¿Qué son los Equipos de Tratamiento de Aguas Residuales?
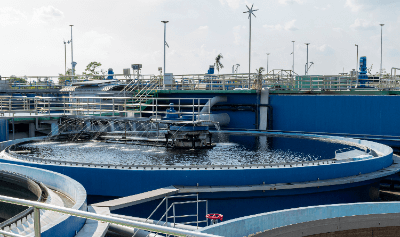
Los equipos de tratamiento de aguas residuales depuran las aguas residuales vertidas por la industria, la agricultura y otras industrias, así como las aguas residuales y otras formas de vida humana.
El tratamiento de las aguas es un proceso indispensable en nuestra vida cotidiana por lo que respecta al uso eficiente del agua, la prevención de la contaminación ambiental y los olores. Por ello, muchas empresas trabajan en innovaciones tecnológicas para mejorar la eficacia del tratamiento de las aguas residuales.
Dependiendo del tipo de aguas residuales, se requieren varios tipos de eliminación, como la eliminación de metales pesados, la eliminación orgánica, la desnitrificación y la eliminación de fósforo.
Usos de los Equipos de Tratamiento de Aguas Residuales
Los sistemas de tratamiento de aguas residuales se utilizan en todos los sectores, como la industria, la agricultura, la ganadería y las depuradoras.
En el sector industrial, existe una gran necesidad de reciclar las aguas residuales industriales en Singapur, donde el agua escasea. Las economías emergentes, como China, Oriente Medio y el Sudeste Asiático, también necesitan depurar las aguas residuales desde la perspectiva de la prevención de la contaminación ambiental, así como del reciclado de las aguas residuales.
En el sector ganadero, los sistemas de tratamiento de aguas residuales también se utilizan para prevenir la contaminación ambiental y los malos olores debido a la gran cantidad de aguas residuales que contienen grandes cantidades de heces y orina de ganado que se vierten.
Principios de los Sistemas de Tratamiento de Aguas Residuales
Por lo general, las plantas de tratamiento de aguas residuales pretratan, coagulan y sedimentan y separan y filtran las aguas residuales recibidas, que se vierten o reutilizan una vez ajustados el pH y otros parámetros. Los procesos de tratamiento de aguas residuales pueden dividirse en dos categorías principales: procesos de pretratamiento y procesos de tratamiento biológico.
1. Proceso de Pretratamiento
El proceso de pretratamiento elimina principalmente las sustancias que inhiben el tratamiento biológico. Los aceites y disolventes orgánicos, que tienden a flotar, se separan mediante un separador, mientras que los metales pesados (por ejemplo, cobre, níquel, zinc) y los sólidos en suspensión se tratan mediante coagulación y sedimentación.
2. Proceso de Tratamiento Biológico
En el proceso de tratamiento biológico, la materia orgánica se elimina del agua pretratada utilizando la capacidad de descomposición de los microorganismos. La cantidad de materia orgánica en el agua se expresa como DBO (demanda bioquímica de oxígeno) o DQO (demanda química de oxígeno), y el agua se depura hasta que estos valores caen por debajo de los estándares.
El método de fangos activados es el más utilizado en las plantas de tratamiento de aguas residuales y depuración de aguas. El método de lodos activados se refiere a un método en el que las aguas residuales son tratadas por microorganismos aerobios que utilizan el oxígeno disuelto en el agua para descomponer la materia orgánica mediante aireación y separación por sedimentación.
Otro método es el de la membrana biológica. El método de membrana biológica es un método de tratamiento en el que los microorganismos se adhieren a soportes para crear una estructura similar a una membrana, que absorbe y descompone los contaminantes de las aguas residuales.
Otra Información sobre Sistemas de Tratamiento de Aguas Residuales
1. Unidades Pequeñas de Tratamiento de Aguas Residuales
Las pequeñas unidades de tratamiento de aguas residuales se utilizan en obras de construcción y en pequeñas fábricas. Esto se debe a que el volumen de aguas residuales vertidas es pequeño y puede tratarse dentro de las instalaciones.
Las aplicaciones incluyen aguas residuales de detergentes, aguas residuales de molienda y aguas residuales del procesado de alimentos. Debido a su pequeño tamaño, pueden transportarse en camiones de 2 a 4 toneladas e instalarse fácilmente. Además, pueden realizar la serie de operaciones de tratamiento descritas anteriormente, son sencillas de manejar y requieren bajos costes de inversión de capital.
Por otro lado, cada día se vierte una gran cantidad de aguas residuales domésticas e industriales. Por lo tanto, los equipos de tratamiento de aguas residuales propiamente dichos no son adecuados para su uso en pequeñas unidades de tratamiento de aguas residuales, ya que son de gran envergadura.
2. Equipos de Tratamiento de Aguas Residuales en Fábricas
Las aguas residuales de las fábricas contienen muchos contaminantes. Por lo tanto, es necesario considerar el equipo de tratamiento según el tipo de contaminante y las características de las aguas residuales de cada planta.
Tipo de Contaminante
El equipo de tratamiento debe considerarse para cada sustancia presente en el agua tratada, como aceite, materia orgánica, amoníaco y metales tóxicos. Por ejemplo, las instalaciones de lodos activados son necesarias para reducir la DBO (demanda bioquímica de oxígeno) y la DQO (demanda química de oxígeno), mientras que las instalaciones de sedimentación por coagulación son necesarias para tratar los SS (sólidos en suspensión).
Características de las Aguas Residuales de las Distintas Plantas
Las especificaciones de los equipos difieren de una planta a otra, ya que la concentración de sustancias peligrosas en el agua tratada, el pH y otras características de los efluentes difieren en cada planta, como las alimentarias, las de componentes electrónicos, las de petróleo y las petroquímicas. En el caso de las plantas alimentarias, se incluyen el tratamiento anaeróbico por fermentación metánica y la filtración mediante biofiltros.
En el caso de las plantas de componentes electrónicos, las aguas residuales inorgánicas y orgánicas se tratan por separado, ya que se utilizan muchas sustancias inorgánicas como el flúor y el arsénico. La concentración de cada sustancia peligrosa en el agua tratada de la planta viene determinada por las leyes y normativas pertinentes. Para alcanzar la concentración de tratamiento requerida, las especificaciones de los equipos se determinan una vez establecidas las condiciones previas de la cantidad de agua tratada y la concentración de agua bruta.