What Is a Ball Valve?
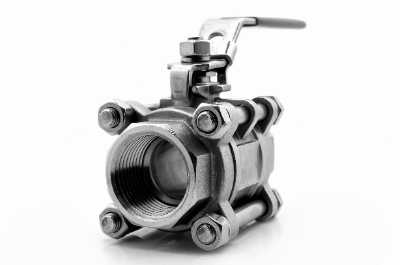
A ball valve is a valve with a spherical (ball-shaped) valve plug with a hole drilled in the center, which is inserted into a seat in the body (valve box).
By rotating the ball of the valve body 90 degrees, the fluid flow is shut off and the flow path is closed. Ball valve is defined in the Glossary of Terms for valves (JIS B0100) as “a general term for a valve in which a spherical valve plug rotates inside a valve housing with a valve rod as its axis. The valve plug can be a full-surface or half-surface sphere. The valve plug can be either a full-surface ball or a half-surface ball.
The ball of the valve plug does not remain in the flow path when the valve is open, resulting in a small pressure drop, and is used for fully open or fully closed valves, not for flow control.
Uses of Ball Valves
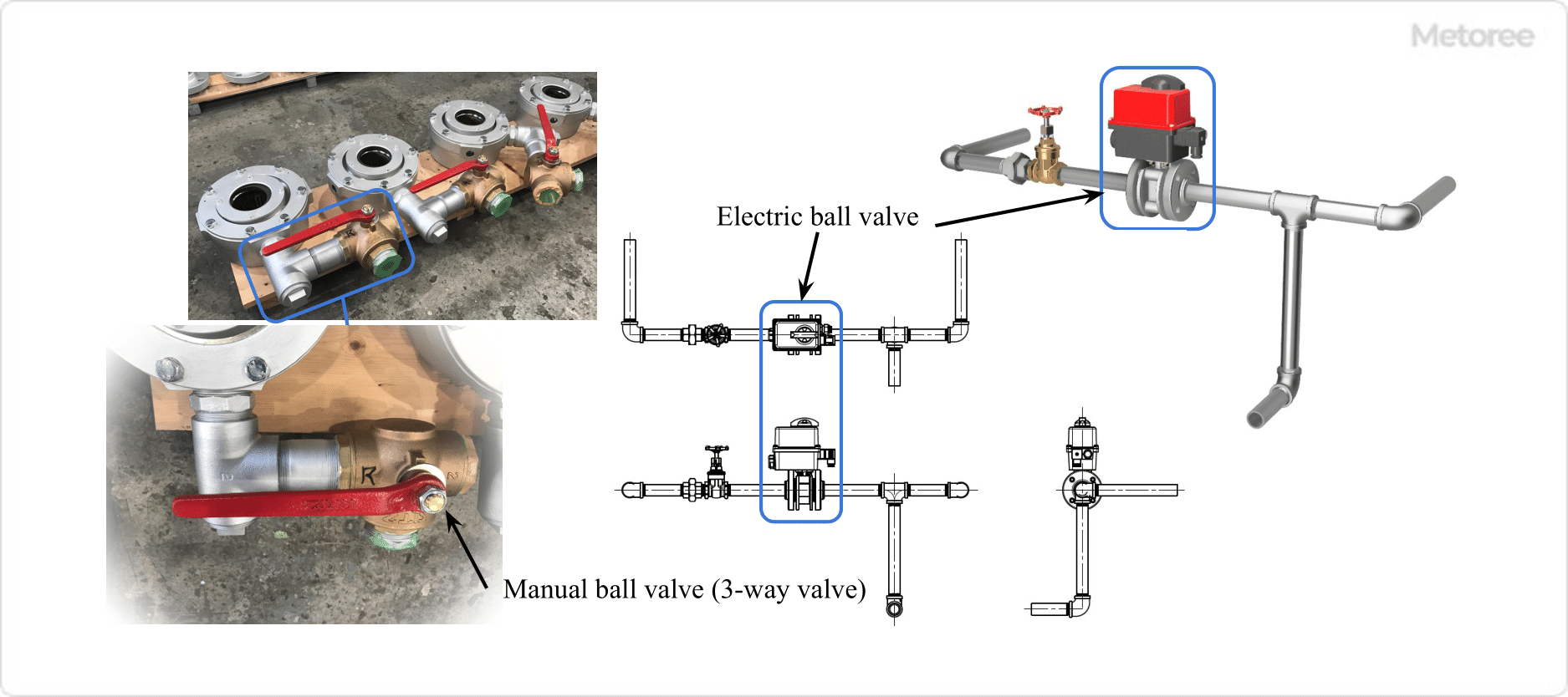
Figure 1. Example of Ball Valve Use
Ball valves are widely used in household and general industrial applications because of their ease of operation, simple structure, and compact size. Ball valves are generally used in the fully open or fully closed position because fluid accumulates between the body (valve plug) and the ball (plug) when used at the ball’s mid-position opening angle. Therefore, this valve is used as a shutoff valve for shutoff purposes.
The ball (plug) of a ball valve can be opened or closed by turning the handle attached to the stem (valve stem) 90 degrees, which has the advantage of easy operation and short operating time. In addition, since the ball does not remain in the flow path during valve opening, pressure loss is reduced.
The flow path has a few steps and can be used for piping fluids containing slurries and solids. The slurry is a mixture of solids and liquids, such as finely ground coal or ore, mixed with water to form mud, which is used for conveying.
Principle of Ball Valves
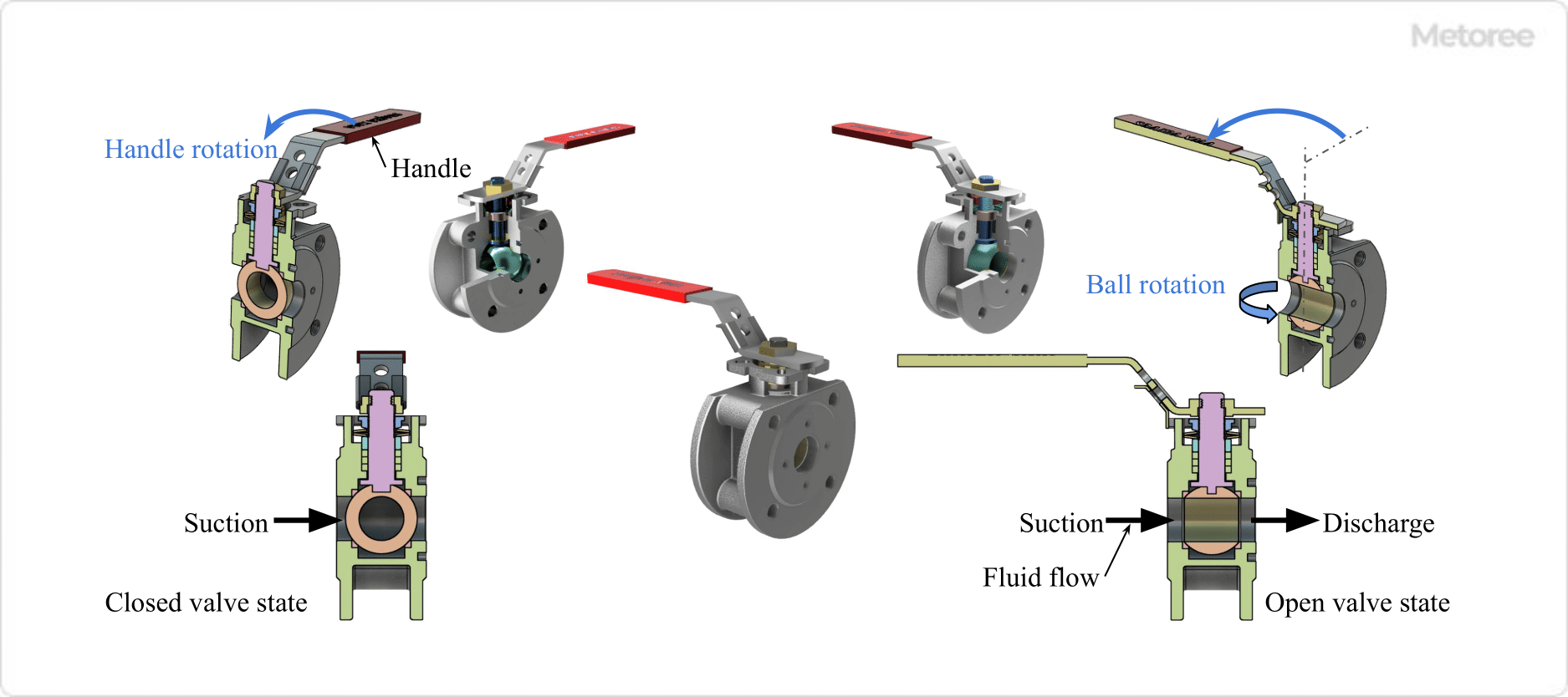
Figure 2. Ball Valve Opening and Closing Valve Status and Fluid Flow
In a ball valve, the ball (valve plug) and seat (valve seat) inside the body (valve box) make surface contact to close the fluid. In this condition, the center of the ball bore is at 90 degrees to the center of the body opening. When the ball is rotated 90 degrees, the center of the ball hole becomes concentric with the center of the body opening, and the fluid flows.
The force required for this open/close operation is proportional to the frictional resistance between the ball’s spherical surface and the seat. The larger the nominal diameter of the valve, the greater the force required to open and close the valve. Therefore, valves with larger nominal diameters use rotating handles equipped with gear actuators (reduction gears).
Many ball valves are full-bore port valves with a small difference in flow path area between the inside of the body and the inlet/outlet piping, and feature an extremely small pressure loss when fully open because the flow path is almost straight.
Structure of Ball Valves
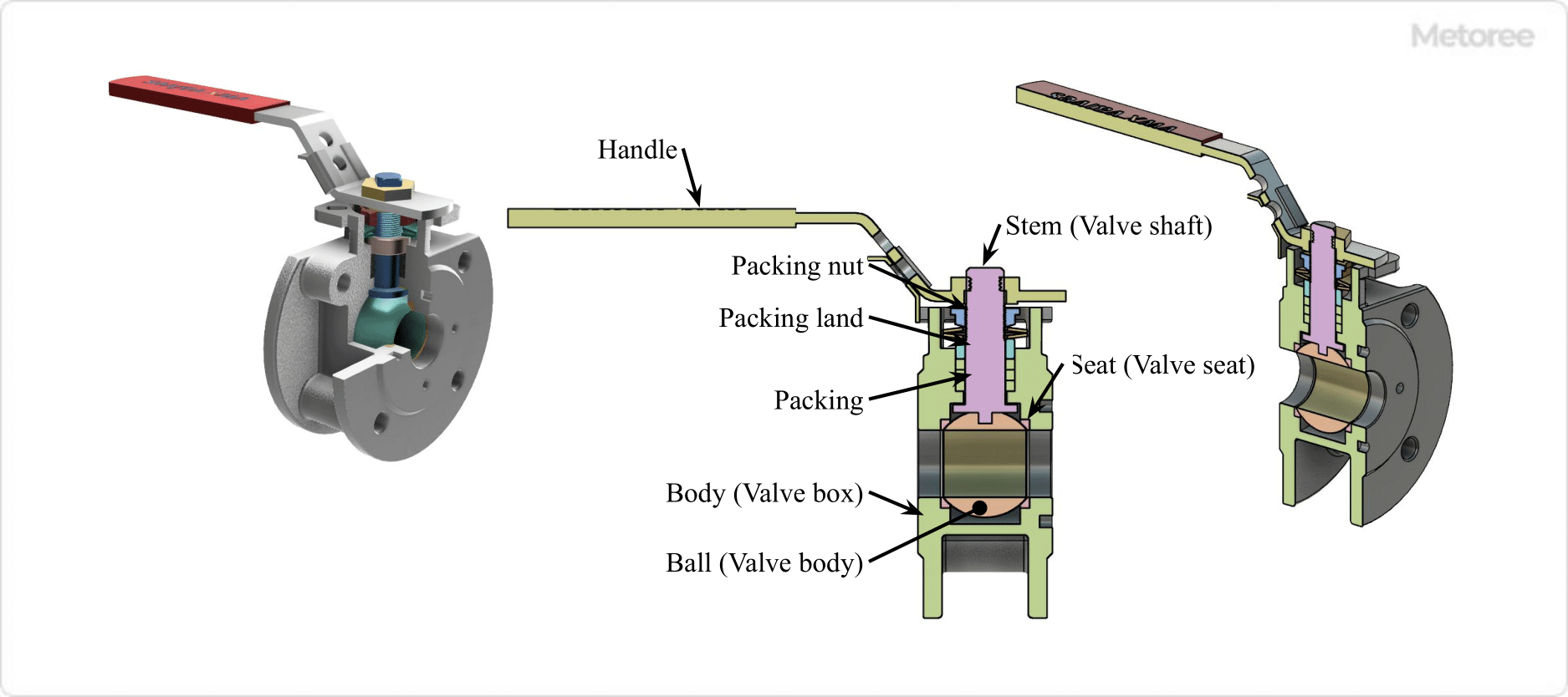
Figure 3. Structure of Ball Valve
Ball valves are mainly composed of a body (valve box), a disc (valve plug), a stem (valve stem), and a handle. A ball valve is operated by a handle or an actuator.
The handle is attached to the stem and transmits rotation to the stem. When the valve is open, the rotation of the handle causes the ball to rotate 90 degrees, and when the valve is closed, the ball rotates in the opposite direction.
Types of Ball Valves
1. Classification by Opening/Closing Operation Method
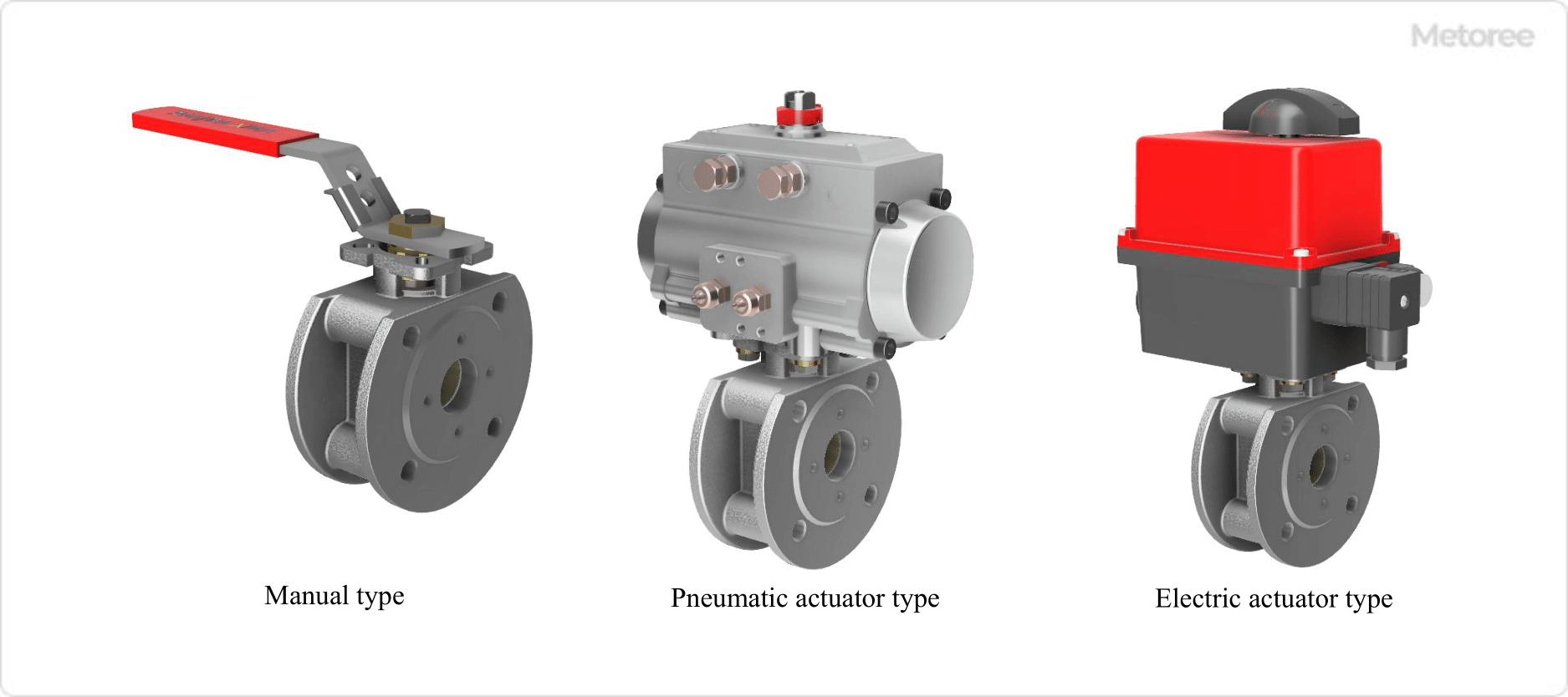
Figure 4. Operation and Drive System of Ball Valve
Ball valves have the following three main types of operation and drive methods for opening and closing.
- Manual Type
Rotation of stem by the handle, etc.
- Air-Actuated Type
Rotates the stem with a pneumatic actuator
- Electric Type
Rotate stem with electric actuator
2. Classification by Bore Shape
Ball valves are available in the following three bore shapes. The bore is the inside diameter of the flow path in the body.
- Standard Bore
The bore diameter is one size smaller than the valve’s nominal diameter (pipe inner diameter).
- Reduced Bore
The bore diameter is at least one size smaller than the valve’s nominal diameter (pipe bore).
- Full Bore
The bore diameter is almost the same as the nominal diameter of the valve (pipe I.D.)
3. Classification by Ball Support Method
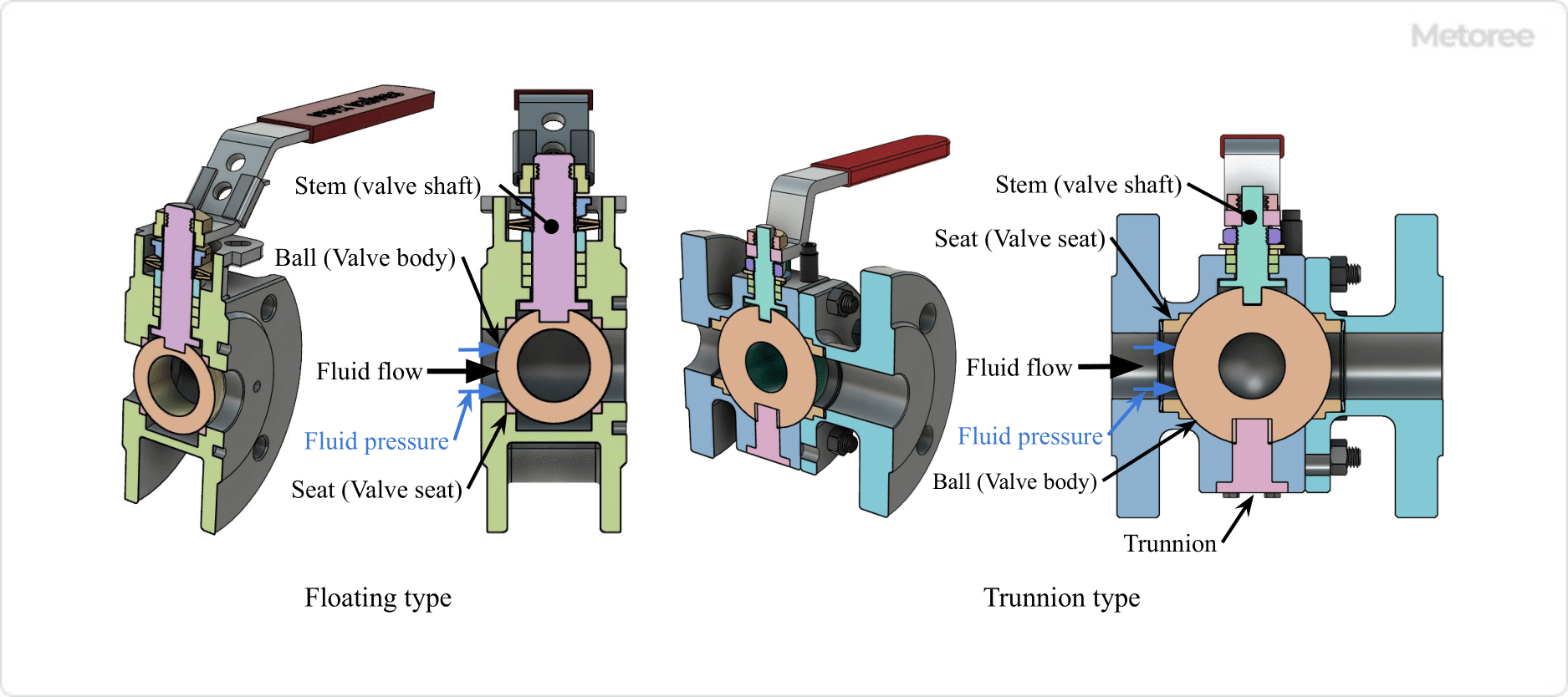
Figure 5. Ball Support Method
Ball valves are available in the following two types of rotating ball support methods.
Floating Type (Floating Ball Type)
In the floating type, the ball is supported by a seat mounted inside the body. The square end of the stem fits into the ball groove and rotates the ball.
The groove of the ball is parallel to the fluid flow direction when fully closed, and the ball slides slightly and is pressed against the seal by the fluid pressure to ensure sealing. Typically used for low pressure (up to JIS20K, CL300) and small bore (up to DN200).
Trunnion Type (Fixed Ball Type)
In the trunnion type, the upper part of the ball is supported by the stem (valve stem) and the lower part by the trunnion (rotating shaft). The upper and lower parts of the ball are supported by the rotating shaft, making it less susceptible to fluid pressure. The seat is pushed by a spring built into the seat holder, which contacts and seals the ball. It is generally used for high pressure (JIS 30K, CL600 or higher) and large bore (DN250 or higher).
4. Classification by Body Material
- Grey cast iron JIS G5501 FC200
- Spheroidal graphite cast iron JIS G5502 FCD400
- Carbon steel forgings for pressure vessels JIS G3202 SFVC 2A
- High temperature and high pressure cast steel JIS G5151 SCPH2, SCPH21
- Stainless steel castings JIS G5121 SCS13A, SCS14A
- Copper and copper alloy castings JIS H5120 CAC401 Bronze castings Class 1
- Copper and copper alloy rods JIS H3250 C3771 Brass for forging
Body materials are selected based on the following requirements. For details, refer to each manufacturer’s catalog, etc.
- Fluid type, pressure, temperature, flow velocity, and presence/absence of impurities
- Corrosion resistance required or not
- Applicable regulations and standards
5. Classification by Sheet Material
In general, ball valve seats are either soft seals made of resin or carbon fiber, or metal seats made of metal.
Soft Seals
PTFE (Teflon) or PTFE filled with carbon or other agents. Maximum service temperatures are approximately 150°C for PTFE alone and 300°C for PTFE filled with carbon or other agents.
PTFE sheets are characterized by chemical resistance, low frictional resistance, and excellent operability. There are also carbon fiber sheets with a maximum operating temperature of approximately 500°C.
Metal Sheet
Carbon steel or stainless steel material is thermal-sprayed with a high-hardness nickel alloy on the ball contact surface of the sheet. In this case, the same thermal spray is also applied to the ball side.
The metal sheet has a maximum operating temperature of up to about 500°C and applies to high-temperature fluids, powders, slurries, and viscous fluids that are difficult to handle with soft sheets.