What Is an Aerial Cable?
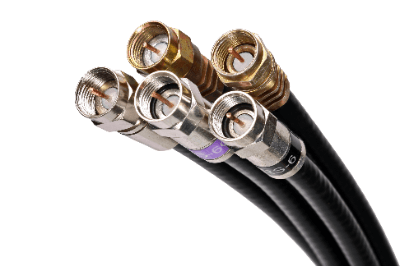
An aerial cable is a cable used to receive terrestrial and satellite broadcasts.
It is connected to a dedicated terminal called the “F” tangent terminal on the back of a TV or HDD recorder. Digital terrestrial broadcasting signals are received by a dedicated UHF receiving antenna installed outside the room.
For BS digital broadcasting and CS digital broadcasting, a dedicated parabolic antenna is used to receive broadcast signals. Since BS and CS digital broadcasting waves are sent from broadcasting satellites located in relatively the same direction, a single parabolic antenna can receive both types of broadcasting simultaneously.
Uses of Aerial Cables
Aerial cables are used to distribute broadcasts received by an antenna to video equipment. The following are examples of uses for aerial cable.
- For receiving broadcasts from home-use televisions
- For Blu-Ray players
- For HDD recorders
- For coaxial cameras
Mainly used for broadcasting transmission and reception. However, since it is a coaxial cable, it can also be used for camera video transmission if the plug is compatible.
Principle of Aerial Cables
Aerial cable is a type of cable called coaxial cable. It consists of a core wire, insulator, outer conductor, and outer sheath.
1. Core Wire
The core wire is the part that transmits and receives electrical signals. In most cases, copper wire is used, and it is characterized by its single-core structure instead of a stranded wire structure. Three diameters are mainly used: 5.4 mm, 6 mm, and 7.7 mm.
2. Insulator
The insulator is a component that insulates the core wire and outer conductor, and is mainly made of polyethylene in most cases. The outer sheath is used to protect the entire cable from the external environment and is made of vinyl or similar material.
3. Outer Conductor
The outer conductor is the signal wiring that surrounds the outer circumference of the insulation and is made of reticulated copper. The outer conductor is generally grounded and also serves as a shielding layer to protect the core wire from noise.
Signals are transmitted by a weak voltage between the outer conductor and the core wire.
Other Information on Aerial Cables
1. Signal Distribution by Aerial Cable
After broadcast signals are received from the aerial cable, they are sent through the cable to the wall terminal in each room. If the antenna and the wall terminal are far apart, or if there are many rooms, the signal is amplified and distributed by a device called a booster.
After the wall terminal, the signal is sent to the receiving equipment via aerial cable. Since the frequencies of terrestrial and BS/CS broadcasting are very different, separate cables must be used for each of these signals.
2. Differences Between Terrestrial and BS/CS Broadcasting
Terrestrial wave broadcasting has a frequency range of 470-710 MHz. These broadcast signals are converted into signals that can be processed inside receivers, such as televisions.
After the high-frequency signals in the 470-710 MHz range are converted into a frequency band known as the baseband signals, they are decrypted using a B-CAS card. Since video/audio signals and program information signals are mixed in the signals, they are separated from each other. The separated signals are decoded and finally projected on the screen.
BS Broadcasting
BS broadcasting is an abbreviation for “Broadcasting Satellites.” It is received by a parabolic antenna, down-converted to the frequency band 1022-1522 MHz, known as BS-IF, and input to a tuner for BS broadcasting.
CS Broadcasting
CS broadcasting is an abbreviation for “communication satellites,” and is also called 110-degree CS digital broadcasting.
3. Aerial Cable Standards
Aerial cables are marked with a part number such as “S-5C-FB”. This printout indicates the standard of the Aerial Cable, etc.
First Letter
The first letter “S” means that the cable is compatible with satellite broadcasting.
Second Character
The second “5” indicates the thickness of the cable (unit: mm). The second “2” indicates an outer diameter of 4 mm, “3” indicates an outer diameter of 5.4 mm, “4” indicates an outer diameter of 6 mm, and “5” indicates an outer diameter of 7.7 mm.
Third Letter
The third “C” refers to the impedance of the cable. C” stands for 75Ω (for TV) and “D” for 50Ω (for radio).
Fourth Letter
The fourth “F” represents the material of the insulation. F” stands for foamed polyethylene and “2” stands for polyethylene.
Fifth Letter
The last “B” indicates the type of wire braid. B” indicates that the braid consists of aluminum foil wrapped inside the braid, “V” indicates that the braid is a single-layer, “W” indicates that the braid is a double-layer, and “T” indicates that the braid is a triple-layer.
4. Types of Antenna Cable Plugs
There are several types of aerial cable plugs. It is important to select the most suitable plug according to the type of aerial cable to be connected and the location where it will be used.
Straight Type
This is the most common type of plug and is suitable for connection between a TV and a recorder, for example. It is not suitable for use in confined spaces, as the cable is easily overloaded when bent.
L-Shaped Plug
The plug is bent in an L-shape and is suitable for use in confined spaces.
F-Type Plug
This plug has a threaded groove on the inside. It is connected to the Aerial Cable by screwing it in. The advantage of this plug is that it is difficult to disconnect due to the screw type.
Mixed Type
This type has a different shape at both ends, such as straight at one end and L-shaped at the other end.