Was ist eine Dispersionsfarbe?
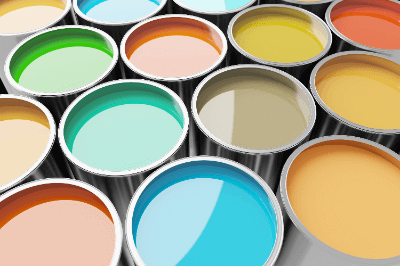
Dispersionsfarben sind Farben, bei denen die Nachteile herkömmlicher Öl- und Wasserfarben durch die Emulsionstechnik verbessert werden.
Sie sind nicht brennbar und ermöglichen eine einfache Einstellung der Viskosität und das Mischen von Zusatzstoffen. Bei der Emulgierung werden Flüssigkeiten, die sich nicht miteinander vermischen, also Komponenten auf Öl- und Wasserbasis, gemischt, indem die eine in feine Partikel zerlegt und diese dann in der anderen dispergiert werden, um einen Mischzustand herzustellen.
Die Emulsionstechnologie wurde erstmals 1927 in den USA eingesetzt, als synthetischer Kautschuk erfolgreich aus Butadien-Emulgator-Dispersionen hergestellt wurde.
Anwendungen von Dispersionsfarben
60 % der Dispersionsfarben werden in der Architektur eingesetzt. Der Grund dafür ist, dass sie im Vergleich zu Farben auf Ölbasis weniger flüchtige organische Verbindungen enthalten und zur Vermeidung des Sick-Building-Syndroms beitragen. Dispersionsfarben auf Wasserbasis lassen sich problemlos mit Wasser verdünnen, die Viskosität kann mit Verdickungsmitteln leicht eingestellt werden und sie lassen sich hervorragend spritzen. Sie lassen sich selbst auf stark hygroskopischen Untergründen wie Mörtel leicht auftragen und Pigmente und Additive können einfach gemischt werden.
Duroplastische Acrylemulsionen werden für Metallbeschichtungen verwendet. Sie werden nach dem Lackieren eingebrannt, wodurch eine Vernetzungsreaktion ausgelöst wird, die die Härte, die Haftung und die Beständigkeit gegen Wasser und Lösungsmittel verbessert.
Unter rauen Bedingungen werden manchmal wärmehärtende Acrylemulsionen für Metallbeschichtungen verwendet, z. B. Acrylate mit ausgezeichneter Wetter-, Wasser- und Alkalibeständigkeit. Das Einbrennen erfolgt nach dem Anstrich, um eine Vernetzungsreaktion herbeizuführen, die die Härte, die Haftung und die Beständigkeit gegen Wasser und Lösungsmittel verbessert.
Funktionsweise der Dispersionsfarben
Zunächst werden die in Wasser dispergierten Emulsionspartikel durch den Anstrich in enge Nähe zueinander gebracht und dicht aneinander gepackt. Wenn das Wasser verdunstet, wird die Schutzschicht auf den Partikeloberflächen zerstört und die Vernetzung auf den freiliegenden Polymeroberflächen schreitet voran, was allmählich zur Adhäsion führt. Die aneinander haftenden Teilchen bilden einen gleichmäßigen Film, der zu einer pigmentgefüllten Beschichtung wird.
Liegt die Trocknungstemperatur unter der Mindestfilmbildungstemperatur, werden die Teilchen nicht verformt und haften nicht, was zu einem Pulver mit unzureichender Festigkeit führt. Daher werden Hilfsmittel hinzugefügt, um die Reaktion zu erleichtern.
Da viele Emulsionen nach dem Gefrieren irreversibel sind, werden sie durch den Zusatz von Ethylenglykol als Gefrierstabilisator oder durch Copolymerisation hydrophiler Monomere stabilisiert. Auch Dispergiermittel, Verdickungsmittel, Stabilisatoren und Antipilzmittel werden je nach Bedarf zugesetzt, um die Qualität der Farbe während der Lagerung zu stabilisieren.
Die mechanische Festigkeit ist nach einer gewissen Zeit oft höher als unmittelbar nach der Filmbildung, da die Polymerdiffusion nach der Filmbildung weitergeht.
Arten von Dispersionsfarben
Dispersionsfarben lassen sich je nach verwendetem Lösemittel grob in Öl- und Wasserfarben unterteilen. Bei Farben auf Ölbasis werden organische Lösungsmittel verwendet, während bei Farben auf Wasserbasis Wasser als Lösungsmittel eingesetzt wird.
Dispersionsfarben können ebenfalls auf Lösungsmittel- oder Wasserbasis hergestellt werden. Farben, bei denen Wasserpartikel in einem ölbasierten Lösungsmittel schwimmen, werden als lösungsmittelbasierte Farben bezeichnet, während Farben mit ölbasierten Partikelbestandteilen in einer Wasserlösung als wasserbasierte Farben bezeichnet werden.
Organische Lösungsmittel, die in Ölfarben verwendet werden, können für die Umwelt und die menschliche Gesundheit schädlich sein und die Hersteller haben sich auf die Verbesserung von Wasserfarben konzentriert, indem sie Tenside entwickelt haben, also Stoffe, die sie im emulgierten Zustand stabilisieren. Infolgedessen wurden Dispersionsfarben entwickelt, in denen Pigmente auf Ölbasis dispergiert sind, und heute sind Dispersionsfarben auf Wasserbasis der Mainstream.
Auswahl von Dispersionsfarben
Die wichtigste Eigenschaft von Dispersionsfarben ist die Aushärtung. Die Aushärtung ist der Prozess, bei dem das Wasser in der aufgetragenen Farbe mit der Zeit verdunstet und einen harten Anstrichfilm bildet. Je nach Art der Aushärtung und der Festigkeit des Anstrichfilms kann man zwischen Schmelzhärtung und Reaktionshärtung auf Wasserbasis unterscheiden.
Bei der Schmelzhärtung kommen dispergierte Partikel zusammen, verschmelzen und härten durch die Verdunstung von Wasser oder Öl aus. Da die Partikel selbst nur miteinander verschmolzen sind, ist die Haftung des Beschichtungsfilms relativ schwach.
Bei der Reaktionshärtung auf Wasserbasis hingegen verkleben die Partikel und der mit den Partikeln vorab vermischte Reaktant, wenn das Wasser oder Öl verdunstet. Dies wird als Vernetzungsreaktion bezeichnet. Die durch die Vernetzungsreaktion hervorgerufene Aushärtung lässt die dreidimensionale Struktur zwischen den Partikeln verschmelzen, was zu einem festeren Farbfilm führt. Reaktionshärtende Dispersionsfarben auf Wasserbasis, die ein Reaktionsmittel enthalten, werden empfohlen, wenn eine lange Haltbarkeit der Farbe erforderlich ist.
Weitere Informationen zu Dispersionsfarben
1. Eigenschaften von Dispersionsfarben
Dispersionsfarben haben eine geringe Auswirkung auf den menschlichen Körper. Nach dem Auftragen von Ölfarben verdampfen die Lösemittelbestandteile und der Farbfilm härtet aus. Wenn sie eingeatmet werden, kann es zu Übelkeit und sogar zu Bewusstlosigkeit kommen. Die geringe Menge an Lösemittelbestandteilen, die nach dem Trocknen zurückbleibt, kann auch zu gesundheitlichen Problemen wie dem Sick-Building-Syndrom führen, während Dispersionsfarben keine negativen Auswirkungen auf die Gesundheit haben, da nur Wasser verdunstet.
Allerdings ist die Haftung des Farbfilms im Vergleich zu Farben auf Ölbasis schlecht. Da die Farbe in Wasser suspendiert ist, ist sie hydrophiler als Ölfarben und hat den Nachteil, dass die Farbe in Bereichen, in denen sie Regenwasser ausgesetzt ist, wie z. B. an Außenwänden, zum Abblättern neigt. Um diesen Nachteil auszugleichen, muss man sich etwas einfallen lassen, z. B. indem man mehrere Farbschichten aufträgt.
2. Qualität der Farbe
Die Anstrichsorten unterscheiden sich je nach Haltbarkeit. Acryl-, Urethan-, Silikon- und Fluorfarben sind die haltbarsten und teuersten, in dieser Reihenfolge. Von diesen bietet Silikonfarbe das beste Verhältnis zwischen Haltbarkeit und Preis.
Silikonfarbe wird bei vielen Anstrichprojekten verwendet und ist derzeit die gängigste Farbe. Fluorfarben werden verwendet, wenn die Haltbarkeit wichtig ist, während Acryl- und Urethanfarben verwendet werden, wenn die Anschaffungskosten niedriger sind als die Haltbarkeit.
- Acryllacke
Am billigsten, extrem wenig haltbar und selten für Außenwände verwendet.
- Urethanfarbe
Geringe Kosten und geringe Haltbarkeit. Geringste Qualität der für Außenwände verwendeten Farbe
Silikonfarbe: kostengünstigste in Bezug auf Preis und Lebensdauer, derzeit am weitesten verbreitet.
- Fluorierte Farbe
Längere Lebensdauer, aber teurer.
3. Sick-Building-Syndrom
Das Sick-Building-Syndrom ist ein allgemeiner Begriff für Gesundheitsprobleme, die vermutlich auf die Luftverschmutzung in Innenräumen durch flüchtige organische Verbindungen zurückzuführen sind, die in Bau- und Innenraummaterialien enthalten sind, da die Häuser immer luftdichter und besser isoliert werden.
Baustoffe und Materialien, die einen hohen Gehalt an flüchtigen organischen Verbindungen wie Formaldehyd und Toluol enthalten, wurden für das Syndrom verantwortlich gemacht.