What Is a Fresnel Lens?
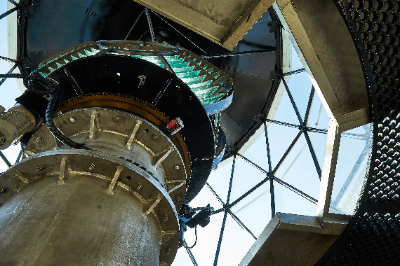
Fresnel lenses differ from ordinary spherical or aspherical lenses as they are flat and feature numerous concentric grooves engraved on one side of a plastic sheet.
The cross-section resembles the teeth of a saw. The name “Fresnel” originates from Augustin Jean Fresnel, a 19th-century French physicist who invented this type of lens.
Compared to conventional lenses, Fresnel lenses are lighter and thinner, resulting in cost savings.
Applications of Fresnel Lenses
Fresnel lenses are frequently employed when large lenses are needed, owing to their lightweight characteristics.
Historically, Fresnel lenses were used in lighthouses, where very large lenses were required, but traditional lenses would have been exceedingly thick and heavy. Nowadays, Fresnel lenses are also used as illumination lenses for camera flashes and viewfinder field lenses in single-lens and twin-lens reflex cameras.
They are also utilized in simpler magnification devices like loupes and magnifying glasses.
Principles of Fresnel Lenses
The grooves on Fresnel lenses are crucial for their optical function, similar to regular optical lenses.
In a conventional curved lens, incident light is refracted to form an image. In contrast, Fresnel lenses use their grooves to refract and focus incoming light. This allows thinner and lighter Fresnel lenses to achieve similar or better light-collecting capabilities compared to traditional lenses.
By adjusting the groove depth and quantity, it’s possible to achieve a shorter focal length than the aperture diameter, a feat not achievable with typical spherical lenses.
The majority of Fresnel lenses are constructed from materials such as glass or resin (acrylic, polystyrene, polycarbonate).
Acrylic Fresnel lenses are popular due to their high transmittance in the visible and ultraviolet spectra, while polycarbonate lenses are used in harsh environments due to their exceptional impact and heat resistance.
Advantages and Disadvantages of Fresnel Lenses
Despite being thinner and lighter, Fresnel lenses have drawbacks in terms of image formation compared to singlet lenses. This is primarily because the grooves on Fresnel lenses are visible, and they introduce diffraction effects, causing light leakage in nearby regions and resulting in blurred images.
However, it’s worth noting that diffraction, although considered a disadvantage in some cases, can be advantageous. Diffractive lenses actively exploit diffraction phenomena for specific applications.
Fresnel lenses and diffractive lenses share similar structures, often leading to confusion, but their underlying physical phenomena differ.
Fresnel Lenses in Illumination
Fresnel lenses find applications in various fields, with LED lighting being a prominent example. In recent years, they have been used as condenser lenses for solar panels, projector screens, optical sensors, and more.
When employed as lighting lenses, Fresnel lenses are often used to emit collimated light by placing a light source at the focal distance position. They are ideal for soft and controlled illumination of specific areas, commonly used in stage lighting and outdoor events.
While they may not match singlet lenses in image formation, they exemplify the use of diffraction to achieve distinct optical effects.
Linear Fresnel lenses are akin to Fresnel lenses for illumination. While Fresnel lenses are spherical with concentric grooves, linear Fresnel lenses are cylindrical lenses arranged in a plane. They are suited for collecting and diffusing light in a single direction, making them suitable for linear light sources.