What Is a CAD VR?
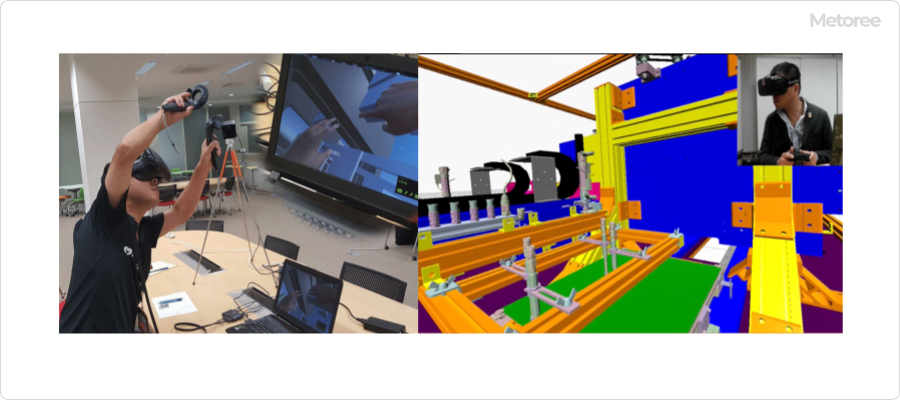
CAD VR is a fusion of 3D CAD (Computer-Aided Design) commonly used in architecture and manufacturing, and VR (Virtual Reality) technology. It allows data designed with 3D CAD software to be visualized in a stereoscopic manner within a VR environment.
3D CAD serves as a tool for designing three-dimensional industrial products and structures. Widely used across industries, it offers advantages such as more advanced simulation and analysis compared to 2D CAD. On the other hand, VR technology provides a means to create realistic experiences within virtual spaces. The combination of 3D CAD and VR enables the direct incorporation of design data into VR environments, allowing users to pseudo-experience the shapes and sizes of products and structures.
Uses of CAD VR
In the field of product design, discrepancies between the imagined and actual outcomes are common. Issues like “columns being thinner than expected” can be attributed to the limitations of designing on 2D displays. Even with 3D CAD design, there are constraints in verifying designs on 2D screens, making it challenging for experienced professionals to fully grasp the actual image.
This is where VR brings innovation. By utilizing VR, designed objects can be viewed in actual size in three dimensions, facilitating intuitive understanding. The ability to experience CAD models at the same scale as physical objects allows even those without specialized knowledge to easily comprehend shapes and sizes, significantly improving communication. With VR, individuals less skilled in detailed design can review design content as if they were on-site, enhancing their intuitive understanding of projects.
Especially for those without expertise in design, engineering, or architecture, VR has become a groundbreaking tool. It allows the perception of three-dimensional shapes and scales that are difficult to understand from 2D drawings or 3D models, providing a method to explore them as if physically walking through them. This deepens intuitive understanding of projects, making designs more widely accepted.
VR serves as a valuable tool across various fields, from design reviews to customer presentations and educational training. Elevate product development to the next level and achieve intuitive and precise design.
Types and Classifications of CAD VR
VR can be classified based on usage, functionality, and data processing methods. The classifications provided here are indicative of VR systems for the manufacturing industry, and the selection should be tailored to the company’s requirements and objectives.
1. Classification Based on Data Storage and Processing Methods
Local Version
VR content and software are installed directly on the user’s device (e.g., PC or VR headset) and run on that device. Since the user’s device processes the content directly, there is no network delay, and high real-time performance can be expected. Additionally, products with high confidentiality often use the local version.
Cloud Version
VR content and software run on servers in the cloud and the results are streamed to the user’s device. This requires the ability to receive and display streaming content. Factors such as internet bandwidth, latency, and the quality of cloud services may impact the quality of the VR experience. With the widespread adoption of 5G and advancements in edge computing, the quality of cloud-based VR experiences has improved, leading many companies and service providers to enter this field.
2. Classification Based on Purpose
Design Verification and Prototyping
Using VR for the confirmation and improvement of product design and prototypes.
Training and Education
Utilizing VR for training purposes, such as manufacturing process training and safety education.
Remote Collaboration
Using VR for simultaneous connections and collaborative work from multiple locations.
Product Presentation
Using VR for product introductions and demonstrations at exhibitions for customer-facing purposes.
3. Classification Based on Supported Devices
Standalone VR
Systems designed for VR devices that operate independently. These systems are portable and easy to set up anywhere without the need for external PCs or sensors. While convenient, the processing power is limited compared to high-performance PCs.
PC-Connected VR
Systems designed for VR devices that connect to high-performance PCs. This allows leveraging the capabilities of high-performance PCs for complex simulations and high-quality real-time rendering. However, the need for PC connectivity makes them less portable and more complex to set up.
4. Classification Based on Interactivity
Static VR
Basic VR is designed for simple 3D viewing purposes, similar to a 3D viewer.
Interactive VR
VR allows the simulation of product operations and the execution of tasks within virtual spaces. It enables experiencing mechanism simulations.
How to choose CAD VR
To effectively utilize 3D data within an organization, careful selection of VR systems is crucial. Starting on a small scale is recommended, with key considerations being accessibility for all users. Ease of use for everyone, at any time, is essential.
When choosing a VR system for the manufacturing industry, consider the following points:
1. Clarification of Purpose
Not all systems can meet every purpose. Whether it’s prototype evaluation, production line simulation, or training materials, selecting the most suitable VR system based on the specific purpose is crucial. Understand who will use it for what purpose and in what situations.
2. Budget
The cost of hardware and software used can significantly impact system selection. Considering the risk of obsolescence, especially with new hardware products being announced annually, set a budget initially and choose the most suitable system within that range. Don’t forget to include maintenance costs for the following years.
3. System Performance
The required performance of the VR system depends on the complexity and detail of simulations and designs in manufacturing. For scenarios demanding high real-time rendering and complex simulations, a high-performance PC-connected VR system is suitable.
4. User-Friendliness
Select a VR system that is user-friendly even for those without a technical background. Intuitive operability and support infrastructure are crucial points for system selection. Especially for VR, it’s essential to investigate whether users can intuitively reach their destinations, move as intended, and experience a sense similar to reality.
5. Expandability
Choosing a system that can adapt to future needs and technological advancements is vital for long-term investment. Systems that easily support software and hardware updates or introduce additional features later on are favorable.
6. Compatibility
Confirm the compatibility of existing CAD data and other software to efficiently build a VR environment. Checking compatibility with intermediate formats such as Parasolid and STEP is also necessary.
7. Security
As manufacturing data often involves high confidentiality, verifying the security features and privacy measures of the VR system is crucial. For highly confidential data, opting for the local version is recommended.
8. Support System
Consider the support system for software and hardware troubleshooting, support for updates, and training. For beginners, systems developed domestically with Japanese language support are recommended.
Other information on CAD VR
Manufacturing Industry and Game Engines
There is a significant correlation between VR systems for the manufacturing industry and game engines. While game engines are originally tools for game development, their advanced 3D rendering capabilities, physics engines, and scripting features are also utilized in VR system development.
In the development of VR applications for the manufacturing industry, game engines like Unity and Unreal Engine are commonly used. Using game engines facilitates the rapid development of VR applications, enabling easy creation of realistic representations and virtual spaces.
Realistic Representations:
The use of advanced physics simulations and high-quality 3D graphics allows the creation of realistic virtual environments. Extensive scripts and plugins can be utilized for customization tailored to specific applications. Significant utilization in major manufacturing industries has been observed in recent years.
VR/AR/MR/XR
In recent years, not only Virtual Reality (VR) but also Augmented Reality (AR), Mixed Reality (MR), and the overarching term Extended Reality (XR) have been actively utilized in the manufacturing industry. These technologies bring innovation to manufacturing processes, enhancing efficiency, quality, cost-effectiveness, and training reinforcement.
These evolving XR technologies are expected to drive further efficiency and innovation in the manufacturing industry. Leveraging these technologies allows for the establishment of flexible and smart production systems, enabling rapid adaptation to market changes. Moreover, they contribute to improving overall competitiveness in terms of product quality, cost reduction, and enhanced safety in the working environment throughout the manufacturing sector.