What Is a Buret?
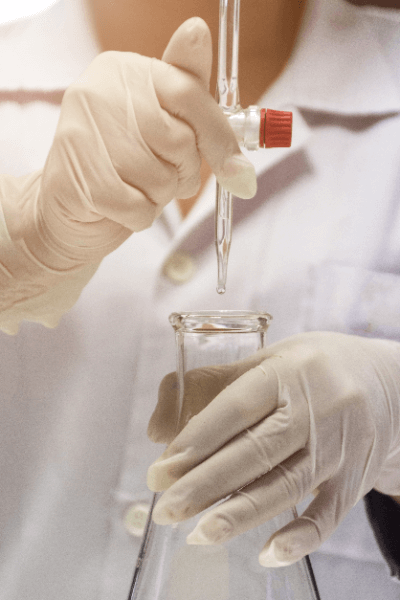
A buret is a glassware that can measure the volume of liquid dropped by dropping a small amount of liquid while operating it with a cock.
A removable cock is attached to the bottom of a thin, tubular glass tube with a scale on it, and the amount of liquid dropped is adjusted by turning the cock.
A pipette can also be used to measure the volume of a dropped liquid, but the buret can be used in a vertical position, so the scale can be read more precisely and the amount of liquid can be adjusted finely with the cock. Moreover, since the volume of a drop can be precisely controlled with a cock, the buret is suitable for experiments that require accurate liquid volume measurement, such as neutralization titration.
Uses for burets
Buret is mainly used for neutralization titration. Neutralization titration is a type of volumetric analysis, in which the concentration of a solution of unknown concentration is determined using a standard solution of known concentration and a solution of unknown concentration that reacts in proportion to the concentration of the standard solution.
The judgment of the neutralization reaction, the so-called endpoint, is determined by the color change of the mixed solution after dropping. Although the operation of the cock requires a certain degree of skill, an automatic operation called auto-buret is also available and is used for quality control in the food, pharmaceutical, and chemical industries.
Features of burets
Burets are available in white and brown. As with other glassware, some substances react with light, so the choice should be made according to the type of substance dissolved in the standard solution. For example, silver nitrate is photosensitive and must be used under a light-shielded condition, so a brown buret must be used when using it as a titrant.
Also, as mentioned above, it is important to become familiar with the buret’s cocking operation. If the speed of dropping liquid from the buret is too fast, there is a possibility of adding more standard solution than the endpoint. In addition, it is necessary to grease the cock part for maintenance, and if maintenance is insufficient, liquid may leak, etc.
Furthermore, if the tip is chipped, it is impossible to accurately measure the volume, so it must be handled with care. Experiments have shown that even a scratch on the tip can change the volume per drop. It is also known that the volume of residual liquid in the buret changes the volume of the residual drop, so it is advisable to always use the buret from the top of the scale, which is the zero point.
Since the buret is glassware, repeated heating and cooling deforms it, which impairs the accuracy of its measurement volume. Therefore, heating and drying after washing should be avoided, and the buret should be dried at room temperature. For the same reason, the titrant to be placed in the buret should be a liquid with a constant temperature of about room temperature. The temperature of the titrant should be considered not only because it causes expansion and deformation of the buret, but also because the volume of the titrant is temperature-dependent. For this reason, the titrant should be at a constant temperature for accurate volume measurement.
Why co-wash a buret?
Co-washing is the process of washing a buret, a whole pipette, or another side vessel instrument (an instrument used to measure the volume of a liquid) with the solution to be weighed (the solution to be placed inside).
To avoid volume changes due to deformation of the instrument, side vessel instruments are usually not heated and dried in a dryer. After washing with tap water, they are rinsed with distilled water and washed with the solution to be weighed immediately before use.
The reason for co-washing is that the concentration of the sample solution decreases when the inner surface of the instrument is wet with water. On the other hand, if the sample solution itself is wet, the concentration does not change when the solution is added.
Since a buret is used to put in a solution of unknown concentration during titration, if the concentration of the solution changes inside the buret, it will be impossible to obtain an accurate concentration.
Also, if you co-wash the apparatus once used again, you can continue to use it without letting it dry out.
First, fill the buret about 1/5 of the way with a solution and wash the inner walls while turning the buret on its side. Next, turn the cock to let the solution out of the tip, wash the inner wall below the cock, and discard the remaining solution from the top. This process is repeated several times.
How to use the buret
Fix the buret vertically to the buret stand and make sure the live plug is closed.
Using a funnel, pour the solution from the top of the glass tube. To prevent the solution from overflowing from the top of the funnel, leave a gap between the funnel and the top of the buret to allow air to escape. Also, to prevent the solution from getting into the eyes, pour the solution below eye level. After pouring the solution, remove the funnel.
Open the stopper with a beaker or other container underneath, and pour out the solution vigorously to completely expel air bubbles from the area below the stopper. If there are air bubbles above the stopper, remove them as well.
After the air has been expelled, read the scale and record the reading. The bottom (lower end) of the “meniscus” should be read, with the buret perpendicular to the line of sight. The meniscus is the curved surface of the liquid in a narrow tube due to surface tension, or a dent if the liquid wets the tube wall. The scale is read by eye to the nearest 1/10 of the smallest scale.
Turn the stopper to start dripping. Hold the buret with one hand and pull it toward the main body of the buret to prevent the stopper from falling out.
When titration is completed, read the scale to determine the volume to be titrated.