light source. In optical microscopy, the color of a sample is one of the most important factors to observe.
In order to correctly compare the color of a sample with the color described in literature, it is necessary to observe the sample at the same color temperature. Therefore, a color temperature conversion filter is used to achieve the same color temperature as sunlight, which is the most universal light source.
Color Correction (CC) Filters
Color correction (CC) filters are used to adjust the intensity of the three primary colors of light (red, green, and blue) or the three primary colors of color (cyan, magenta, and yellow).
Polarization Filter
Polarizing filters are a set of polarizers placed immediately after the light source (in front of the sample) and an analyzer placed between the sample and the eyepiece. The polarization filters are used to determine the change in polarization state when polarized light that has passed through the polarizer is reflected by the sample.
Since the polarization state changes depending on the crystal structure of the sample and other factors, the polarization filter can be used to determine the optical properties of crystals and the internal structure of polymers.
2. Preparation of Samples for Metallograph
When observing with a metallograph, the specimen surface must be smooth and set so that the light from the objective lens enters the specimen perpendicularly. Microscopic observation with reflected light provides strong contrast in the case of scratches on the specimen surface, but it is often impossible to distinguish differences in the optical orientation of crystals or slight differences in composition.
Therefore, unless the surface is smooth without processing, the specimen may need to be cut and polished before observation, or an etching process may be required to make difficult-to-see microstructures easier to see.
Preparation of Polished Specimens
Diamond cutters and polishing equipment are used to cut and polish specimens to the appropriate size. In addition, special polishing flakes are required for mineralogical studies, for example, when it is necessary to switch between transmitted and reflected illumination observation. The creation of polishing flakes can be automated to some extent, but sufficient experience and knowledge are required for the creation of polishing flakes.
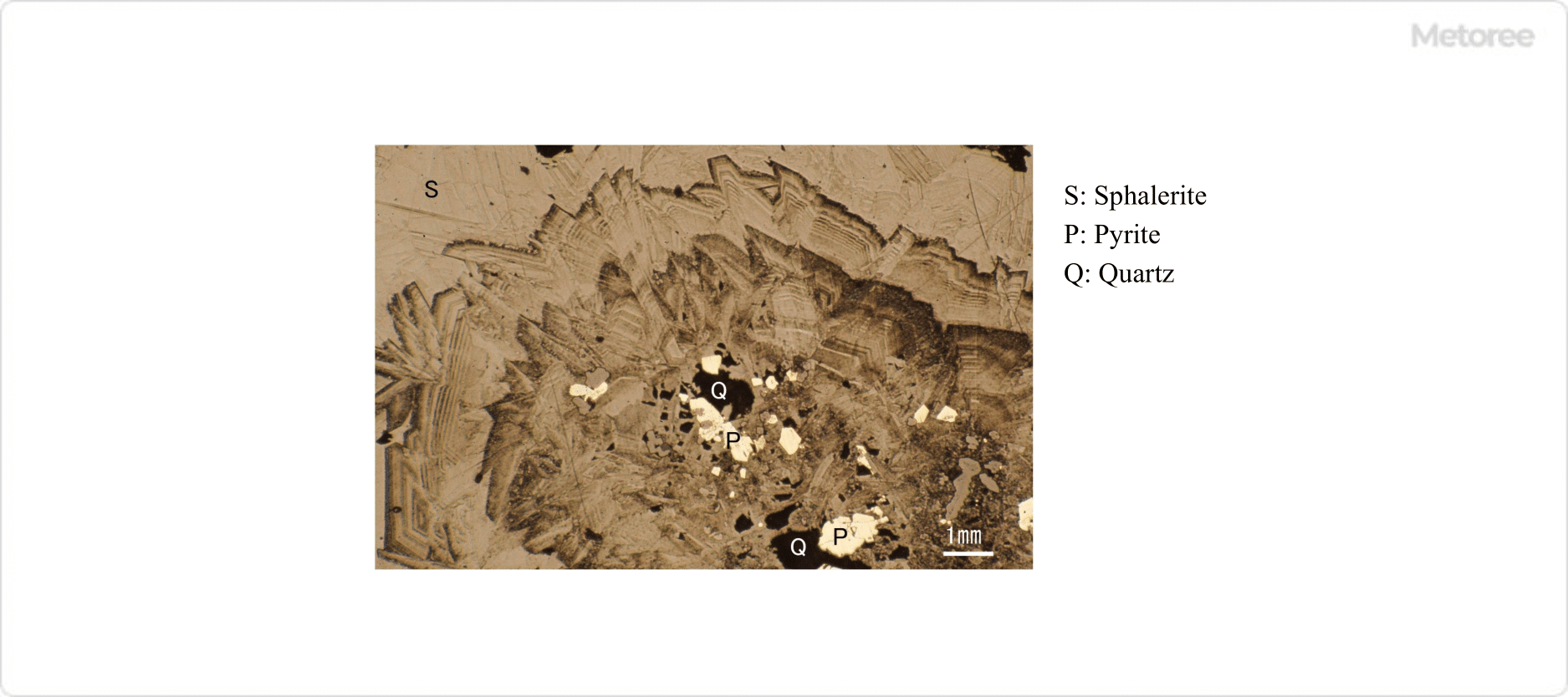
Figure 3. Growth pattern in sphalerite after etching with nitric acid
When grain boundaries or microstructures that should be present are not visible, etching of the sample surface can often solve the problem. There are two types of etching methods: chemical etching with acid and electrolytic etching.