What Is a Steamroller?
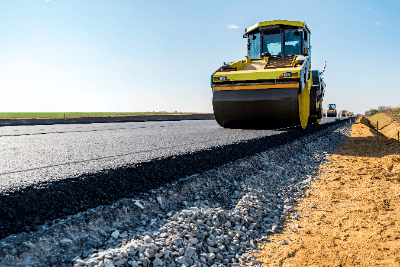
A steamroller is a machine used in pavement construction.
Steamrollers are used in different ways, depending on the structure of the pavement and the construction process. The basic structure consists of four layers, starting from the one closest to the ground: “roadbed,” “base layer,” and “surface layer.” The structure also varies depending on the pavement specifications, including the most familiar asphalt pavement, concrete pavement, and special pavement.
The construction procedure for each layer is determined, and the appropriate steamroller for the job is used.
Uses of Steamrollers
The steamroller used in the paving process varies along with the pavement specifications. Each layer created by the steamroller has its own role. The first roadbed transfers the load of the upper three layers to the ground and is made mainly of soil.
The roadbed is responsible for distributing the loads of the top two layers, and there are two layers of crushed stone containing cement, lime, etc., the top layer and the bottom layer. The base layer is responsible for correcting the unevenness of the roadbed and is a layer of asphalt, sand, etc.
The last surface layer is asphalt or concrete, which distributes the load of vehicles passing over it. Steamrollers are used to ensure that each layer performs its role properly.
Principles of Steamrollers
The following are the principles and methods of steamroller used for each paving process.
1. Roadbed Construction
Roadbed is to flatten and consolidate the ground. This prevents the roadbed from settling due to the weight of vehicles and other objects passing over it. A bulldozer is an earth-moving machine that excavates, fills, and levels the ground, using its front blades to push and remove earth and sand.
Motor graders are used to level the ground by tilting the blade installed under the body against the direction of travel. Tire rollers and road rollers are used to compact the soil by rolling it under their own weight. In addition to the dead-weight type, vibratory road rollers are also available.
In roadbed construction, a bulldozer is used first to level the roadbed, and a motor grader is used for the final leveling. Next, tire rollers are used for compaction, and finally, road rollers are used for hardening.
2. Roadbed Construction
The roadbed work uses the same earth-moving equipment as for roadbed construction. In roadbed construction, crushed stone materials are first unloaded from dump trucks.
Next, a bulldozer is used for rough leveling, and a motor grader is used to spread the material to the specified finished thickness. Then, tire rollers and road rollers are used for compaction and spreading to the specified density.
3. Base Layer and Surface Layer Construction
The asphalt finisher is a self-propelled steamroller. As a specialized steamroller for asphalt paving, it is used for both base layer and surface layer work. It consists of a hopper for storing asphalt mixture, a prime mover, a tractor section for traveling equipment, and a screed for spreading the asphalt mixture evenly.
First, the asphalt mixture transported by dump trucks is stored in the hopper. Next, the mixture is fed backward by a bar feeder at the bottom of the hopper, spread to the left and right by a screw, and spread evenly by a screed. The angle of the screed can be varied to increase or decrease the amount of asphalt and to change the thickness of the spread.
Surface work using asphalt finishers involves two processes: leveling and compaction. Spreading is the process of spreading the asphalt mixture. Compaction is the process of repeatedly compacting the spread to create a firm base.
Finally, it is finished by rolling with tire rollers or road rollers.
Other Information on Steamroller
Concrete Steamroller
For roadbed and roadbed construction, the Steamroller required for concrete paving is the same as for asphalt paving. An asphalt intermediate layer is placed on top of the roadbed, and a concrete slab is formed on top of the asphalt.
To form the concrete slab, concrete is generally transported by mixer trucks and poured by concrete pump trucks. In addition to ordinary concrete pavement, there are other methods to overcome the disadvantages of concrete pavement, such as continuous reinforced concrete pavement and compacted concrete pavement.
In recent years, asphalt pavement has become the majority and the percentage of concrete pavement has declined. Concrete pavement has advantages and disadvantages compared to asphalt coating, and its adoption is for special locations.
Concrete pavement is used in tunnels, steep roads, airport aprons, container yards, etc. because of its superior durability and service life.