What Is a Polyphenylene Sulfide (PPS) Resin?
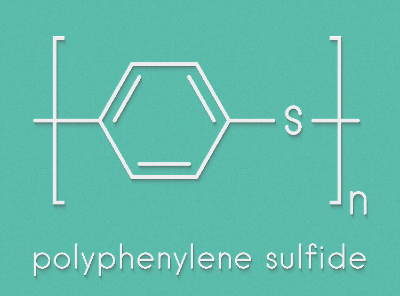
Polyphenylene sulfide (PPS) resin is a thermoplastic resin characterized by a structure of alternating benzene and sulfur bonds. It is esteemed as a super engineering plastic due to its outstanding properties. The mechanical strength and other characteristics of PPS can be modified with different fillers, leading to its widespread use as a reinforced resin, typically with about 30% glass fiber composites.
Its growing popularity across various industries stems from its well-balanced properties, including excellent moldability, processability, heat resistance, mechanical strength, dimensional stability, flame resistance, and chemical resistance.
Uses of Polyphenylene Sulfide (PPS) Resins
PPS resin, a super engineering plastic, is utilized in automotive parts, electronic parts, and medical equipment parts, among other high-performance applications. Notably, nearly half of the PPS resin market is dedicated to automotive parts.
As hybrid vehicles increasingly employ PPS resin components, its demand is expected to rise. In non-automotive sectors, PPS is essential for electronic components like IC chips, due to its superior dimensional stability and insulation properties. Its excellent heat and flame resistance makes it ideal for filter manufacturing as well.
Principle of Polyphenylene Sulfide (PPS) Resins
PPS resin is typically produced by a polycondensation reaction of paradichlorobenzene and sodium sulfide in a polar solvent, under high temperature and pressure. The polymerization process involves dehydration and dephosphorization reactions. Cross-linking in the resulting polymer greatly influences its properties, making the distinction between cross-linked and linear PPS resin critical for various applications.
1. Crosslinked Polyphenylene Sulfide (PPS) Resin
Crosslinked PPS resin, formed by heat treatment in an oxygen atmosphere during synthesis, allows molecular weight control by incorporating oxygen into the polymer chain. This results in a cross-linked structure with high rigidity and creep deformation resistance, even in high-temperature environments.
2. Linear Polyphenylene Sulfide (PPS) Resin
Linear-chain PPS resin retains its linear structure without undergoing special heat treatment. This type of PPS has lower rigidity but improved toughness and elongation compared to cross-linked PPS. It allows for high-purity synthesis and achieves superior moisture absorption resistance, electrical insulation, and dimensional stability.
Types of Polyphenylene Sulfide (PPS) Resin
1. Unreinforced Polyphenylene Sulfide (PPS) Resin
Unreinforced PPS consists purely of PPS resin without additional reinforcing materials like glass or carbon fiber. It’s widely used across various industries thanks to its impressive properties, especially its remarkable heat resistance. Unreinforced PPS maintains stable performance even under high temperatures, making it suitable for high-temperature industrial applications such as engine parts, exhaust system components, and boiler parts.
2. Reinforced Polyphenylene Sulfide (PPS) Resin
Reinforced PPS resin, created by adding materials like glass or carbon fiber to PPS, offers enhanced strength and rigidity. It’s ideal for components needing impact resistance. In the automotive sector, it’s used for engine parts, exterior parts, and suspension components, where durability and rigidity are paramount. Its excellent performance under severe conditions like high temperatures, vibration, and friction makes it especially valuable.
3. Polyphenylene Sulfide (PPS) Resin for Electrical and Electronic Applications
This type of PPS resin, known for high electrical insulation, is crucial in the electrical and electronics fields. It’s used in printed circuit boards, connectors, terminal blocks, motor parts, transistors, and IC packages. Suitable for high-temperature operations, it maintains stable electrical properties under such conditions and offers excellent chemical resistance.
4. Alloy-Reinforced Polyphenylene Sulfide (PPS) Resin
Alloy-reinforced PPS is a blend of PPS with other materials to enhance specific properties, making it suitable for applications that require lubricity and wear resistance. By incorporating elements like graphite and mineral fillers, this variant improves friction and wear resistance. It’s particularly effective in automotive and mechanical parts that endure high friction and temperatures.