What Is a Capillaroscope?
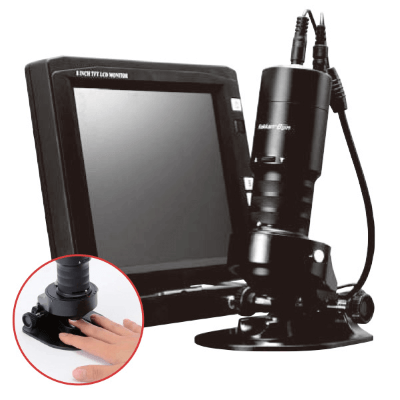
A capillaroscope is a microscope that can easily observe the condition of capillaries in the fingertips and skin, as well as red blood cells, white blood cells, and platelets flowing in capillaries, by applying oil to the fingertips, illuminating them with a high-intensity light source, and magnifying them under the skin, without drawing blood.
In the Lifelong Education Series 6 “Microcirculation” published in 1979, under the general supervision of Taro Takemi, Shigeo Okinaka, and Yuichi Yamamura, Makishige Asano provided a biological window into the observation of microcirculation in the skin. In the article, Makishige Asano, under the supervision of Taro Takemi, Shigeo Okinaka, and Yuichi Yamamura, emphasized the observation of capillary vessels in the nail bed and labial skin as one monitor of microcirculation in the skin. However, at that time, observation took the form of looking through a microscope and recording using reproductions and photographs. With the advancement of science and technology, these studies opened up new possibilities in the 21st century, where they could be checked on a monitor and recorded as moving images, and were called capillary blood flow observation devices.
Around 2010, capillary observation devices began to be miniaturized, and the Osaka University Graduate School of Medicine, in collaboration with Atto, succeeded in extracting capillary images using the reaction-diffusion equation, making it possible to quantify capillaries. The scope is used in a wide range of applications in the medical industry.
Capillaroscopes are used not only for research in the medical industry, but are also widely used in the health and beauty industries to observe capillaries and measure the effects of treatments.
Uses of Capillaroscope
The following is a description of the uses of capillaroscope.
Capillaroscopes are widely used in the medical industry, for example, as a clinical test and demonstration device at universities and research institutes, or as a device for verifying the effectiveness of treatment at hospitals by observing capillary shape and blood flow in the peripheral and subcutaneous tissues. In the past, the device was used for observation and capillary imaging. Previously, observation and capillary images were stored and quantified visually or using a simple drawing system, but the aforementioned non-personal quantification method of Osaka University has enabled mass analysis, and in October 2020, Maekawa et al. (Department of Ophthalmology, Tohoku University School of Medicine) presented a paper at the Japanese Society for Glaucoma Research on the usefulness of nail bed capillary measurement for glaucoma diagnosis at the Japan Glaucoma Society. The usefulness of capillary measurement in glaucoma diagnosis was presented by Maekawa et al. (Department of Ophthalmology, Tohoku University School of Medicine) at the Japan Glaucoma Society in October 2020, and the Capillary Laboratory Social Implementation Consortium was established by the NPO Kinki Bioindustry Promotion Council with Professor Takakura of the Department of Information Transfer, Research Institute for Microbial Diseases, Osaka University as the committee chair.
It is also used to observe changes in blood circulation promotion in Chinese medicine and massage, and in counseling for behavioral change to improve lifestyle at pharmacies.
In addition to the medical industry, it is also used in the beauty and health industries to observe capillaries and blood flow improvement after treatment.
Principle of Capillaroscopes
The capillaroscope projects a high-intensity light source onto the epidermis and dermis to magnify the capillaries on the body surface and project the capillaries on a camera to observe the red blood cells, white blood cells, and platelets flowing in the capillaries without the need to draw blood.
Capillaroscopes are often composed of a high-power lens and a camera, and can be connected to a suitable monitor for projection or combined with analysis software for quantification, thereby expanding their range of applications.
Results of Introducing a Capillaroscope
The greatest advantage of the capillaroscope is that it allows observation of capillaries and blood flow in real-time without drawing blood from the examinee. It is a very useful examination device because it allows us to confirm the capillary shape and changes in blood flow.
The reason the condition of capillaries can be easily identified is that the point of observation is specialized to observe capillaries in the “under the cuticle of the nail” because capillaries between the skin and the nail run in a hairpin shape. It is very easy to operate and does not require specialized knowledge or difficult operating techniques. Furthermore, the simple UI allows anyone to operate and easily observe.
The ability to easily identify minute changes in oneself based on capillary shape and blood flow is also beneficial to the examinee. All the examinee has to do is apply oil to the fingertips, without enduring pain or long waiting periods. The examinee simply applies oil to his or her fingertips, and that is all there is to it. The fact that there is almost no burden on the examinee is another reason for its popularity. Furthermore, since the capillary shape and blood flow can be checked in real-time, it has the potential to provide a strong argument for measures to improve lifestyle-related diseases and other illnesses in the future.
As described above, the capillaroscope is a testing device that benefits both the user and the examinee when introduced. Even today, its popularity is increasing. It is expected that capillaroscopes will be used in a wider range of fields and many more situations in the future.
Price of a Capillaroscope
The price of a capillaroscope ranges from 200,000 yen to 500,000 yen. Recently, however, low-priced capillaroscopes that are not dedicated to capillaries but are used to observe printed matter, electronic components, and skin, have been developed that use inexpensive lenses and sensors and have simple functionality. Some low-priced products are now available.
Capillaroscopes that use lenses and sensors with high performance include tabletop and handheld capillaroscopes with manual focus adjustment. It costs about 400,000 yen due to its high degree of freedom and manually adjustable functionality.
There are cheaper scopes that are handheld types and have a function that allows autofocusing with half the probability of focus adjustment as a diversion of those made to look at the quality of printed materials and electronic components. Here, although manual adjustment is almost impossible, the LCD monitor can be projected on a smartphone or computer, and can be purchased for about 180,000 yen.
Capillaroscopes range in price. However, some offer low prices while maintaining high functionality, and can be purchased according to the functionality required. Capillaroscopes can also be introduced through the rental method.