What Is Anti-Slip Tape?
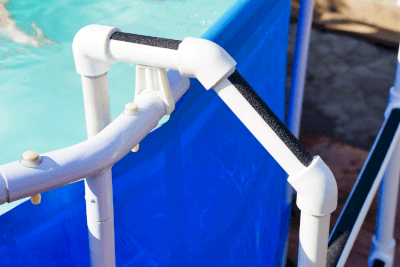
Anti-slip tape is a tape that is attached to slippery floors to prevent slips and falls.
Anti-slip tape is sold in various types, such as for striped steel plates, or iron plates with protrusions used for gutter covers, for indoor use, and for outdoor use, depending on the application and place of use.
It is used in places where people are likely to fall, such as factories where powder tends to accumulate, and it is designed not only for human walking but also for wheelchairs to prevent slipping when climbing over steps.
Uses of Anti-Slip Tape
Anti-slip tape, as mentioned above, is often used to prevent falls. Smooth surfaces are easier to clean and look more beautiful than carpets, so smooth floors such as tiles are preferred for building entrances and other places that are easily soiled.
On the other hand, smooth floors have low friction and are very prone to falling, especially when liquid is present, and falls often cause injuries, especially on rainy days. Anti-slip tape is intended to prevent these accidents.
Anti-slip tape may also be applied to stairs and other places where a slip can cause serious injury. Bathrooms in particular are even more slippery than water alone because of the use of soap and other surfactants. Anti-slip tape is used not only outdoors but also indoors to prevent hazards.
Principle of Anti-Slip Tape
Anti-slip tape is mainly plastic tape with hard mineral particles or plastic granules attached to its surface to increase friction.
The surface grains vary depending on the application, but they are firmly bonded with a resin coating so that the particles will not come off when stepped on or when a load or other object passes over them. Similarly, the adhesive strength of the tape applied to the floor is also strong, making it difficult to peel off.
Outdoor use is characterized by high water resistance and strong materials since it is exposed to rain and wind. Some of them allow you to walk without slipping as long as you step on the tape, especially when the floor is covered with oil.
Anti-slip tape of the light-storing type is also available, which releases stored light and glows in the event of a sudden power outage, making it more visible and safer.
Types of Anti-Slip Tape
Anti-slip tape is classified into different types depending on where it is used.
1. Classification by Abrasive Grain
For outdoor use, hard mineral particles are mainly used to prevent slipping, as it is expected to be stepped on or walked on with shoes on. On the other hand, for indoor or bathroom use, soft plastic is often used in consideration of touching with bare hands or bare feet.
2. Classification by Tape Color
Generally, black or gray is used. Depending on the location, some tapes are available in transparent colors to make them less noticeable, and others are available with graphics to alert people to their presence.
Classification by Substrate Material
Anti-slip tape is mostly made of plastic. There is no problem as long as the surface to which the tape is applied is flat. However, if the tape is applied to an uneven surface or striped steel plate, the adhesive surface will lift up. In such cases, the base material is made of aluminum and can be adhered to uneven surfaces.
How to Select Anti-Slip Tape
In most cases, manufacturers sell their products in categories based on the intended use scenario. However, the colors and sizes available may be limited depending on the situation of use.
Although appearance is an important factor, anti-slip tape should be selected by placing the highest priority on the effectiveness and purpose of the anti-slip tape. In particular, if a tape designed for indoor use is used outdoors, it may not be effective enough.
Other Information on Anti-Slip Tape
How to Use Anti-Slip Tape
To apply anti-slip tape, cut the tape to the required length with scissors, peel off the backing paper to reveal the adhesive side, and stick it to the floor. The key point is not to stick only one row of tape, but to stick several rows at a pitch of about 20 cm according to the size of a person’s foot, avoiding the tape and avoiding stepping directly on a wet floor.
In addition, before applying the tape, clean the adhesive surface to prevent it from peeling off, and round the corners to ensure long-lasting effectiveness. Some manufacturers recommend applying a primer to the surface to be affixed beforehand, so prior confirmation is essential.