What Is a Centrifuge?
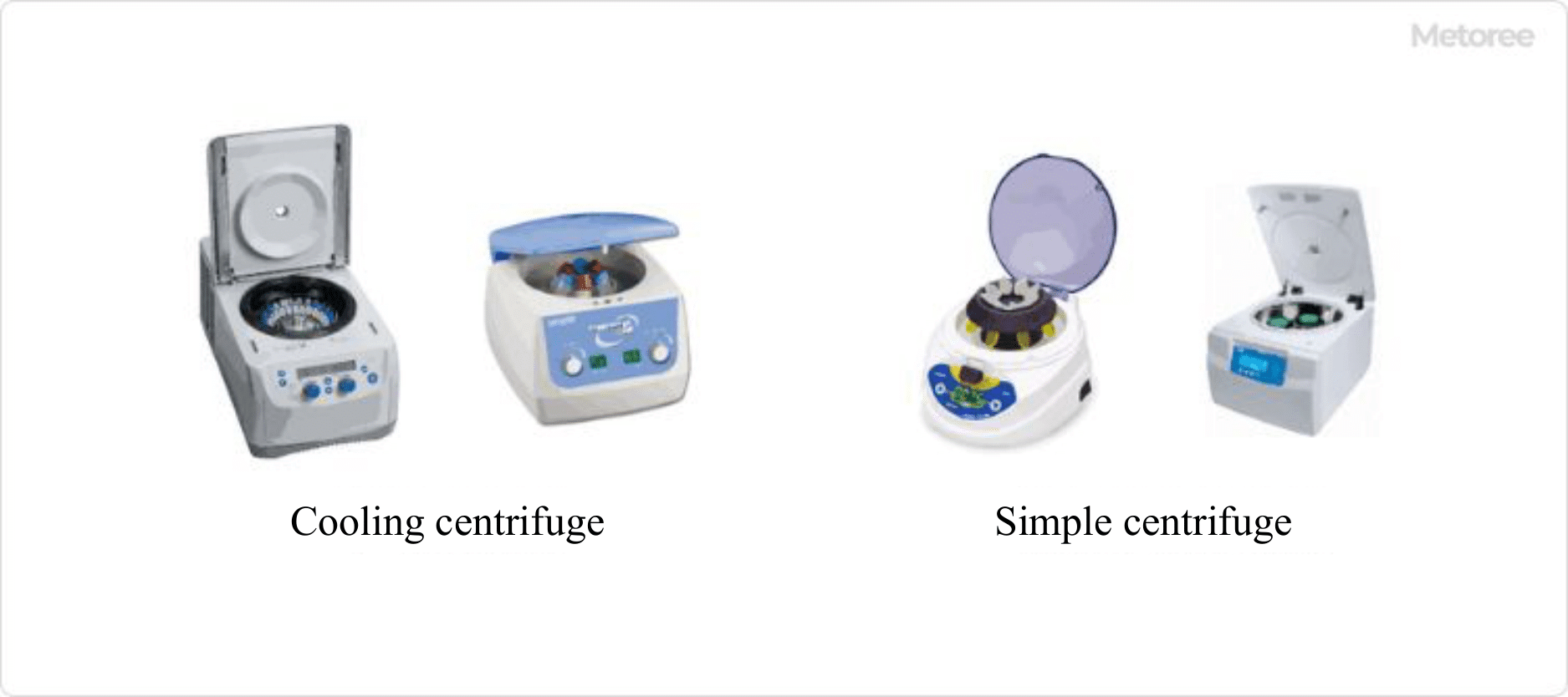
Figure 1. Various experimental centrifuges
A centrifuge is a machine that separates mixtures of different specific gravities (liquid-liquid or liquid-solid) by applying centrifugal force.
Mixtures can settle spontaneously using the difference in specific gravity (e.g., using a separating funnel). Still, it separates with gravity (1G) and takes longer to complete. Centrifuges can apply forces of several thousand Gs, which allows for faster separation. Centrifuges that can apply tens of thousands of Gs or more are called ultracentrifuges.
Uses of Centrifuges
Centrifuges are used in various applications, such as in laboratories of universities and companies, medical institutions, and manufacturing plants. In each field, products are used according to the application and scale.
1. Uses in Laboratories
Centrifuges are often used in biochemistry laboratories. Typical applications include the collection of cells mixed in liquids and the separation and collection of proteins and peptides.
In the pharmaceutical industry, it separates mixed liquids of different specific gravity. In quality control laboratories, it often analyzes pharmaceutical ingredients. In both cases, experimental samples are used.
2. Uses in Medical Institutions
In medical institutions, they are used for blood tests such as coagulation tests and biochemical tests. When blood collected in a blood collection tube containing an anticoagulant is subjected to centrifugal separation, plasma can be collected as the supernatant as the blood cell components settle to the bottom of the tube (coagulation test).
If blood is collected in a container that does not contain anticoagulant and allowed to coagulate, and then centrifuged, the solids (blood cell and coagulation components) will settle, and the serum can be collected as the supernatant (biochemistry test).
3. Uses in Industrial Applications
In industrial applications, it is used in food factories for refining sugar and separating milk fat and in chemical plants for deliquescence of resins, separation of slurry, and recovery of catalysts. They are also used in the fields of sewage treatment and sludge treatment. Centrifuges mainly used in these industrial fields are decanter centrifuges and cylindrical centrifuges.
Principles of Centrifuges
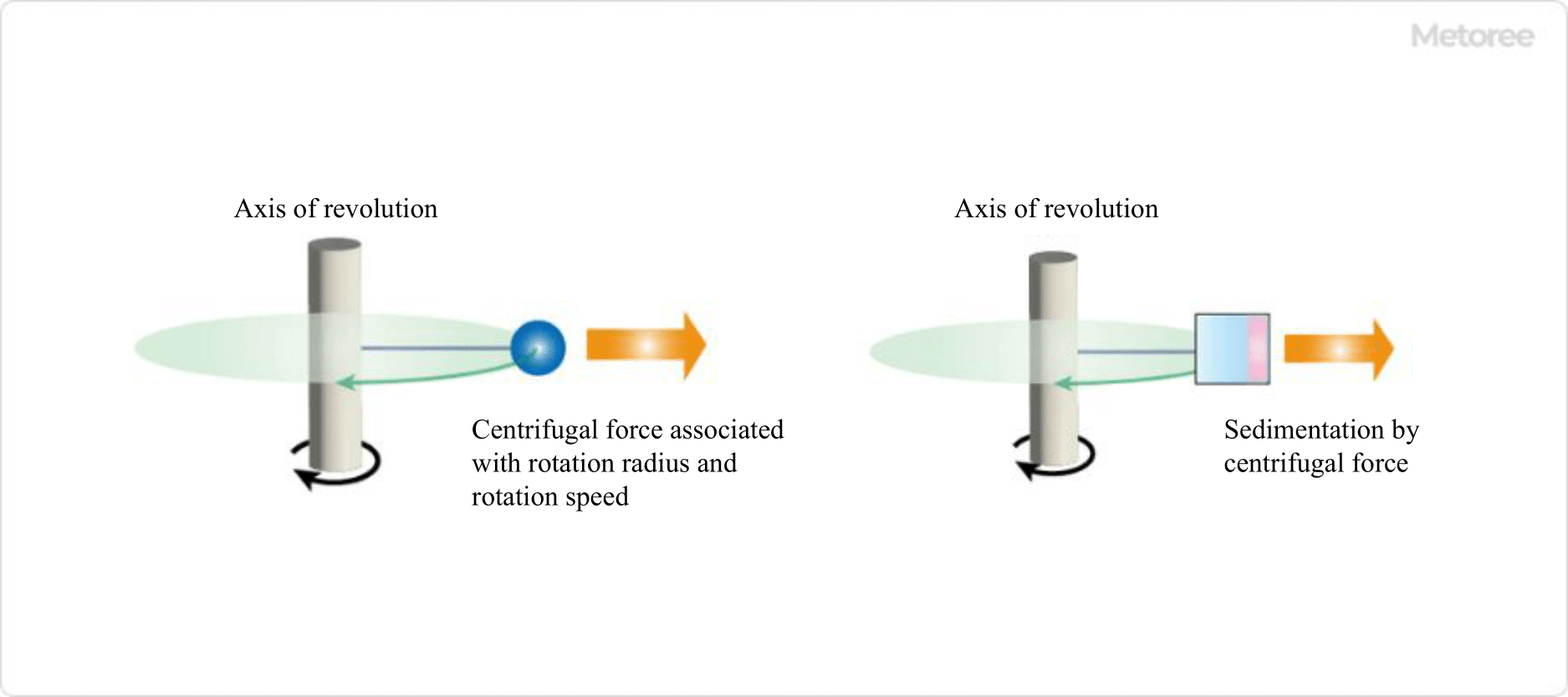
Figure 2. Schematic diagram of centrifugal sedimentation
Liquid-solid or liquid-liquid mixtures with different specific gravities can be separated using gravity by standing still (gravity sedimentation). However, gravity sedimentation is time-consuming because only 1 G acts on it.
A centrifuge is a device that can separate substances faster than gravity sedimentation by applying centrifugal force of several thousand Gs. The magnitude of the centrifugal force depends on the distance of the substance to be separated from the rotation axis and the rotation speed.
1. Experimental Centrifuge
An experimental centrifuge mainly consists of a “rotor” that holds and rotates a sample container, a “drive shaft” that is the axis of rotation, and a “motor” connected to the drive shaft.
The sample container is called a sedimentation tube, and various shapes of containers are used, such as test tubes, spitz tubes, deep-well plates, and microtubes. Therefore, it is usually possible to accommodate a variety of vessels by replacing the rotor section or changing adapters.
When using a centrifuge for laboratory use, the balanced sample must be placed symmetrically concerning the rotor’s axis of rotation. Furthermore, in the case of a swinging rotor, the sample must also be positioned so that the center of gravity in the bucket is on the swing axis.
If not correctly balanced, proper sample separation may not be possible. Many centrifuges are equipped with a function that automatically stops when an imbalance is detected.
2. Industrial Centrifuge
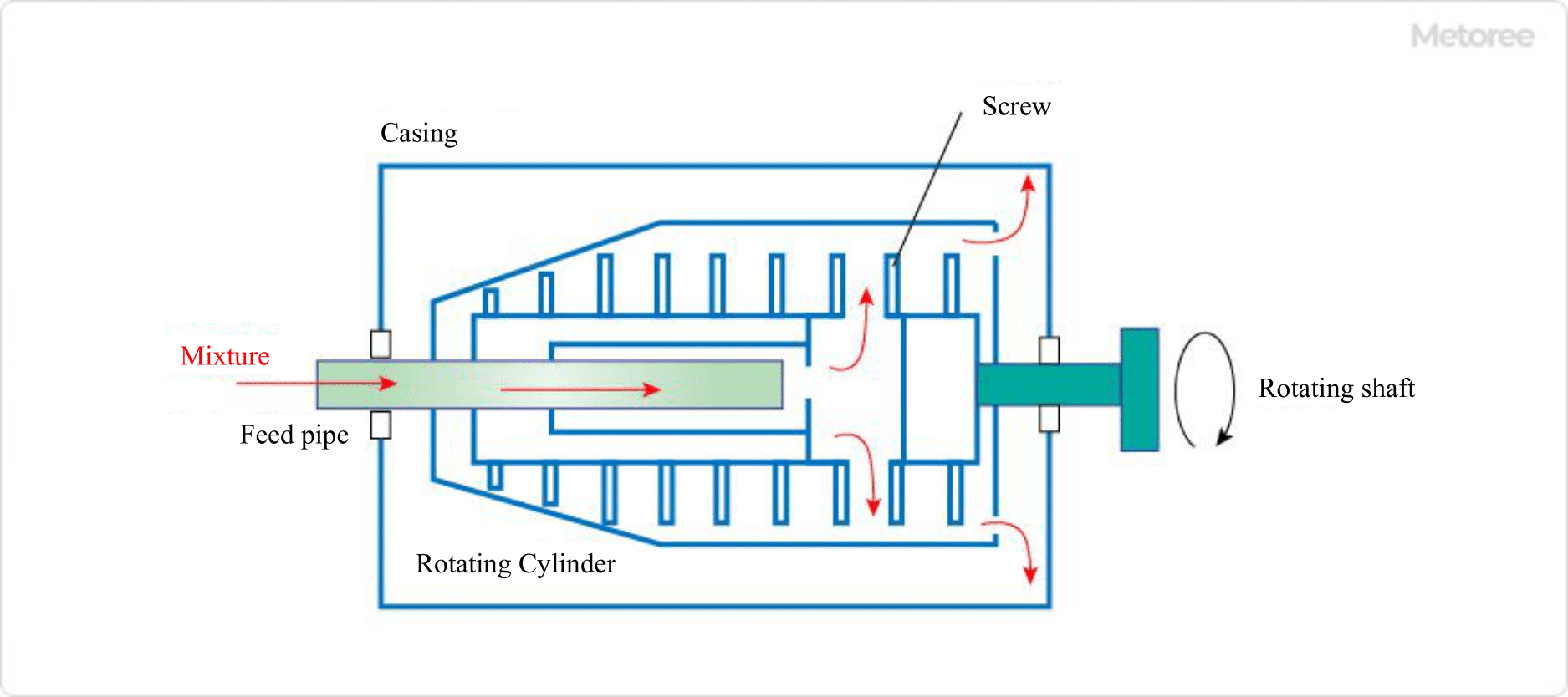
Figure 3. Schematic diagram of a decanter centrifuge
One type of industrial centrifuge larger in scale than a laboratory centrifuge is the decanter type—in a decanter-type centrifuge, rotating the bowl at high speed accomplishes separation. The mixture enters through a feed pipe and is dehydrated by centrifugal force while conveyed by a screw conveyor. The solids and liquid are collected by the casing and discharged outside the machine, respectively.
Types of Centrifuges
Centrifuges can be categorized according to their use.
1. Experimental Centrifuge
Centrifuges for laboratory use come in various sizes, from small to large, and can be divided into tabletop and floor models. Sedimentation tubes range from small ones that can accommodate microtubes with a capacity of 2 ml or less to large ones that can accommodate vessels ranging from several hundred ml to over 1 L in volume.
Due to their construction, they can usually separate multiple samples at once. Regarding handling biological samples, some products are equipped with a mechanism to cool the heat generated by friction between the rotor and air (cooled centrifuges).
2. Industrial Centrifuge
Industrial centrifuges are divided into centrifugal sedimentation machines and centrifugal filtration machines.
- Centrifugal Sedimentation Machine Centrifuge is a type of centrifuge in which the rotor has no filter or holes through which the liquid can pass. Each layer is formed on the wall of the rotor, and the separated liquid is collected by discharging.
- Centrifugal Filtration Machine A basket or similar device with holes in the wall surface of the rotating body is used, and filtering material (cloth or metal filter) is attached to the body. Sedimentation stays in the basket due to the filter material, and water is smaller than the filter material discharged through the holes in the basket.
In addition to the decanter type mentioned above, there is also a cylindrical type. Various products are available to meet the needs of different applications and industries.