What Is an Ultrasonic Instrument?
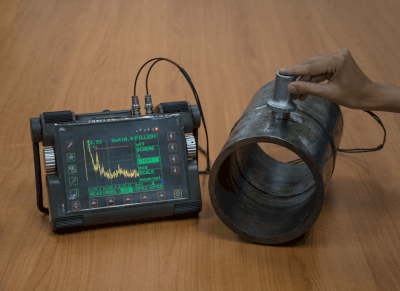
Ultrasonic measuring instruments transmit ultrasonic waves (sound waves with a high frequency that is inaudible to the human ear) to gaseous, liquid, or solid objects and measure various conditions of the objects by utilizing their characteristics, such as reflection and absorption.
Sound waves have characteristics, such as reflection, velocity, and attenuation. The properties of sound waves, such as reflection, velocity, and attenuation, vary depending on the material, concentration, and flow rate of the medium (the substance that mediates the transmission of sound waves). By measuring these changes in sound wave characteristics, it is possible to investigate the properties of the medium.
Uses of Ultrasonic Instruments
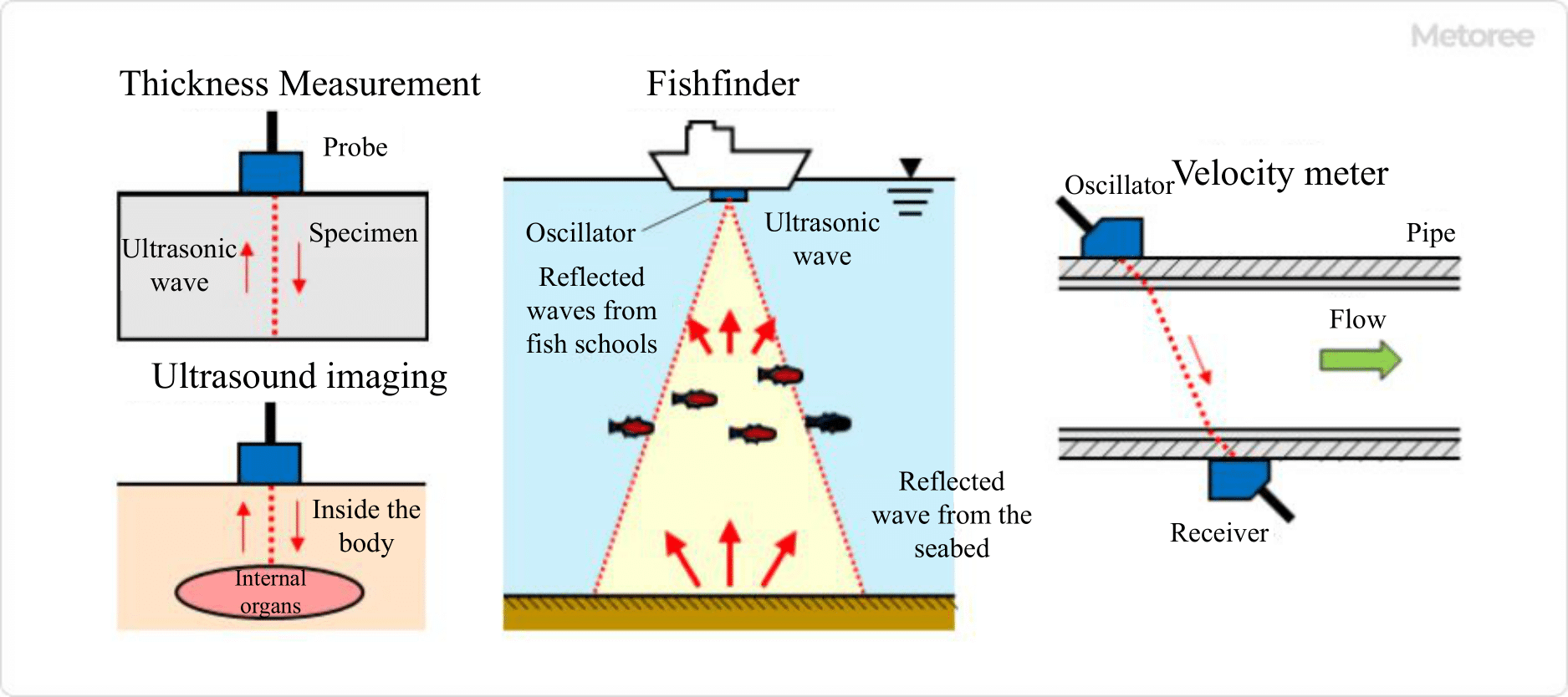
Figure 1. Uses of ultrasonic instrumentation
The objects to be investigated with ultrasonic measuring instruments can be classified into the three states of matter: solid, liquid, gas, and mixed state.
1. Individuals
An example of a solid is the measurement of the thickness of a metal. By irradiating ultrasonic waves into the metal and measuring the time it takes for the waves to reflect back, the thickness of the metal can be determined.
2. Liquid
An example of a liquid is a fish finder. By irradiating ultrasonic waves into the sea and measuring the time it takes for the waves to reflect back from a school of fish or the seafloor, the size and position of the school of fish and the distance to the seafloor can be determined.
3. Gas
An example of a gas is a gas anemometer. Using the fact that sound waves in a gas are affected by the velocity of the gas, the velocity of the gas can be measured.
4. Mixed state
An example of a mixed state is an ultrasound imaging system. Unlike X-ray or CT images, ultrasound is not exposed to radiation, so it is used for the purpose of viewing the fetus.
Principle of Ultrasonic Instruments
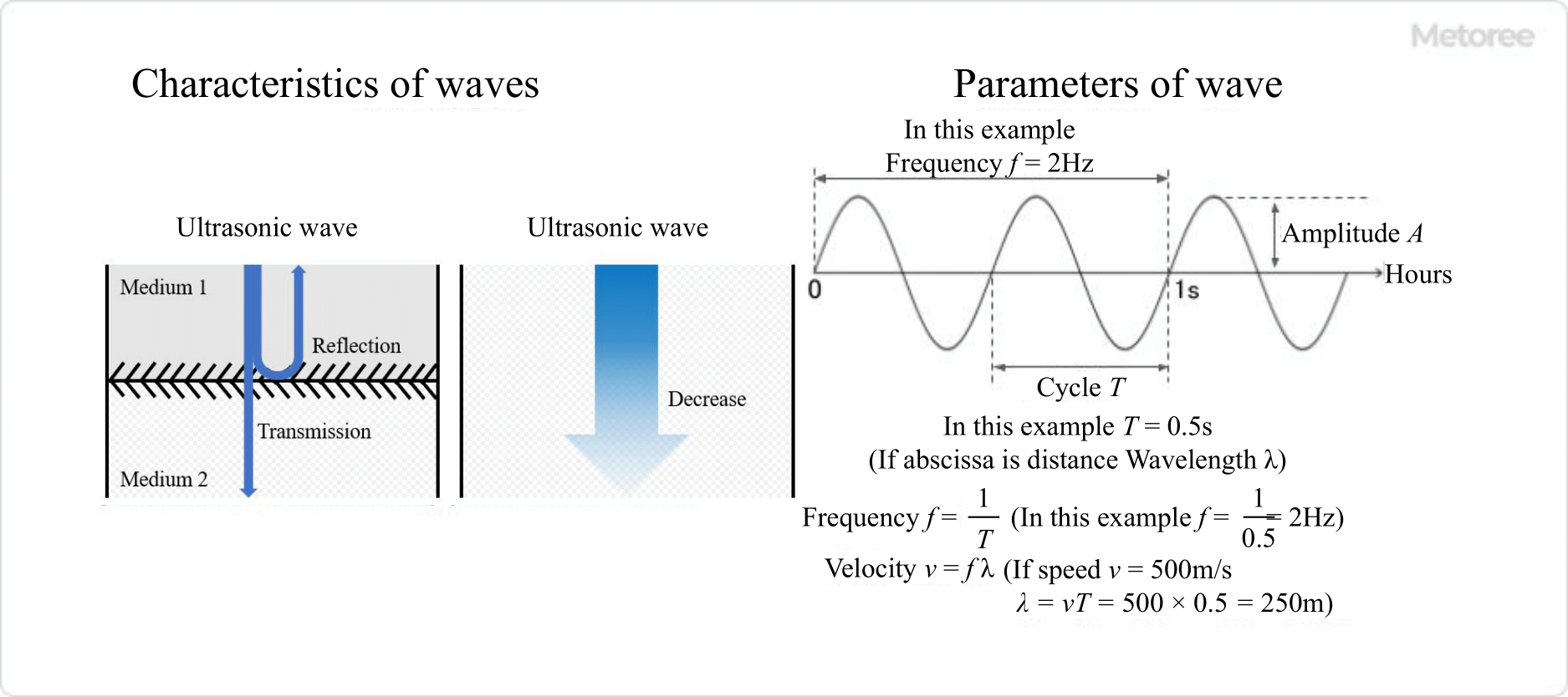
Figure 2. Wave characteristics and parameters
1. Ultrasonic Wave Parameters
In general, “waves” have the following parameters: wavelength, amplitude, frequency, speed, and period.
A sine wave can be represented by the following equation:
y = Asin (2π / T) (x – t / v)
Where y is the position on the vertical axis, A is the amplitude, T is the period, x is the position on the horizontal axis, t is the time, and v is the velocity. The frequency f and wavelength λ can be shown as follows, respectively:
f = 1 / T
λ = Tv
These parameters are also true for sound waves. In the case of sound waves, the above parameters change for the same sound wave in different media.
2. Ultrasonic Measurement
Ultrasonic wave measurement takes advantage of the fact that the characteristics of ultrasonic waves change depending on the medium.
For example, the relationship between sound velocity is gas < liquid < solid. Even in the same solid, the speed of sound varies depending on the substance. By utilizing these characteristics, the following measurements can be made.
1. Individual
Since the speed of sound in a solid under the same conditions is considered to be constant, the thickness of the solid can be measured if the speed of sound and the time it takes for sound waves irradiated in the solid to reflect back are known.
2. Liquid
Assuming that the undersea conditions are almost constant, the position of a school of fish can be estimated from the time it takes for the irradiated ultrasonic waves to be reflected back by the school of fish.
3. Gas
If the medium is moving:
(speed of sound in medium) = (original speed of sound) + (speed of medium)
This relationship is valid. Using this relationship, the velocity of the medium can be measured by measuring the sound velocity in the medium.
4. Mixing State
Sound attenuation is related to attenuation coefficient, distance, and frequency, and the attenuation coefficient varies depending on the medium. Using this relationship, the state of the medium can be estimated by measuring the attenuation coefficient.
Other Information on Ultrasonic Instruments
1. Ultrasonic Instrument for Thickness Measurement
Ultrasonic Instruments measure the thickness of an object by placing a transducer (probe) on one side of the object to be measured.
Ultrasonic waves emitted from the transducer pass through the contact medium, pass through the object, and are reflected back to the transducer on the opposite side of the object. Ultrasonic waves passing through a material have a specific sound velocity value. Ultrasonic thickness gauges measure the thickness of a material based on the intrinsic sound velocity of the material and the time it takes for the ultrasonic waves to be transmitted and then reflected back.
The material to be measured can be metal, glass, plastic, or a variety of other materials. Furthermore, various shapes, from flat to curved, are applicable.
2. How to use Ultrasonic Instrument
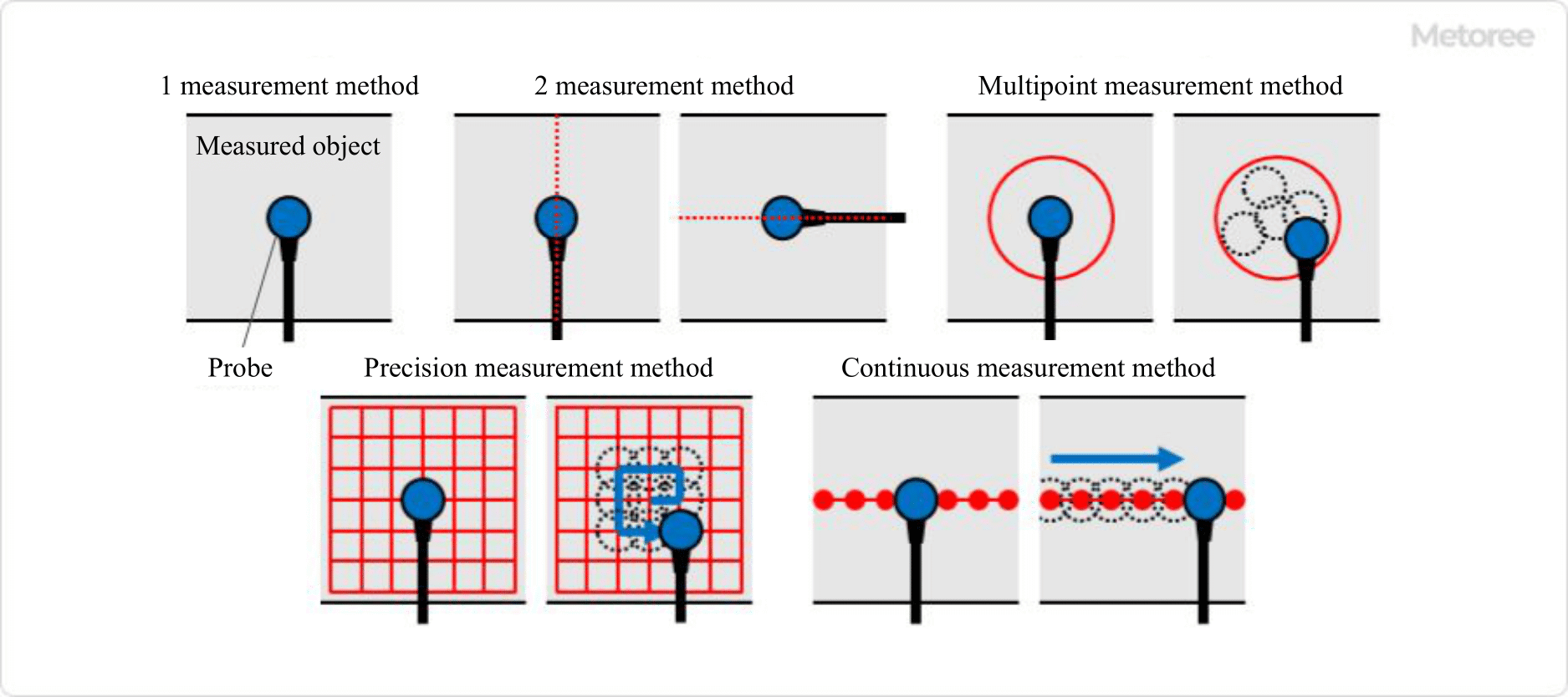
Figure 3. How to use an ultrasonic thickness gauge
The following measurement methods are known to be used with ultrasonic thickness gauges.
1. One-Time Measurement Method
In the one-time measurement method, the probe (transducer) is brought into contact with the object to be measured to measure its thickness. This method is suitable for cases where the corrosion or wall thinning of the object to be measured is slight.
2. Two-Time Measurement Method
The twice measurement method is a measurement method in which the transducer is rotated 90 degrees and the once measurement method is performed twice; the smaller of the two measurements is used as the measurement value, resulting in higher measurement accuracy than the once measurement method.
3. Multi-Point Measurement Method
In the multi-point measurement method, the inside of a circle centered on the measurement point is measured multiple times. The smallest value among multiple measurements is adopted as the measurement value, which is suitable for the measurement of locations where localized corrosion is in progress.
4. Precision Measurement Method
The precision measurement method measures the distribution of thickness reduction due to corrosion at locations where corrosion is expected to have progressed to a certain degree.
5. Continuous Measurement Method
The continuous measurement method is a measurement method used to confirm thickness changes and to infer the state of the back surface based on changes in the cross-sectional thickness of the object to be measured. The thickness change can be checked by measuring with the one-time measurement method at regular intervals or by scanning continuously. In the case of tubular materials, wall thinning may be progressing from the inside, even if there is no abnormality on the outside.
6. Other Measurement Methods
For measuring the thickness of pipe materials, a Ni-oscillator probe is used, and either a one-time or two-time measurement method is used. The direction of contact of the transducer is important during measurement.