¿Qué son las Buretas?
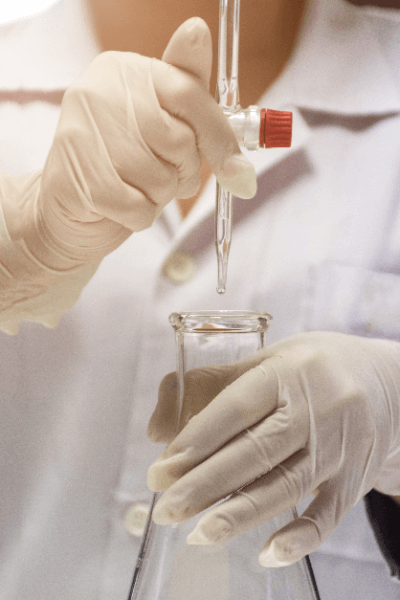
Una bureta es un recipiente de vidrio que puede medir el volumen de una gota de líquido dejando caer una pequeña cantidad de líquido en su interior mientras se acciona con un grifo. En el fondo de un tubo cilíndrico delgado de vidrio con una escala graduada hay un grifo desmontable.
También se puede utilizar una pipeta para medir el volumen de una gota de líquido, pero las Buretas se pueden utilizar en posición vertical, por lo que la escala se puede leer con mayor precisión y la cantidad de líquido se puede ajustar finamente con el grifo. Además, el grifo puede utilizarse para controlar con precisión el volumen de la gota, lo que hace que la bureta sea adecuada para experimentos como valoraciones de neutralización, en los que se requiere una medición precisa del volumen de líquido.
Usos de las Buretas
Las buretas se utilizan principalmente para valoraciones de neutralización. La valoración por neutralización es un tipo de análisis volumétrico en el que la concentración de una solución de concentración desconocida se determina utilizando una solución patrón de concentración conocida y una solución de concentración desconocida que reacciona en proporción a la concentración de la solución patrón.
El juicio de la reacción de neutralización, el llamado punto final, se determina por el cambio de color de la mezcla después de la gota. El manejo de la bureta requiere un cierto grado de destreza, pero también existe la bureta automática, que puede manejarse de forma automática y se utiliza para el control de calidad en la industria alimentaria, farmacéutica y química.
Características de las Buretas
Las buretas existen tanto en color blanco como en color tostado. Como ocurre con otros materiales de vidrio, esta elección depende del tipo de sustancia disuelta en la solución patrón, ya que algunas sustancias reaccionan con la luz. Por ejemplo, el nitrato de plata es fotosensible y debe utilizarse en condiciones protegidas de la luz, por lo que debe emplearse una Buretas marrón cuando se utilice como valorante.
Además, como se ha mencionado anteriormente, es importante familiarizarse con el funcionamiento del grifo de las buretas. Es importante operar la llave de manera que el líquido pueda gotear a una velocidad adecuada, ya que una velocidad de goteo rápida de las buretas puede resultar en la adición de más solución estándar que el punto final. Tenga en cuenta que el grifo debe mantenerse engrasando la pieza del grifo, y un mantenimiento insuficiente puede provocar fugas de líquido, etc.
Además, si la punta se astilla, es imposible medir con precisión el volumen, por lo que debe manipularse con cuidado. Los experimentos han demostrado que incluso un arañazo en la punta puede cambiar el volumen por gota. También se ha demostrado que el volumen de gotas residuales varía en función del volumen de líquido residual en las buretas, por lo que siempre es aconsejable utilizar las buretas desde la parte superior de la escala, que es el punto cero.
Dado que la bureta es una pieza de vidrio, el calentamiento y el enfriamiento repetidos la deforman, lo que perjudica la precisión de su volumen de medición. Por esta razón, debe evitarse calentarla y secarla después de limpiarla, y la bureta debe secarse a temperatura ambiente. Por la misma razón, el valorante que se coloque en las buretas debe ser un líquido de temperatura constante, generalmente en torno a la temperatura ambiente. Debe tenerse en cuenta que la temperatura del valorante no sólo provoca la dilatación y deformación de las buretas, sino también que el volumen del valorante depende de la temperatura. Por esta razón, el valorante debe estar a una temperatura constante para una medición precisa del volumen.
Razones para el co-lavado de Buretas
El co-lavado es el proceso de lavar un dispositivo de recipiente lateral (un instrumento utilizado para medir el volumen de un líquido), como una buretas o una pipeta entera, con la solución que se va a pesar (la solución que se va a poner dentro).
Los instrumentos de recipiente lateral no suelen calentarse ni secarse en un secador para evitar cambios de volumen debidos a la deformación del instrumento. Después de lavarlos con agua del grifo, se enjuagan con agua destilada y se lavan con la solución que se va a pesar inmediatamente antes de su uso.
La razón del lavado conjunto es que la concentración de la solución de muestra se reduce si la superficie interior del instrumento está mojada con agua. En cambio, si se moja con la propia solución de la muestra, la concentración no cambiará al añadir la solución.
Las buretas se utilizan para introducir soluciones de concentración desconocida durante la valoración, por lo que si la concentración de la solución cambia en las buretas, no será posible obtener una concentración exacta.
Además, si lavas el aparato una vez que vuelvas a utilizarlo, podrás seguir utilizándolo sin dejar que se seque.
En primer lugar, llene las buretas con aproximadamente 1/5 de la solución y lave las paredes interiores mientras gira las buretas de lado. A continuación, gire el grifo (tapón vivo) para dejar salir la solución por la punta, lave la pared interior por debajo del grifo y deseche el líquido restante de la parte superior. Repita esta operación varias veces.
Cómo utilizar las Buretas
Fije las buretas verticalmente al soporte de buretas y asegúrese de que el grifo vivo está cerrado.
Con ayuda de un embudo, vierte la solución por la parte superior del tubo de vidrio. En este punto, deja un espacio entre el embudo y la parte superior de las buretas para permitir que salga el aire y que la solución no rebose por la parte superior del embudo. Además, para evitar el riesgo de que la solución entre en contacto con los ojos, vierta la solución por debajo de los ojos. Una vez vertida la solución, retira el embudo.
Abra el tapón con un vaso de precipitados u otro recipiente debajo y vierta la solución enérgicamente para expulsar completamente el aire de la zona situada debajo del tapón. Si hay burbujas de aire por encima del tapón, también deben eliminarse.
Una vez expulsado el aire, lea y registre la escala. En este punto, la línea de visión debe ser perpendicular a las buretas y debe leerse el fondo (extremo inferior) del “menisco”. El menisco es la superficie curvada del líquido en un tubo estrecho debido a la tensión superficial, o una abolladura si el líquido moja la pared del tubo. La escala también se lee a ojo con una precisión de 1/10 de escala.
Gire el tapón vivo para iniciar el goteo. Sujete la bureta con una mano y tire de ella hacia el cuerpo de la bureta para evitar que el tapón se caiga.
Una vez finalizada la valoración, lee la escala y da el volumen de valoración.