What Is a Coolant System?
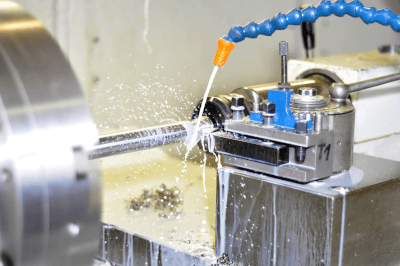
A coolant system is a device designed to supply cooling liquid. It plays a critical role in various applications by cooling heat generated during processes involving tools and objects, such as engines. Coolant systems come in various types, ranging from those used in large machine tools to those employing two fluids (coolant and lubricant) to enhance cutting efficiency and maintain tool quality.
Uses of Coolant Systems
Coolant systems find extensive use in industries such as automotive manufacturing, metalworking, cleaning equipment, and any field where heat dissipation is required. These systems serve multiple purposes, including cooling, lubrication, filtration, cleaning, rust prevention, and removal of sludge and chips.
In the automotive sector, coolant systems are essential to prevent defects and breakdowns caused by excessive engine heat. In metal processing, they are employed in various cutting machines, such as NC lathes, machining centers, milling machines, grinding machines, and specialized equipment, to prevent tool and object deterioration and distortion due to heat and foreign materials.
Principle of Coolant Systems
1. For Machine Tools
Coolant systems for machine tools consist of components like a coolant tank, pump, piping hose, nozzle, recovery system, and regeneration system. These systems spray high-pressure coolant from nozzles onto the cutting tool area to cool, lubricate, clean, and remove chips from the workpiece and cutting tools.
The used coolant undergoes various regeneration processes, including cooling, filtration, sludge removal, chip removal, and modification as necessary. The regenerated coolant is then pressurized and reused.
2. For Engines
Coolant systems for automobile engines consist of coolant, piping hoses, radiators, cooling fans, pumps, and temperature controllers. The coolant absorbs heat generated during combustion in the engine and transfers it to a heat exchanger known as a radiator.
Radiators serve as heat exchangers between the coolant and the external air, dissipating the coolant’s heat to the surroundings. Temperature controllers are employed to maintain the coolant at the appropriate temperature.
The coolant used in engines is typically a mixture of water and rust inhibitors like ethylene glycol or propylene glycol. This mixture prevents engine corrosion and freezing during winter, and it should be replaced periodically.
Engine coolant systems, similar in concept, are also used in ships, construction machinery, civil engineering machinery, agricultural machinery, power generation equipment, pump equipment, and more.
Types of Coolant Systems
1. High-Pressure Coolant System
This system pressurizes and injects coolant, efficiently cooling chips in contact with tools. It can also separate, crush, and discharge chips.
A supply pump draws coolant from a tank, and a filter (typically ceramic) effectively removes fine chips. The coolant is maintained at the desired temperature and can be reused after proper regeneration. High-pressure coolant pumps increase the coolant’s pressure, allowing it to flow out through the nozzle at high pressure.
2. Two-Component Mist Coolant System
This system utilizes both coolant and lubricating oil. It generates a mixed mist of vegetable oil and water-soluble coolant. By combining the lubricating properties of vegetable oil with the cooling effect of water-soluble coolant, semi-dry machining is achieved. This approach offers several advantages, including maintaining tool quality and reducing machining time, making it suitable for deep-hole drilling and challenging materials.
3. Engine Coolant System
Engine coolant systems are typically integrated into the engine’s components rather than being standalone units. They consist of components like pumps, radiators, cooling fans, and more.
Characteristics of Coolant Systems
Coolant systems for machine tools exhibit several characteristics:
1. Prevention of Stagnation
The flow path within the coolant tank is designed to prevent coolant stagnation, as stagnation can lead to the accumulation of sludge and chips.
2. Filtration Accuracy
Combination filtration devices can be employed to achieve filtration accuracy suitable for the specific machine tool application.
3. Temperature Control
Coolant systems can incorporate temperature controllers to maintain the coolant at the optimal temperature for machining processes.
4. Optional Functions
Additional components such as magnetic catchers, cyclone separators, and bucket separators can be installed to further enhance coolant cleanliness.