What Is a Welding Robot?
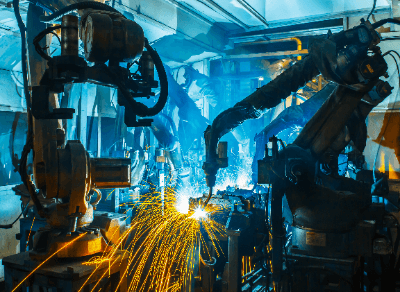
A welding robot is an industrial robot that can perform welding processes automatically. They are mainly used in factories that manufacture automobiles, airplanes, etc.
Welding robots can save labor and improve productivity. They can repeat the same operation quickly and accurately, increasing work efficiency through short and stable operations. Additionally, they can reduce the risk of occupational accidents, such as burns from welding processes and health hazards due to inhaling toxic gases during welding, as well as errors caused by human factors.
In the welding process, achieving consistent weld appearance and density is challenging when done manually, as the quality of welding processes significantly depends on the skills of individual workers. While welding robots are industrial products and may have minimal play in their operating axes, individual differences between robots are controlled meticulously, ensuring exceptional work reproducibility.
Welding robots can minimize quality variations without relying on operators’ skills, consistently producing uniform products, thus enhancing quality reliability.
Uses of Welding Robots
Welding robots automate and optimize welding processes, reducing the need for human intervention and enhancing efficiency. They can be programmed to execute a series of work procedures and processes, reducing labor costs and preventing a decrease in work efficiency due to a lack of manpower.
Furthermore, in manual welding processes, workers are exposed to high-temperature areas where metal melts, increasing the risk of burns from welding spatter, eye damage from intense light, and health hazards from harmful gases. Welding robots contribute to improving the safety of the work environment.
Principles of Welding Robots
Welding robots have an arm structure resembling a human hand with multiple joints for smooth movement. The most common type is the 6-axis robot, but robots with fewer joints can handle heavier objects with a more limited range of motion, while those with more joints can perform more intricate movements.
Attached to the end of the robot’s arm is a welding torch, and by changing the torch part, various welding processes can be performed. Additionally, by replacing the welding torch with a fixture for holding parts, the robot can function as a transfer/handling robot, enabling automation of tasks beyond welding.
Other Information on Welding Robots
- Teaching Welding Robots
Teaching involves instructing welding robots on welding operations and procedures, programming them for automatic operation. Robots can only perform tasks defined in the program. Teaching is crucial because the accuracy of welding processes depends on factors beyond the welding robot, such as workpiece alignment during part setup and the surface quality of the welding surface.
Teaching programming typically uses a microcontroller called a PLC (programmable logic controller) or a sequencer. The most common programming language is the “ladder diagram,” which uses an intuitive “ladder-like” graphical representation. There are two primary teaching methods:
Offline Teaching
Offline teaching involves using 3D data on a computer to obtain coordinates for welding process points, simulating them, and transferring the data to the welding robot. Alternatively, welding motion can be programmed directly into the robot. Depending on the accuracy of the product or fixture, strict adherence to 3D data may not always be possible. Combining online teaching, as described in the next section, can improve teaching accuracy.
Online Teaching
In online teaching, a teaching operator uses a remote control to move the welding robot directly, performing a sequence of welding operations. The robot memorizes these actions and reproduces them precisely. However, this teaching method has the drawback that the robot cannot be used for production during the teaching process. It is time-consuming because the operator must set up each welding operation by moving the robot. Consequently, offline teaching has become more common in recent years. Nevertheless, fine adjustments may still be necessary based on the product’s machining accuracy or fixture, so it’s essential to switch teaching methods flexibly as needed.
- Qualifications for Teaching Welding Robots
Teaching welding robots requires special training, as mandated by Article 59 of the Occupational Safety and Health Law. Violations can result in penalties for both the operator and the company. Operators can qualify for the job with just two days of specialized training and must acquire the skills and knowledge to perform teaching immediately.
Teaching involves programming and simulation using 3D data, as well as knowledge of welding operations. In many cases, optimizing the welding process order and adjusting the welding robot’s posture can significantly enhance welding process efficiency. The skill of the operator conducting the teaching is crucial, so training from an experienced person within or outside the company is essential.
- Control of Welding Robots by Sensors
For large parts, processing and assembly errors in preceding processes often lead to misalignment in the welding area. In recent years, sensor technology has gained attention for its ability to automatically compensate for welding robot misalignment by attaching sensors to the robot. Sensing technologies include wire touch sensors and laser displacement sensors for pre-sensing before welding and arc sensors and visual sensors for real-time sensing during welding.
Sensing technology continues to advance, allowing welding robots to automatically compensate for misalignment. This eliminates the need for detailed manual teaching corrections, ensuring more stable product quality.