Was ist ein Gaschromatograph?
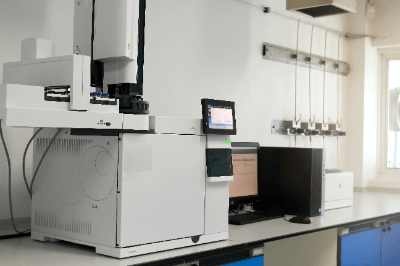
Gaschromatographen sind Geräte, die zur qualitativen und quantitativen Analyse von leicht verdampfbaren Verbindungen eingesetzt werden. Das Verfahren wird üblicherweise als Gaschromatographie abgekürzt und manchmal auch als GC abgekürzt, von der englischen Abkürzung Gas Chromatograph. Zusammen mit der Hochleistungsflüssigkeitschromatographie ist sie eine sehr bekannte Analysetechnik.
Ihr Prinzip besteht darin, dass die Probe verdampft und dann für jede Komponente getrennt wird, um die Art und den Gehalt der Verbindung zu bestimmen. Der größte Vorteil besteht darin, dass auch sehr geringe Konzentrationen flüchtiger Bestandteile analysiert werden können. Die Gaschromatographie wird heute in vielen Bereichen eingesetzt, u. a. in der pharmazeutischen, der Lebensmittel- und der chemischen Industrie und trägt zu den Grundlagen und der Entwicklung von Wissenschaft und Technik bei.
Gaschromatograph ist ein ähnlicher Begriff wie Gaschromatographie und die beiden Ausdrücke werden oft verwechselt, aber ersterer (Gaschromatograph) bedeutet „Versuchsgerät“ und letzterer (Gaschromatographie) „Trennverfahren mit einem Gaschromatographen“, so dass sie unterschiedliche Bedeutungen haben.
Anwendungen von Gaschromatographen
Gaschromatographen werden für die Trennung und Analyse von Verbindungen in Bereichen wie Medizin, Lebensmittel und Chemie eingesetzt. So kann der Gaschromatograph beispielsweise zur Messung der Konzentration gefährlicher Stoffe und zur Analyse der Bestandteile von Gasen, die in Geräten erzeugt werden, eingesetzt werden. Es ist jedoch zu beachten, dass nicht alle Verbindungen analysiert werden können. Aufgrund ihres Prinzips kann die Gaschromatographie im Allgemeinen keine nicht flüchtigen Verbindungen mit einem Siedepunkt von 400 °C oder mehr oder instabile Verbindungen, die sich bei hohen Temperaturen zersetzen, analysieren. Anorganische Metalle, Ionen und stark adsorbierbare Verbindungen sind aus demselben Grund ebenfalls schwer zu analysieren und müssen vor der Analyse überprüft werden.
Funktionsweise der Gaschromatographie
Die Funktionsweise der Gaschromatographie ist sehr einfach und besteht aus drei Schritten:
1. Die Probe wird durch Hitze verdampft
2. Trennung der Komponenten durch Säulenchromatographie
3. Nachweis der Komponenten durch eine geeignete Methode
Zunächst wird die flüssige Probe thermisch verdampft. Die verdampften Bestandteile werden mit einem Trägergas zur Säule transportiert. Die verdampften Komponenten werden adsorbiert und auf der stationären Phase (flüssige Phase) in der Säule verteilt, wo sie Komponente für Komponente getrennt werden und die Säule durchlaufen. Die Geschwindigkeit, mit der sich die Verbindungen durch die Säule bewegen, ist je nach Verbindung unterschiedlich, so dass die sich am schnellsten bewegenden Komponenten die Säule in dieser Reihenfolge verlassen. Jede abgetrennte Komponente wird vom Detektor als Peak registriert und durch den Vergleich der Retentionszeit und der Peakfläche mit denen des Standards können Art und Konzentration der Probe bestimmt werden.
Das Hauptmerkmal dieser Analysemethode besteht darin, dass sie für die Analyse flüchtiger Komponenten verwendet werden kann, die nicht durch Hochleistungsflüssigkeitschromatographie getrennt, identifiziert und quantifiziert werden können.
Stationäre Phasen in der Gaschromatographie
Die Wahl der stationären Phase, die in der Gaschromatographiesäule verwendet wird, ist sehr wichtig, da die Trennung und Analyse schwierig ist, wenn nicht eine Säule mit der geeigneten stationären Phase entsprechend den Eigenschaften der Komponenten verwendet wird.
Die Säulen lassen sich je nach Polarität der stationären Phase grob in zwei Typen einteilen: unpolare Säulen und hochpolare Säulen.
Unpolare Säulen
Eine unpolare Säulen ist eine Säule, in der eine Verbindung mit geringer Polarität als stationäre Phase verwendet wird. In solchen Säulen werden Verbindungen mit geringer Polarität stark in der flüssigen Phase mit geringer Polarität als stationäre Phase zurückgehalten, was zu langsameren Migrationsraten und folglich zu einer höheren Trennleistung führt. Daher sind diese Säulen für die Analyse von unpolaren Verbindungen geeignet. Unpolare Säulen sind auch hitzebeständiger als hochpolare Säulen und können im Allgemeinen bis zu 350 °C verwendet werden.
Hochpolare Säulen
Hochpolare Säulen sind solche, in denen hochpolare Verbindungen als stationäre Phase verwendet werden. In solchen Säulen werden hochpolare Verbindungen stark zurückgehalten, was ihre Migrationsrate verlangsamt und zu einer hohen Trennleistung führt. Sie sind daher für die Analyse hochpolarer Verbindungen geeignet. Zu beachten ist auch, dass hochpolare Säulen eine geringe Hitzebeständigkeit aufweisen, im Allgemeinen mit einer Obergrenze von etwa 250 °C.
Trennung von hochpolaren organischen niedermolekularen Verbindungen durch Derivatisierung
Hochpolare organische Verbindungen mit niedrigem Molekulargewicht sind aufgrund ihrer geringen Flüchtigkeit im Allgemeinen schwer zu trennen und mit Hilfe der Gaschromatographen zu analysieren. Je nach Struktur der Zielverbindung kann es jedoch möglich sein, sie durch chemische Methoden in eine flüchtige Verbindung zu derivatisieren, so dass eine gaschromatographische Trennung möglich wird. Derartige Derivatisierungstechniken werden daher häufig für die Trennung und Analyse von Verbindungen eingesetzt, die sich nur schwer durch Hochleistungsflüssigkeitschromatographie trennen lassen. Ein Beispiel hierfür ist die TMS-Derivatisierung von Zuckern und Oligosacchariden, also von Verbindungen mit vielen Hydroxylgruppen, mit anschließender GC-Analyse.
Detektoren in der Gaschromatographie
Detektoren weisen die von der Gaschromatographen-Säule getrennten Komponenten nach und werden für unterschiedliche Zwecke eingesetzt:
Flammenionisationsdetektor (FID)
Dieser detektiert ionisierte Verbindungen, die bei der Verbrennung organischer Verbindungen in einer Wasserstoffflamme aus Luft und Wasserstoff entstehen. Es können fast alle organischen Verbindungen nachgewiesen werden und die Empfindlichkeit ist extrem hoch.
Wärmeleitfähigkeitsdetektor (TCD)
Dieser detektiert Komponenten durch Messung der Temperaturänderung des Glühfadens auf der Grundlage des Unterschieds in der Wärmeleitfähigkeit zwischen dem Trägergas und der betreffenden Komponente. Sowohl anorganische als auch organische Komponenten können zerstörungsfrei nachgewiesen werden.
Flammenphotometrischer Detektor (FPD)
Dieser detektiert einzelne Komponenten durch Verstärkung des von dem Element durch Verbrennung erzeugten Lichts einer bestimmten Wellenlänge mit Hilfe einer Photomultiplier-Röhre und Umwandlung seiner Intensität in ein elektrisches Signal. Schwefel, Phosphor und zinnorganische Verbindungen werden nachgewiesen.
Schwefel-Chemilumineszenz-Detektor (SCD)
Dieser detektiert Schwefelkomponenten durch Messung des Lichts, das erzeugt wird, wenn chemische Spezies (hauptsächlich SO), die aus Schwefelverbindungen umgewandelt werden, durch Ozon angeregt werden und dann mit Hilfe einer Photomultiplier-Röhre in ihren Grundzustand zurückkehren.
Stickstoff-Phosphor-Detektor (NPD)
Dieser Detektor eignet sich für die Messung organischer Stickstoffverbindungen. Die Wasserstoffflamme enthält Rubidiumsalze, die beim Eintritt von phosphor- oder stickstoffhaltigen Verbindungen in die Flamme zu CN- und PO- Ionen ionisiert werden, die dann nachgewiesen werden.
Elektroneneinfangdetektor (EECD)
Dieser wird für den selektiven Nachweis von hochneoelektronischen Verbindungen wie Organohalogenverbindungen, metallorganischen Verbindungen und Nitroverbindungen verwendet. Die Komponenten werden durch Ablesen von Änderungen der Spannungswerte nachgewiesen, um den im Kollektor gesammelten Ionenstrom konstant zu halten.
Gaschromatographen-Massenspektrometer
Ein Gaschromatographen-Massenspektrometer ist ein Gerät, das über eine Schnittstelle einen Gaschromatographen und ein Massenspektrometer miteinander verbindet. Eine Probe, die mehrere Komponenten enthält, wird durch den Gaschromatographen zunächst in einzelne Komponenten aufgetrennt. Anschließend misst das Massenspektrometer die MS-Spektren der einzelnen Komponenten zur qualitativen Bestimmung der Komponenten und anschließend zur quantitativen Bestimmung anhand der spektralen Intensität der Ionen.
Gaschromatographen-Massenspektrometer eignen sich für die Zusammensetzungsanalyse verschiedener Öle, die qualitative Analyse organischer Lösungsmittel, die qualitative und quantitative Analyse von Gasen und durch Pyrolyse erzeugten Gasspezies aus verschiedenen Materialien, die Analyse flüchtiger organischer Verbindungen (VOC) in Luft und Wasser usw.