What Is a Corrosion Inhibitor?
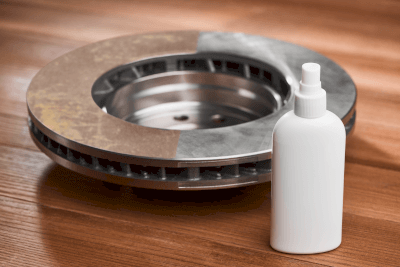
A corrosion inhibitor is used to prevent rust on metal products and metal parts.
Generally used on steel, the corrosion inhibitor is applied in liquid form directly to the object to protect the metal surface.
There are several types of corrosion inhibitors, depending on the product and application.
Uses of Corrosion Inhibitors
1. Liquid Corrosion Inhibitors (Water-Soluble or Oil-Soluble)
Liquid corrosion inhibitors are used when applied directly to the target metal or added to a solution. Typical examples of its use include application to the surface of steel plates, application to springs (such as piano wires), addition to press oil and cutting oil, and application to other steel parts.
2. Vaporizable Corrosion Inhibitors
Vaporizable corrosion inhibitors prevent rust by forming a film of inhibitors on the surface of metal parts. The rust-preventive ingredients that form the film gradually evaporate, preventing the metal from reacting with moisture and oxygen in the atmosphere, which causes rust. Volatile rust inhibitors are used in the form of corrosion inhibitors paper or corrosion inhibitors film coated or impregnated on film or paper. By wrapping metal parts with anticorrosive paper or anticorrosive film, or by including volatile anticorrosive agents, the anticorrosive agent will gradually evaporate and exert its anticorrosive effect.
Principle of Corrosion Inhibitors
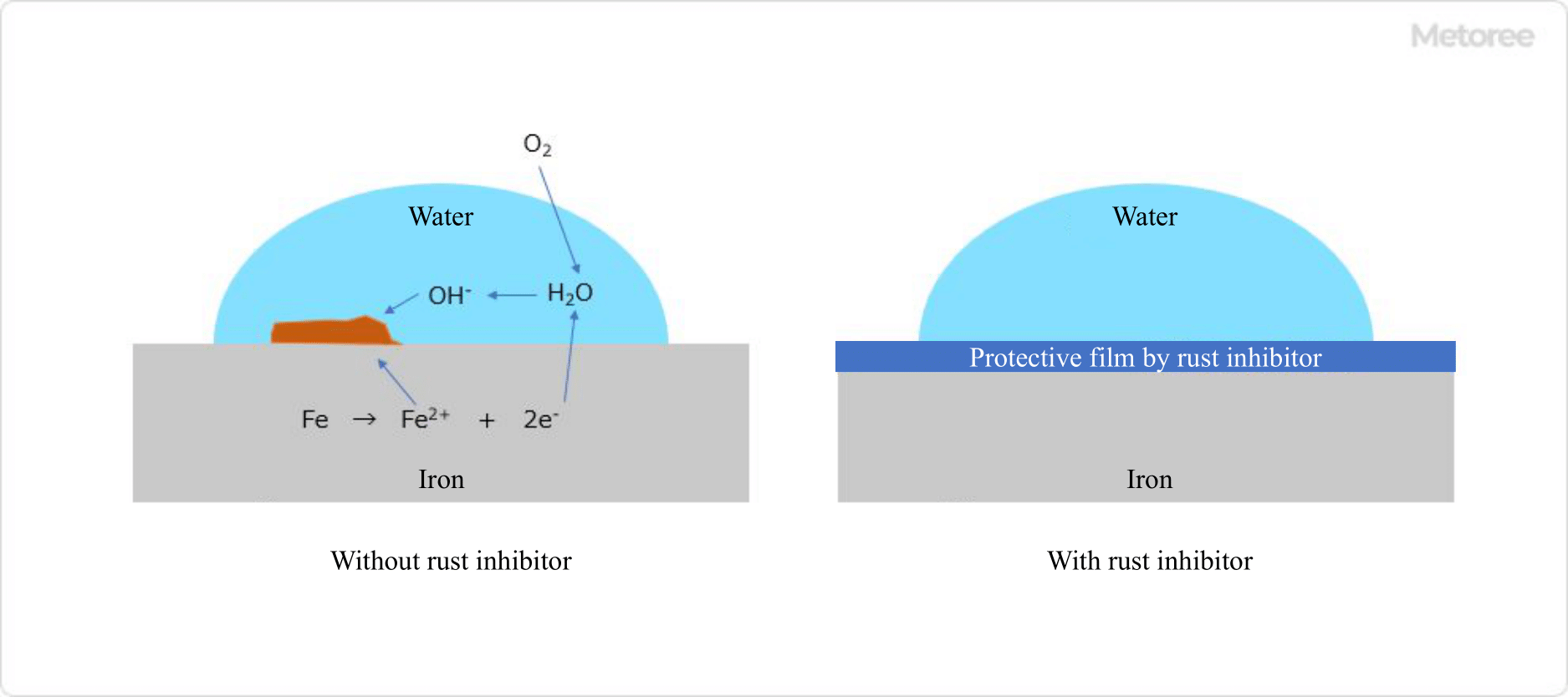
Figure 1. Mechanism of rust formation
Corrosion inhibitors inhibit rust by forming a protective film on metal surfaces that inhibits contact with water and oxygen, which causes rust.
Oxygen from the air dissolves in the water film, but the concentration of the dissolved oxygen differs between the water film surface and the metal surface.
Since rust occurs when metals come into contact with moisture and oxygen in the air, corrosion inhibitors are used to prevent rust from occurring.
Types of Corrosion Inhibitors
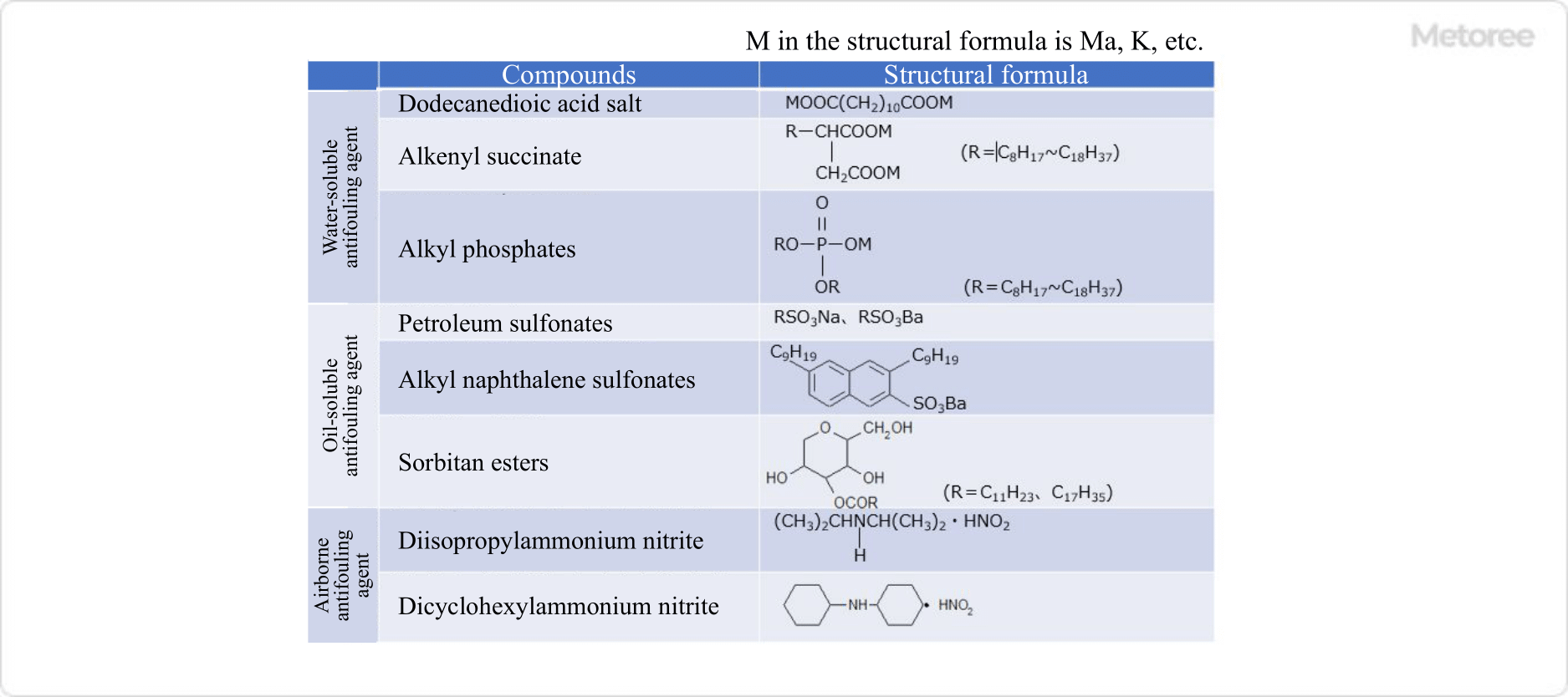
Figure 2. Typical rust inhibitors
Corrosion inhibitors are classified into three types based on their chemical properties: water-soluble corrosion inhibitors, oil-soluble corrosion inhibitors, and vaporizable corrosion inhibitors.
1. Water-Soluble Corrosion Inhibitors
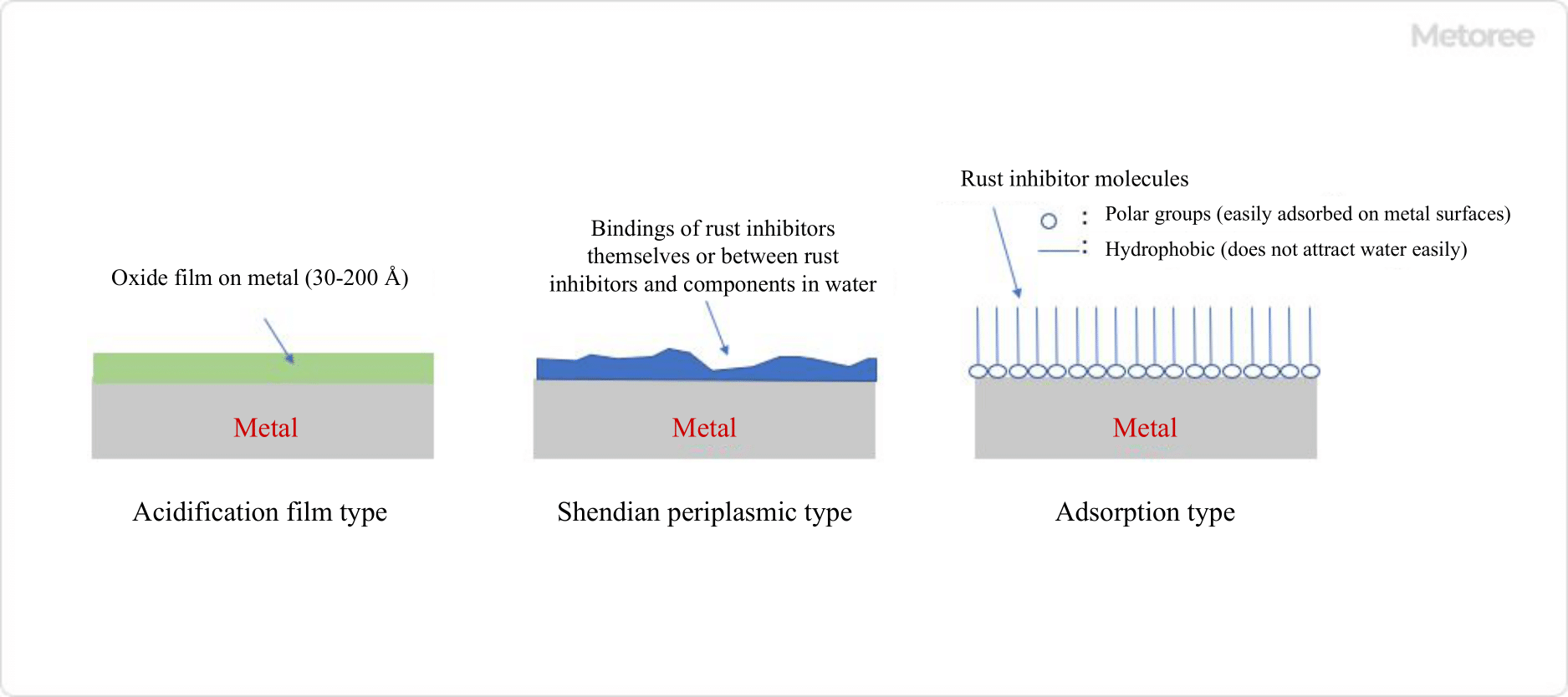
Figure 3. Rust suppression mechanism of water-soluble rust inhibitor
Water-soluble corrosion inhibitors are corrosion inhibitors that dissolve in water. They are classified into oxidized film type, precipitated film type, and adsorbed film type according to the type of film formed. Typical compounds are chromate, molybdate, polymerized phosphate, and mercaptobenzothiazole. Surfactant-type corrosion inhibitors also fall into the category of water-soluble corrosion inhibitors, and the structure of such compounds has both polar and hydrophobic groups in the molecule. The polar groups in the molecule adsorb on the metal surface and the hydrophobic groups cover the metal surface. The hydrophobic group has the property of excluding water molecules, thus reducing the formation of rust.
2. Oil-Soluble Corrosion Inhibitors
Oil-soluble corrosion inhibitors are low-polarity corrosion inhibitors that are soluble in oil and form an adsorption-type film. The structure of an oil-soluble rust inhibitor has both polar groups and hydrocarbon chains in the molecule. The hydrocarbon chain has a sufficiently long structure so that the compound as a whole is highly lipophilic. When applied to a metal surface, the polar groups adhere to the metal surface, while the hydrocarbon chains, which exhibit lipophilic properties, cover the metal surface. These hydrophobic chains retain oil components, so the metal surface is covered with a thin layer of oil.
Typical compounds are petroleum sulfonates and sorbitan esters.
3. Evaporative Corrosion Inhibitors
Vaporizable corrosion inhibitors are corrosion inhibitors that vaporize slowly at room temperature and pressure. The vaporized rust inhibitor fills the atmosphere and forms a thin film on the metal surface, thereby producing a rust-preventive effect. Typical compounds include diisopropylammonium nitrite and dicyclohexylammonium nitrite.
Other Information on Corrosion Inhibitors
Other Materials With Anticorrosive Properties
The following groups of compounds also have rust-preventive properties and are widely used:
1. Plastics
Plastics are sprayed on metal surfaces or immersed in metal to coat them, thereby preventing the formation of rust. Based on their applications and characteristics, they are classified into two types: coated and hot dipped. In the case of the paint type, the film formed is relatively thin and is easy to peel off, and in the case of the hot dipping type, the film is thicker than the coated coating.
2. Desiccant
Silica gel is a typical example of a desiccant widely used to remove moisture from packaging.
3. Oxygen absorber
Oxygen absorbers are used to prevent rust from occurring by fixing oxygen in the packaging. Iron powder, which is inexpensive and readily available, is commonly used.
4. Corrosion inhibitor
These are compounds that adsorb on metal surfaces to form their film to inhibit the generation of rust. A wide range of compounds falls under this category, including various inorganic salts and organic acids. Examples include various chromates, carboxylic acids, amine salts, and esters.
5. Chelating agents
A type of compound that forms complex salts on the surface of ferrous metals to prevent rust formation; typical examples are EDTA, gluconic acid, NTA, and HEDTA.