Was ist Bentonit?
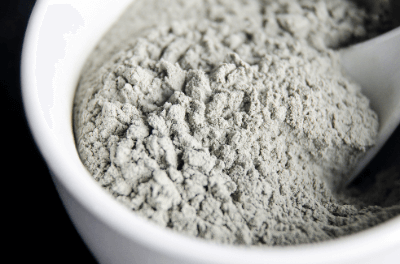
Bentonit ist eine allgemeine Bezeichnung für Ton, der aus einem Gemisch verschiedener Zusammensetzungen wie Quarz, Glimmer und Calcit besteht, mit Montmorillonit als Hauptbestandteil.
Bentonit zeichnet sich durch seine hohe Wasseraufnahmefähigkeit aufgrund der Schichtstruktur seines Hauptbestandteils, des Montmorillonits, und seine hohe Viskosität nach dem Aufquellen aus. Aus diesem Grund wird es in der Industrie und im Bauwesen, einschließlich der Keramik, häufig verwendet. Es wird auch häufig als Zusatzstoff in Arzneimitteln, Kosmetika, Reinigungsmitteln und anderen Produkten des täglichen Bedarfs verwendet.
Anwendungen von Bentonit
Bentonit ist ein Ton, der sich durch eine hohe Wasseraufnahmefähigkeit und eine hohe Viskosität nach dem Quellen auszeichnet und in einer Vielzahl von Anwendungen eingesetzt wird, von der Keramik über das Bauwesen bis hin zu Produkten des täglichen Bedarfs und Arzneimitteln. Im Folgenden werden einige der wichtigsten Anwendungen genannt:
- Keramik: Material für Keramiken
- Bauwesen: Abdichtungsmaterial für Hoch- und Tiefbauarbeiten, Schlammwasser bei Ausgrabungen
- Haushaltsprodukte: Zusatzstoffe zur Verbesserung der Dispergierbarkeit, Viskosität und Feuchtigkeitsbindung in Kosmetika, Reinigungsmitteln, Seifen und Agrochemikalien
- Pharmazeutische Produkte: Grundlage für pharmazeutische Salben
- Lebensmittel: Trübungsentferner in Wein und Pflaumenwein
- Sonstiges: Gemischt mit Sand zur Herstellung von Schimmelpilzen, Katzenstreu, Adsorptionsmittel für Verunreinigungen bei der Ölraffination
Funktionsweise des Bentonits
Bentonit ist ein Ton, der hauptsächlich aus einer Mineralart (Montmorillonit) besteht. Weitere Bestandteile sind Silikatmineralien wie Quarz und Opal, Silikatmineralien wie Glimmer und Zeolith sowie Karbonat- und Sulfatmineralien wie Calcit.
Bentonitvorkommen gibt es in Japan, den USA, China, Griechenland und der Türkei. Man geht davon aus, dass die wichtigsten in Japan und im Ausland abgebauten Vorkommen dadurch entstanden sind, dass Sedimente aus Vulkanausbrüchen, die vor etwa 200 Millionen bis mehreren Millionen Jahren stattfanden, aufgrund von Temperaturschwankungen und erhöhtem Druck physikalische und chemische Metamorphose erfahren haben, während sie tief unter der Erde begraben waren.
Montmorillonit, der Hauptbestandteil von Bentonit, ist ein feines Partikel mit einer Schichtstruktur aus dünnen Erzschichten, zwischen denen Wassermoleküle und ionische Bestandteile in Abständen von etwa 1 nm gehalten werden. Die hohe Wasseraufnahmefähigkeit von Bentonit ist vor allem auf die Zwischenschichtstruktur von Montmorillonit zurückzuführen, und es ist bekannt, dass die ionischen Komponenten im Montmorillonit eine wichtige Rolle bei der Quellwirkung spielen.
Arten von Bentonit
Die Struktur des Bentonits wird durch die Schichtstruktur seines Hauptbestandteils, des Montmorillonits, bestimmt. Dieser Montmorillonit besteht aus tetraedrischen Schichten, d. h. Schichten aus Tetraedern, die aus Silizium und Sauerstoff bestehen, und oktaedrischen Schichten, d. h. Schichten aus Oktaedern, die aus Aluminium und Hydroxylgruppen bestehen. Ein oktaedrisches Blatt ist dann zwischen zwei tetraedrischen Blättern eingebettet.
In der Praxis hat das oktaedrische Blatt eine Struktur, bei der ein Teil des Aluminiums im oktaedrischen Blatt durch Magnesium ersetzt wurde. Da Aluminium dreiwertig und Magnesium zweiwertig ist, werden in die Schichten Kationen, so genannte Zwischenschichtkationen, eingebaut, um die elektrischen Ladungen auszugleichen.
Es gibt vier Haupttypen von Zwischenschichtkationen: Na+, Ca2+, K+ und Mg2+. Die Bentonitarten werden nach der Art der Zwischenschichtkationen unterteilt, und es gibt zwei Typen: Na-Bentonit und Ca-Bentonit.
1. Na-Bentonit
Bentonit vom Na-Typ ist ein Bentonit mit einem hohen Anteil an Na+-Ionen in den Zwischenschichtkationen des Montmorillonits und zeichnet sich durch eine ausgezeichnete Quell-, Verdickungs- und Suspensionsstabilität aus.
2. Ca-Bentonit
Ca-Bentonit ist ein Bentonit mit einem hohen Anteil an Ca2+-Ionen in den Zwischenschichtkationen des Montmorillonits; Ca-Bentonit ist dem Na-Bentonit in Bezug auf Quellung, Verdickung und Suspensionsstabilität unterlegen, verfügt aber über ausgezeichnete Wasseraufnahmeeigenschaften.
Einige Bentonite des Ca-Typs werden künstlich zum Na-Typ gemacht, indem man dem Bentonit des Ca-Typs einige Gew.-% Natriumcarbonat hinzufügt, was als aktivierter Bentonit bezeichnet wird. Die Eigenschaften dieses aktivierten Bentonits ähneln denen des Na-Typ-Bentonits.
Weitere Informationen zu Bentonit
1. Toxizität von Bentonit
Bentonit ist bei normalem Gebrauch nicht toxisch, wie seine Verwendung in Haushaltsprodukten und Arzneimitteln beweist. Es wird häufig als Lebensmittelzusatzstoff verwendet, da es kaum Hautreizungen hervorruft und oral unbedenklich eingenommen werden kann. Insbesondere können feine Bentonitpartikel Verunreinigungen adsorbieren und werden als Filterhilfsmittel in der Lebensmittelproduktion verwendet, z. B. bei der Filtration von Bier und anderen alkoholischen Getränken und Softdrinks.
Nach dem Sicherheitsdatenblatt für Bentonit beträgt der LD50-Wert (halbtödliche Dosis: ein Maß für die akute Toxizität) bei oraler Aufnahme durch Ratten 5 000 mg/kg. Aus diesem Wert lässt sich schließen, dass Bentonit in der Einstufung des Gesetzes über die Kontrolle giftiger und schädlicher Stoffe zur Klasse der üblichen Stoffe gehört.
Andererseits kann das Einatmen großer Mengen von Bentonitstaub über die Nase oder den Mund zu einer Pneumokoniose führen. Pneumokoniose ist eine Krankheit, die durch die Ansammlung von Staub in den Atemwegen verursacht wird.
Zunächst treten keine Symptome auf, doch mit der Zeit können Beschwerden wie Husten, Schleim, Kurzatmigkeit und Atemnot auftreten. Ist die Pneumokoniose einmal ausgebrochen, gibt es keine Heilung, und die Krankheit kehrt nicht in die normale Lunge zurück. Aus diesem Grund wird Bentonit zusammen mit Talk und anderen Stäuben in der Klassifizierung der Staubgefahrenstufen der Japan Society for Occupational Health als Staub der Klasse 1 eingestuft.
2. Bentonit im Bauwesen
Bentonit wird als Rohstoff für Schlamm verwendet, um die Wände des ausgehobenen Bodens bei Gebäudefundamenten und Infrastrukturverstärkungsarbeiten zu schützen. Der Grund dafür ist, dass das einfache Ausheben des Bodens zum Einsturz der Seitenwände des ausgehobenen Bereichs führen kann. Das Einstürzen der Seitenwände wird verhindert, indem das Loch mit Schlamm gefüllt wird, der aus einer Mischung von Wasser und Bentonit hergestellt wird.
Dabei wird die Tatsache ausgenutzt, dass Bentonit bei Zugabe von Wasser aufquillt und seine Viskosität zunimmt, so dass es in den Aushub eindringen kann, um die Seitenwände zu stabilisieren und gleichzeitig eine starke, dünne Schlammschicht an der Oberfläche zu bilden, die einen teilweisen Einsturz des Aushubs verhindert. Außerdem verhindert es, dass sich die bei der Ausgrabung anfallenden Sedimente auf dem Boden absetzen. Aufgrund dieser Eigenschaften wird er eingesetzt, wenn ein sicherer und effizienter Aushub erforderlich ist.
Bentonit-Schlamm ist außerdem kostengünstig und hat den Vorteil, dass er leicht zu verarbeiten ist. Nachteilig ist jedoch, dass er anfällig für den Salzgehalt des Bodens und instabil gegenüber Temperaturen ist.
Er ist nicht sehr wirksam bei der Verhinderung des Einsturzes von Seitenwänden und eignet sich daher für den Einsatz in flachen Baugruben. Dem Bentonitschlamm können verschiedene Zusätze wie Dispergier- und Schmiermittel beigefügt werden, um ihn an die Aushubbedingungen anzupassen.