What Is a Fixed Resistor?
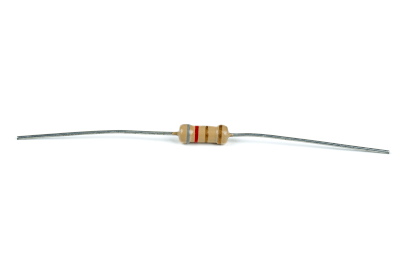
A fixed resistor is an electrical resistor whose resistance is fixed and cannot be varied.
A resistor refers to a circuit element that controls the current value. If the circuit resistance were 0Ω, the circuit would be short-circuited and a large current would flow. To prevent this, a resistor is inserted to control the appropriate current.
Resistors include variable resistors, whose resistance value can be freely changed, and semi-fixed resistor, whose resistance value can be adjusted.
Usage of Fixed Resistors
Fixed resistors are basic circuit elements used in all kinds of electronic circuits and have a variety of applications. Specific uses are as follows:
- Current limiting in electronic circuits
- Voltage divider
- Detecting current values
- Pull-up and pull-down resistors that set the voltage of digital signals
- Active filter circuits combined with capacitors and operational amplifiers
- Circuit protection in the event of lightning surges and other inrush currents
Principle of Fixed Resistors
When a current passes through a resistor, electrons repeatedly collide with atoms in the resistive element. With each collision, the speed of electron movement decreases, resulting in a decrease in the number of electrons passing through in a given time. Since the number of electrons passing through per unit of time is the current value, it can be said that the collision with the resistive element is the essence of resistance.
Also, when electrons collide with atoms, part of the energy of the electrons is converted into heat, which is Joule heat. Ohm’s law: “voltage = current × resistance” holds true between the current flowing through fixed resistors, the applied voltage, and the resistance value. Based on this, when designing a circuit, select fixed resistors with an appropriate resistance value based on the applied voltage and current value.
When a current flows through fixed resistors, a potential difference is generated at both ends of the resistor, and the power calculated by the current value x potential difference is consumed as Joule heat. If this power consumption is excessive, the resistor may burn out, so care should be taken.
The specifications of fixed resistors specify the rated power, which is “the maximum value of power that can be consumed continuously.” Fixed resistors are used at 50% or less of the rated power, and components should be selected based on this.
Types of Fixed Resistors
Fixed resistors can be classified into the following three types in terms of structure.
1. Leaded Type
The leaded type has lead wires connected to the electrodes at both ends of the fixed resistors and designed to be soldered by passing the lead wires through holes in a printed circuit board. Resistors can be further classified into the following types according to the material of the resistive element.
Carbon Film Resistors
Resistors with carbon adhered to the surface of porcelain or other materials as a resistive element, also called carbon resistors. The surface of the porcelain has spiral grooves, and the resistance value is set by changing the width and length of these grooves.
Because they are inexpensive, they are widely used in general circuits, but they have a large resistance error, with the usual product having an accuracy of about 5% of the nominal resistance value. They are also inferior to metallic resistors in terms of noise generation.
Metal Film Resistors
A resistor with a metal resistive element formed on the surface of porcelain. There are two types: a thick-film type, in which a resistive element paste is fired, and a thin-film type, in which the resistive element is vapor-deposited. Thick-film type has a small error margin of about 1%, and thin-film type has a higher accuracy of 0.05%.
They are used in measuring instruments, audio products, etc., where accurate resistance values are required.
Metal Oxide Film Resistors
These resistors are made of metal oxide, such as tin oxide formed on the surface of porcelain as a resistive element. They are mainly used in medium power circuits such as power supplies because of their excellent heat resistance and ability to handle relatively high power.
Metal Glaze Film Resistors
This type of resistor uses a mixture of metal, metal oxide, and glass as the resistive element, and its thick film structure provides stable characteristics and resistance to environmental changes. They also have excellent corrosion resistance. This resistive element is used not only in leaded type but also in chip resistors.
2. Surface Mounting Type
The surface-mount type, which does not come with lead wires, is intended for surface mounting. Since this method of mounting components on the surface of the board can reduce the board space, it was actively used in electronic devices that require miniaturization at first, but now surface-mount type components have become the mainstream.
From the structural aspect, surface mount type resistors can be classified into two types: rectangular chip resistors and cylindrical chip resistors.
Rectangular chip resistors
Resistors use metal glaze as a resistive element.
Cylindrical chip
Originally, it was a leaded resistor with the lead wire removed, but now it is a resistor with a carbon film or metal film resistive element.
Cylindrical type was first popularized as surface mount type resistors, but square chip resistors are now widely used due to their ease of use in the soldering process.
3. Wire-Wound Resistors
A wire-wound resistor is a resistive element made of metal wire wound in a spiral shape. The structure of winding a uniform metal wire with a fixed length allows for highly accurate resistance value setting and a large power capacity. Moreover, by appropriately selecting the resistive element, the change in resistance value due to temperature change can be suppressed.
However, because of its winding structure, it exhibits coil inductance characteristics with respect to AC current, and the higher the frequency, the greater the impedance, which results in a smaller current. This characteristic has an adverse effect in the high-frequency range, so non-inductive winding may be used to prevent this.
Metal Clad Resistors
This term refers to metal-clad resistors. It is a wire-wound resistor with a metal cladding. Since they are intended to be used in high power circuits, some are equipped with a heat sink or heat dissipation fins to prevent heat generation.
Enameled resistors
A metal wire that serves as a resistive element is wound around a core made of porcelain or other material, and an enamel exterior is attached to protect it. Because of its heat-resistant structure, this type of resistor is used in applications where heat generation is inevitable.
Incidentally, enamel is a glassy glaze baked at high temperature on the surface of metallic materials such as iron, aluminum, and stainless steel.
Cement resistors
A wire-wound resistor is housed in a porcelain case and covered with cement. A similar structure is sometimes used for oxide film resistors. Since they are strongly protected by cement, they are very strong against heat and vibration. It is used for high power circuits.