What Is an Ozone Sterilizer?
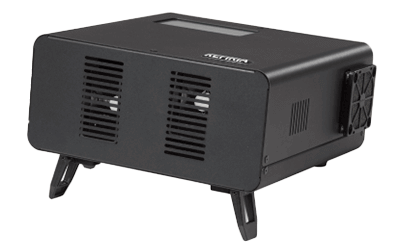
An ozone sterilizer is a device for efficiently sterilizing spaces and materials using the powerful oxidizing action of ozone (O3).
Unlike ordinary disinfectants, ozone disinfection does not produce resistant bacteria. It is also relatively safe because ozone gas is converted to safe oxygen gas (O2) after an oxidation reaction. Another feature of ozone sterilization is that it can be performed at room temperature without heating, making it possible to sterilize non-heat-resistant materials.
Studies have shown that ozone sterilization is effective against a variety of bacteria, including Escherichia coli, Staphylococcus aureus, and Pseudomonas aeruginosa.
Uses of Ozone Sterilizers
Ozone sterilizers are mainly used for sterilization and disinfection. Specifically, ozone gas is generated inside the device and diffused into the air to inactivate airborne viruses and bacteria. The places where viruses and bacteria should be reduced are facilities that are used by large numbers of people.
In such facilities, inactivation of viruses and bacteria is important from a public health perspective. For example, ozone sterilizers are used in hospitals, nursing homes, schools, daycare centers, hotels, food factories, and restaurants.
Ozone sterilizers are also used to decompose odorous substances. In other words, they are used for deodorization. Specifically, ozone sterilizers are used in clean centers to control the odor of garbage, and in pet-owning households to control odors. By suppressing odors, working and living environments can be improved.
In addition, ozone sterilizers can also be used to repel pests. Although it cannot directly exterminate pests such as cockroaches, it can decompose pheromones and other substances necessary for pests to reproduce, thereby keeping them at bay.
Principle of Ozone Sterilizers
The principle of ozone sterilizer is the decomposition of substances by the oxidizing power of ozone gas, as described above. The ozone molecule is a simple molecule (O3) consisting of three oxygen atoms, and is known to have the second highest oxidizing power after fluorine.
An ozone sterilizer decomposes organic substances by oxidizing them with ozone gas generated inside. The oxidative decomposition action not only inactivates microorganisms such as bacteria and viruses, but also decomposes odorous substances.
Features of Ozone Sterilizers
Sterilization methods have long been known for their ability to produce sterilizing and inactivating effects on microorganisms. Conventional sterilization methods include ethylene oxide gas, gamma rays, and ultraviolet irradiation.
However, the disinfection method using ultraviolet and other types of irradiation has the disadvantage that it cannot sterilize areas where ultraviolet rays cannot reach. In addition, the sterilization method using ethylene oxide gas may cause residues that are harmful to the human body.
In contrast, in the case of the ozone gas sterilization method, ozone gas is a gas, so it can be pumped into even the most complicated structures. In addition, ozone gas itself decomposes when it oxidizes microorganisms, and immediately turns into oxygen gas after decomposition. Therefore, ozone sterilizers can be effective even in areas that are difficult to sterilize and have little effect on the human body if used properly.
Other Information on Ozone Sterilizers
1. Maintenance Cost of Ozone Sterilizers
Ozone sterilizers use ultraviolet lamps and plasma to generate ozone gas. Ultraviolet light and plasma irradiation can generate highly concentrated ozone from oxygen in the air. Since the raw material is oxygen gas, which is originally present in the air, and only the electric power necessary for irradiation is required, no complicated processes are needed for ozone gas generation.
Therefore, another feature of an ozone sterilizer is its low running cost. Ozone sterilizers have relatively high safety for human health and low risk of air pollution, and are becoming popular as a powerful sterilization device in this age of emphasis on SDGs.
2. Effects of Ozone Gas on the Human Body
Ozone gas is relatively safe for the human body at low concentrations because it quickly converts to oxygen gas as described above. However, because of its oxidizing power, it is harmful in high concentrations.
As a guideline for safe ozone gas concentration, 0.05 ppm or less is recommended. Because ozone gas itself has a characteristic odor, the presence of ozone gas can be detected even at very low concentrations.