What Is a Memory IC?
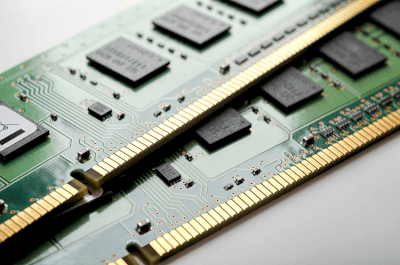
A memory IC is a semiconductor device that is responsible for recording data in a processor-based system.
Memory ICs can be broadly classified into ROM and RAM. ROM (read only memory) is memory that is limited to reading data written at the time of manufacture. However, ROM also includes devices such as EEPROM and flash memory, which allow data to be rewritten.
RAM (random access memory) is a memory that can write/read data at a high speed. RAM is limited to temporary data storage applications because the recorded data disappears when the power supply that drives the memory device is turned off.
There are two types of memory structures: SRAM (Static Random Access Memory) and DRAM (Dynamic Random Access Memory), which allows a higher level of integration.
Uses of Memory ICs
Memory ICs are used in combination with processors to store program data and retain data during arithmetic operations. Memory ICs are installed in all processor-equipped devices and computers, from cell phones, tablet terminals, and personal computers to mainframes.
Generally, ROM stores program data, and the processor performs various processes according to that program data. At that time, data and information to be temporarily stored are written in RAM. Since RAM data is frequently rewritten, it is important for RAM to operate at high speed.
EEPROM, which is classified as a part of ROM, is also used to write adjustment data and other data, especially in electronic devices. Flash memory is used as a storage element in memory cards and SSDs (Solid State Drives), taking advantage of its characteristics as a ROM that can achieve a large memory capacity and can be rewritten.
Principle of Memory ICs
Memory ICs are equipped with a recording area in which many memory elements are arranged in an orderly fashion, address lines for specifying the data of individual memory elements, signal output lines for communicating the data of the memory elements to the outside world, and signal input lines for inputting data from the outside.
The processor used in combination with the Memory IC is also responsible for managing the data recording area of the Memory IC, so that when necessary data is read out, the data of that memory element is output to the signal output line by manipulating the address line. For data to be recorded in the memory, the address line is manipulated to specify the recording element, and the data is transferred to the signal input line.
The above is the flow of reading and writing signals to Memory IC. However, the internal circuit configuration and driving method of Memory ICs are completely different depending on the type.
Types of Memory ICs
Memory ICs can be broadly classified into ROM and RAM, each of which has several types.
1. ROM
Mask ROM
In mask ROM, a dedicated mask is fabricated according to the data to be written, and the data is written using this mask in the device manufacturing process. Therefore, the written data cannot be changed.
PROM (Programmable Read Only Memory)
A PROM is a write/erasable ROM that retains its memory contents even when the power is turned off.
EPROMs consist of an array of MOSFETs with floating gates, and data is written to them using a dedicated writing tool. However, these devices are rarely used today because they require ultraviolet irradiation when erasing data.
EEPROM (Electrically Erasable PROM) and flash memory are used instead. Both can be written or erased by receiving a control signal from a controller, but flash memory has become widely used in memory cards and other devices because of its structure that can achieve particularly large storage capacity.
The data is set to 0 or 1 depending on the presence or absence of a charge injected into the floating gate of the MOSFET. Since the injection and erasure of the charge is done using the tunneling effect, a high-voltage power supply circuit is built into the IC.
2. RAM
SRAM
SRAM uses a flip-flop circuit or similar device as the storage element, and once recorded, the contents are retained as long as power is supplied. Because it does not require a refresh operation like DRAM (see below), it consumes less power than a DRAM of the same memory capacity and can be read/written at high speeds.
However, the complex structure of the memory elements makes it difficult to achieve high density, and the unit manufacturing cost is high. Therefore, DRAM is suitable for applications where power saving and high speed are important. For example, it is often used as high-speed cache memory in computers, where it is placed between the processor and the main memory.
DRAM
DRAM uses one transistor and one capacitor to store data. In other words, the state of the capacitor with/without charge is defined as data 0/1. The transistor acts as a switch to accumulate charge in the capacitor.
The circuit configuration is simple, which allows for a high level of integration. However, because charge gradually leaks from the capacitor even when the switch is in the OFF state, data overwriting is periodically performed to prevent data corruption due to charge leakage. This is called a refresh operation, and is a function unique to DRAM.